Setting up a pharmaceutical manufacturing plant in India is no small feat. It's not just about throwing money at the venture—though, let's be real, the costs can be hefty. We're talking hundreds of thousands to millions of dollars, depending on your aspirations and the scale you're aiming for. So, where does all this money go?
Your first big-ticket item is the land and infrastructure. Picking a strategically located site is crucial, and the cost for this can vary wildly based on location. Urban areas generally demand a steeper price but offer better logistics. Then there's the task of constructing or refurbishing facilities to meet industry standards.
Don't forget about the regulatory maze you'll need to navigate. The Indian government has specific guidelines for pharmaceutical manufacturing that you absolutely must follow. Compliance isn't just a box to tick—it's a continuous process that starts with securing the necessary licenses and approvals.
- Initial Investment Breakdown
- Location and Infrastructure
- Regulatory Compliance
- Equipment and Technology
- Operational Costs
Initial Investment Breakdown
Planning the finances for a pharmaceutical manufacturing plant in India begins with understanding the core costs involved. There's no unicorn answer here—the amount can swing from a few crores to hundreds, based on the plant size and product specialization. Here’s what typically eats up your budget:
1. Land and Infrastructure
Land costs can vary, especially between urban and rural settings. In cities, you're likely to pay a premium, which could start from INR 1 crore for a reasonable plot. Then comes building the plant, which needs to comply with rigorous industry norms. Budgeting for construction and utilities could add another INR 5-10 crores.
2. Equipment Procurement
The right equipment is essential for production efficiency and product quality. Initial setup for machinery might see costs around INR 3-8 crores depending on whether you're focusing on tablets, syrups, or other forms. Keep in mind that importing top-of-the-line machinery could inflate these figures.
3. Compliance and Licensing
Before your plant can start churning out products, you'll need various licenses and registrations—each carrying its own fee. Obtaining Good Manufacturing Practice (GMP) certification is a must, and that could mean an initial outlay of INR 10-20 lakhs.
4. Staffing and Training
Skilled labor is another key component. From experienced chemists to plant operators, budgeting for salaries is crucial. Initial staff training and recruitment might cost around INR 50 lakhs initially, assuming a small to mid-sized workforce. Don't forget ongoing operational costs in your plans.
Investment Item | Estimated Cost (INR) |
---|---|
Land and Infrastructure | 6-11 Crores |
Equipment Procurement | 3-8 Crores |
Compliance and Licensing | 10-20 Lakhs |
Staffing and Training | 50 Lakhs |
The total starting investment depends on several factors and can reach well over INR 10 crores. Consider these costs carefully to ensure your investment aligns with your business goals in the pharma industry.
Location and Infrastructure
When you're setting up a pharmaceutical manufacturing plant, one of the first questions is, 'Where do we build?' Picking the right location isn't just about finding a spot on the map—there's a lot more to it.
Firstly, consider proximity to resources like raw materials and skilled labor. Being close to these means fewer headaches down the road. Many pharma companies in India gravitate towards hubs like Hyderabad or Ahmedabad, thanks to their developed industrial infrastructure and support from local authorities.
You'll also need to think about logistics. Easy access to transportation can cut down distribution costs substantially, so a location near highways or ports can be a smart choice. But remember, land prices can fluctuate hugely depending on these factors. An industrial area might be budget-friendly compared to prime real estate in a city center.
Building the Site
Once you've nailed down a location, it's time to think about the infrastructure itself. The initial build or renovation involves ensuring your facility meets certain standards. You'll need buildings that are suitable for large-scale production while also being compliant with safety and health regulations.
Utilities like stable electricity supply, water, and waste management systems are non-negotiable. These aren't just nice-to-haves; they're essentials to keep operations smooth and efficient.
Cost Considerations
The costs here can add up quickly. You might be looking at land costs ranging from INR 50 lakh to several crores, depending on the location and size. Construction can easily double this, especially if you're opting for high-tech equipment and sustainable systems.
Here's a quick breakdown to consider:
- Land Acquisition: Costs vary widely depending on proximity to urban centers.
- Construction: This includes structural work and installing essential facilities.
- Utilities Setup: Ensure a reliable supply and setup of all basic services.
Choosing the right location and setting up a robust infrastructure can make or break your plant setup costs—and that ultimately affects your bottom line. So, plan wisely!
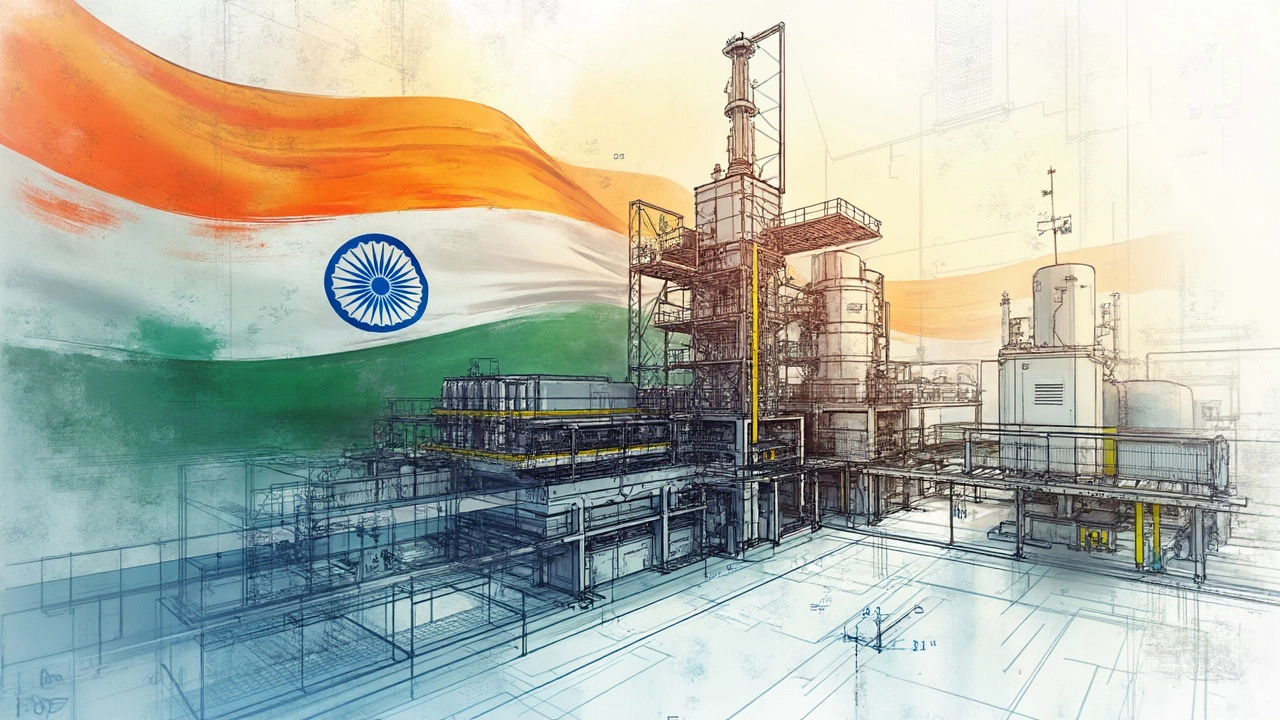
Regulatory Compliance
Regulatory compliance is a big deal when setting up a pharmaceutical manufacturing plant in India. It's not a one-time thing—it's an ongoing commitment. First off, you'll need to get clearance from the Central Drugs Standard Control Organization (CDSCO). This is the national regulatory authority, and trust me, playing by their rules is crucial.
Licensing and Approvals
Getting your plant up and running starts with securing a manufacturing license under the Drugs and Cosmetics Act. This involves submitting applications and detailed documentation regarding your facilities, process, and safety protocols. Expect a few inspections before you get the green light.
GMP Certification
Once you’re past licensing, you'll need to adhere to Good Manufacturing Practices (GMP). This is vital for ensuring product quality and safety. Failure to comply can mean hefty fines or worse, shutting down operations.
Import and Export Regulations
If you're eyeing foreign markets, remember that regulatory compliance doesn't stop at Indian borders. You'll need to follow international regulations such as the U.S. FDA or the EU's EMA standards. This often requires additional documentation and certifications.
Continuous Monitoring
Regulations aren't static. You're required to keep up with changing laws and standards, which means continuous monitoring and updates to your processes. Hiring a dedicated team or consulting with experts can save you a lot of headaches down the line.
In short, keeping on top of regulatory compliance is essential for a successful pharma industry venture in India. It's about being diligent and proactive, ensuring your plant operates smoothly and legally.
Equipment and Technology
When it comes to establishing a pharmaceutical manufacturing plant, investing in the right equipment and technology is essential. This ensures efficiency, productivity, and, most importantly, compliance with health regulations. You'll need a mix of standard and specialized machinery, which can vary significantly in price based on their capabilities and the scale of your operations.
The range of equipment needed includes mixing vessels, dryers, coating machines, and packaging lines, depending on what form of medication you plan to produce. For instance, if you're looking at tablet manufacturing, a fluid bed dryer and high-speed tablet press are must-haves. These offer precision and reliability, critical for maintaining product quality.
High-Tech Driven Innovation
The pharma sector is rapidly adopting cutting-edge technology. Automation and AI integration are game-changers, allowing for more efficient processes and reduced human error. Implementing a robust management software can help monitor production levels, manage inventories, and ensure compliance in real time.
In the words of Dr. Amit Bhatt from PharmaPro Ltd, "
Investing in advanced technology is no longer optional. It sets the pace for operational excellence and can significantly reduce long-term costs."
Cost Considerations
While technology can streamline processes, it also comes with its price tag. A complete setup for a pharmaceutical manufacturing plant might range from ₹10 million to ₹50 million, depending on how tech-intensive your setup is. Remember to account for maintenance and updates, which are crucial for long-term sustenance.
Looking to cut costs? Consider leasing some equipment or purchasing second-hand from reliable sources. Just ensure they're up to current standards, as you'll need to pass rigorous inspections.
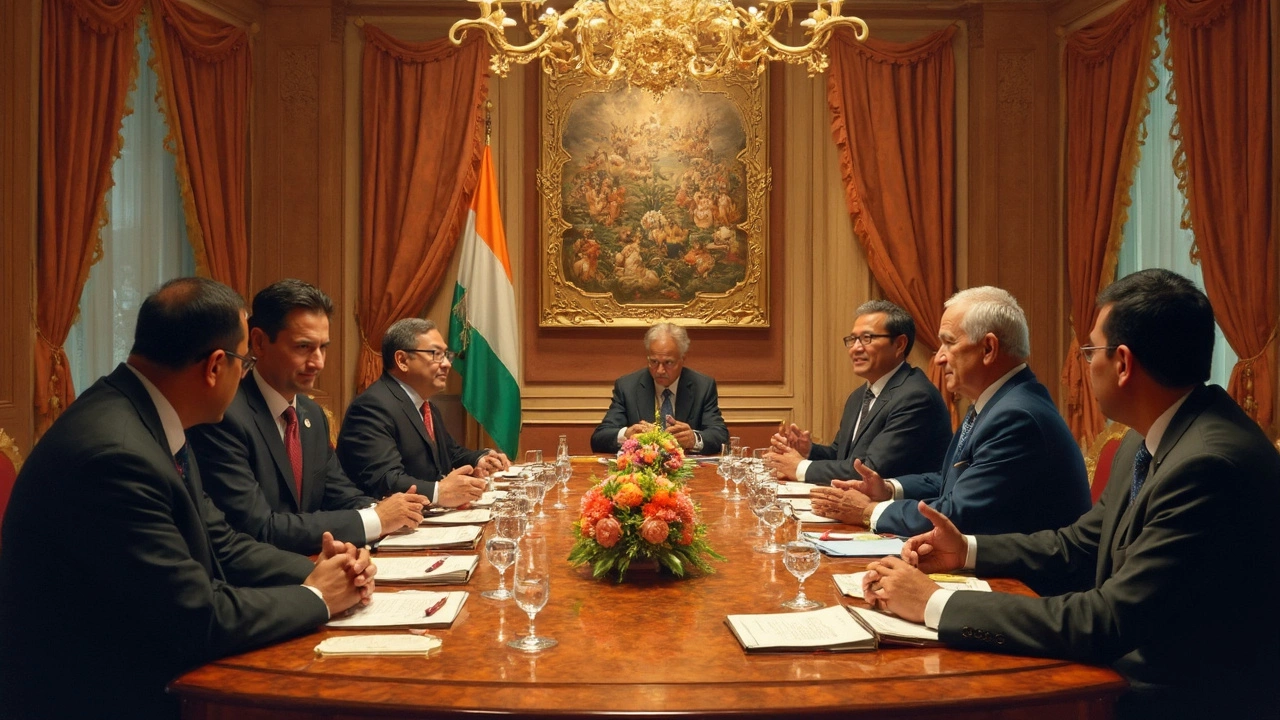
Operational Costs
Once you get past the setup phase, you'll jump into the day-to-day expenses, commonly known as operational costs. It's essential to understand these when setting up a pharmaceutical manufacturing facility in India. This isn't just about keeping things running, but about optimizing and ensuring every penny counts.
Labor Costs
Labor is a major component. Even though labor rates in India are competitive, you're looking at salaries for skilled lab workers, engineers, and administrative staff. Depending on the size, you might employ anywhere from 50 to 500 people. Remember, retention and training are critical to maintaining productivity and quality.
Material and Production Costs
Raw materials can be another big chunk of your budget. Think about everything from chemicals to packaging materials. Keeping an eye on supply chain logistics is key here to avoid disruptions or price hikes impacting your production.
Utilities and Maintenance
You've also got utilities—electricity, water, waste management—these can add up fast. Efficient energy use isn't optional; it's a must if you want to keep costs in check. Plus, regular maintenance of equipment reduces downtime and keeps things ticking like clockwork.
Compliance and Quality Control
Don’t slack off on quality control and regulatory compliance. Testing, audits, and certifications aren't just upfront expenses; they're ongoing ones. Yet, skimping here risks your business and reputation. It's a crucial part of keeping your pharma industry standards top-notch.
Marketing and Distribution
Last but not least, consider costs related to marketing and distribution. Getting your product to market is just as important as making it. This includes engaging with distributors, promotional material, and market research to hit the ground running.
To give you a snapshot of these costs in numbers:
Expense Category | Estimated Monthly Cost (INR) |
---|---|
Labor | 500,000 - 2,000,000 |
Materials | 700,000 - 3,500,000 |
Utilities | 200,000 - 800,000 |
Compliance | 150,000 - 600,000 |
Marketing | 100,000 - 500,000 |
Keeping track of these expenses and continuously optimizing them can make the difference between thriving or just surviving in the pharma manufacturing world.