Chances are, if you’ve played a video game or used the latest AI, you’ve relied on chips designed by Nvidia—but made by someone else. Nvidia doesn’t build its own chips. Instead, it buys manufacturing muscle from TSMC, the powerhouse in Taiwan that practically runs the show when it comes to advanced semiconductors. That might sound crazy: the world’s top chip designer doesn’t own a single factory.
Why does this matter? If you wanted to make a top-tier GPU or a powerful AI processor, you’d face a huge problem: building your own chip factory takes years and billions of dollars. TSMC figured that out early. Now, even giants like Nvidia line up for TSMC’s cutting-edge chip tech because it’s way too expensive and tricky to do it solo. Most of Nvidia’s hottest products, from the RTX graphics cards to the H100 chips powering TikTok and ChatGPT, are all rolled out from TSMC’s production lines.
This isn’t just a nerdy detail—it shapes where new tech gets built, which countries can compete, and why chip shortages mess up everything from laptops to cars. Ask anyone trying to source electronics in India, and you’ll hear about the headaches caused by a few key companies steering the entire market. India’s big talk about becoming a chip hub might change the game—or just add to the noise. Understanding this Nvidia-TSMC connection puts you right in the middle of the world’s most high-stakes tech drama.
- Why Does Nvidia Rely on TSMC?
- How Does This Partnership Work?
- What’s the Impact on Electronics Manufacturing?
- India’s Role: Big Dreams or Just Buzz?
- Tips for Navigating the Chip Supply Chain
Why Does Nvidia Rely on TSMC?
Here’s the deal: Nvidia is a master at designing chips, but it doesn’t actually own any chip factories. Instead, it goes straight to TSMC (TSMC stands for Taiwan Semiconductor Manufacturing Company), which has a tight grip on the world’s most advanced chip production. Nvidia uses TSMC’s factories because building your own chip foundry is way out of reach for most companies—even tech giants. We’re talking about investments in the tens of billions and a minimum wait of three to five years just to get started.
TSMC’s not just anybody—they’ve got the edge when it comes to making the tiniest, most powerful chips on the planet. Their 5-nanometer and 3-nanometer processes are things barely anyone else can do. Nvidia’s best-selling GPUs and AI chips need this kind of tech. Trying to make these in an older or less advanced factory would slow everything down, jack up the costs, or just make weaker products. That’s the last thing Nvidia wants when it’s competing against AMD and Intel.
Take a look at how dominant TSMC is when it comes to real-world orders from big name chip designers:
Company | Percent of TSMC’s Revenue (2024) |
---|---|
Nvidia | 11% |
Apple | 23% |
AMD | 7% |
With those numbers, it’s no wonder Nvidia is glued to TSMC. Most other places—like Samsung or Intel’s foundry—just can’t match TSMC on the newest tech and pure scale. Nvidia knows this and locks in massive orders way ahead of time to make sure it doesn’t get stuck in a supply crunch (like what happened during the pandemic—remember those endless waits for new graphics cards?).
Bottom line: Using TSMC lets Nvidia focus on chip design, not factory headaches. That’s how they pump out world-beaters without the baggage of running giant fabs.
How Does This Partnership Work?
Here’s the deal: Nvidia cooks up the designs for insanely complex chips. TSMC is pure production—they don’t design, but they’re the best at turning tiny blueprints into real-world silicon. Nvidia sends its final chip designs over, TSMC puts them through their ultra-high-tech foundries, and what rolls out is a product with millions (or billions) of transistors packed into an area smaller than your fingernail.
This isn’t a casual one-off order. Nvidia is one of TSMC’s largest customers, competing with Apple for priority when new processes launch. For instance, TSMC’s 4-nanometer and 5-nanometer plants are often running at full tilt, and both Apple and Nvidia have early access. Nvidia’s biggest AI chip, the H100, and its RTX 40 Series GPUs are all built using TSMC’s cutting-edge processes. To lock in capacity, Nvidia usually has to put down huge non-refundable deposits—sometimes months, or even a year, in advance.
Here’s how stuff usually unfolds between them:
- Nvidia finalizes a chip design.
- They send the designs to TSMC, basically as gigantic files full of technical specs.
- TSMC schedules the production and sets up the right manufacturing tools (think: photolithography—seriously high-tech stuff).
- Nvidia pays in tranches, often up front, to make sure they get enough factory time amid global demand.
- The finished chips get shipped to Nvidia’s partners for final assembly onto graphics cards or servers.
All this means semiconductors from Nvidia are only as good as the wafer space they can secure at TSMC. When there was a chip shortage in 2021, even Nvidia struggled to get enough supply. This setup also explains why gamers, AI companies, and even crypto miners sometimes complain about shortages and soaring prices.
Just to see how important this bond is, check this out:
Year | Nvidia Revenue (USD) | TSMC Revenue from Nvidia (USD, approx.) |
---|---|---|
2022 | $26.9 Billion | $7-9 Billion |
2023 | $27.0 Billion | $10+ Billion |
So, if you’re into the business of electronics manufacturing India, knowing how tightly these two giants are locked together is half the battle when you're trying to predict what’s coming next—or where a big opportunity might pop up.
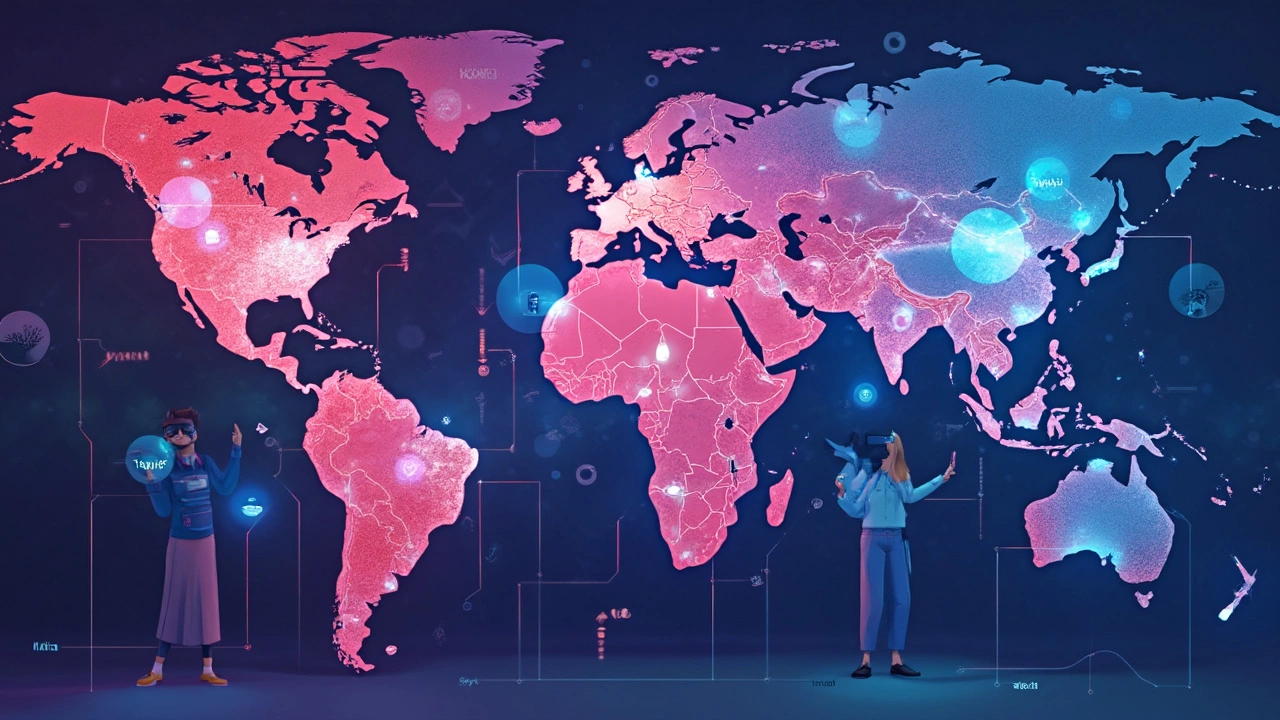
What’s the Impact on Electronics Manufacturing?
When Nvidia designs a new chip and partners with TSMC, the entire electronics manufacturing world feels the ripple. Take gaming consoles, smartphones, and even cars; all these devices depend on powerful chips, and the majority of them come from this Taiwan-based foundry. Because TSMC runs at the leading-edge of technology—think 5nm and 3nm nodes—it shapes which gadgets are even possible.
Here’s the kicker: if TSMC production slows, everyone from PC makers in Bangalore to car factories in Chennai runs into trouble. We’ve seen this happen during the global chip shortage, when long waiting lists left assembly lines idle and prices on graphics cards shot through the roof. There’s real-world fallout when supply chains lean on just a handful of players.
But it’s not all doom and gloom; there’s also a positive side. When a hot new semiconductor like Nvidia’s H100 launches fast thanks to TSMC’s efficiency, fresh tech arrives on shelves everywhere—faster computers, smarter voice assistants, and even medical devices. That raises the bar for manufacturers everywhere, including in India, who now know exactly what level of performance they need to match or connect with.
- Device makers—big and small—must watch Nvidia’s and TSMC’s output to plan their product launches.
- India’s electronics facilities often depend on chips made at TSMC, so delays or changes there impact everything from local smartphone factories to giant car assembly lines.
- Manufacturing plans increasingly revolve around chip supply, not just labor or location—if TSMC is full, your gadget’s launch date might slip.
You don’t have to look far for proof. A 2023 supply chain report showed that over 80% of advanced chips for AI and gaming devices came from just two companies: TSMC and Samsung. That grip means any bottleneck, trade spat, or natural disaster in Taiwan has global consequences, especially for countries like India looking to expand their share in the electronics manufacturing game.
India’s Role: Big Dreams or Just Buzz?
India’s been shouting about becoming the next electronics manufacturing giant for years. But when it comes to actual semiconductor production, there’s still a mountain to climb. Most of the world’s advanced chips, including those from giants like Nvidia, come out of places like Taiwan, South Korea, and the US. So, where does India actually stand right now?
Here’s the real deal: India does make tons of electronics—think phones, TVs, and cheap chipsets for appliances. But high-tech semiconductor fabrication, the kind TSMC handles for Nvidia, just isn’t happening in India… yet. The government rolled out a $10 billion incentive package in 2022, hoping to lure major players. Companies like Micron and ISMC have announced plans, but nothing’s hit mass production. As of April 2025, there’s not one operational advanced foundry in the country.
Look at the numbers:
Country | Advanced Chip Foundries (2025) |
---|---|
Taiwan | 20+ |
South Korea | 5 |
US | 8 |
India | 0 |
Now, there’s plenty of buzz. Startups want to crack design, Indian engineers are global stars, and multinationals have set up research hubs in Bangalore and Hyderabad. But until there’s an actual wafer fab spitting out chips on Indian soil, most of the
Tips for Navigating the Chip Supply Chain
The semiconductor supply chain isn’t just about waiting for chips to show up—there’s a maze of steps involving orders, logistics, and sometimes, flat-out guessing supply and demand. If you’re in electronics manufacturing (especially in India), a late chip shipment can stall your whole assembly line. Here’s how to keep things moving when everyone’s chasing Nvidia or TSMC-level parts.
- Plan way ahead: Don’t just trust sales forecasts. Demand for chips like Nvidia’s H100 blew past expectations in 2023, causing lead times to stretch from weeks to more than 12 months. If you don’t line up suppliers early, you’ll be left scrambling when tech trends shift.
- Diversify your suppliers: If all your chips come from just one fab like TSMC, you’re at risk of production hiccups. Consider splitting orders or qualifying backup suppliers whenever possible, even if it costs a bit more up front.
- Stay plugged in to global news: A drought in Taiwan or export rules in the US can shuffle chip availability overnight. Set up alerts for key regions and companies so you’re not caught off guard by sudden shortages.
- Negotiate transparent terms: Always push for clarity on delivery dates, penalties for delays, and options for expedited orders. Make sure contracts are clear about what happens when there’s a global chip crunch.
- Embrace local manufacturing where you can: With India investing over $10 billion in local semiconductor fabs since 2023, opportunities are growing to source chips closer to home—cutting down surprises tied to global shipping storms or border delays.
Supplier | Typical Lead Time (2024) | Used by |
---|---|---|
TSMC | 6-18 months | Nvidia, AMD, Apple |
Samsung | 4-12 months | Qualcomm, Google |
SMIC (China) | 9-20 months | Huawei, local brands |
Bottom line: Smart supply chain moves don’t just save headaches—they keep your business alive in a market where everyone wants the same chips. Make supplier relationships a priority, stay on top of world events, and watch how rising players in India could soon give more options for electronics manufacturing in the next couple of years.