In the intricate world of food processing, technology plays a pivotal role, ensuring that the products we consume meet high standards of quality and safety. Among the many components in a food processing unit, Read-Only Memory, or ROM, often flies under the radar yet holds tremendous importance.
Almost everyone is familiar with ROM's use in computing, but in food processing, it takes on a unique role. ROM helps in executing specific tasks repeatedly and reliably without alterations, making it a crucial element for maintaining the consistency and reliability of processes in food production.
Why does this matter? Imagine the quality of your morning cereal depending on a tiny memory chip doing its job flawlessly day in and day out. This article sheds light on ROM's role in food processing units, revealing its hidden impact on the industry and why it matters to everyone who appreciates safe, well-made food.
- Introduction to ROM
- Role of ROM in Food Processing
- Benefits of Using ROM
- Challenges and Solutions
- Practical Applications
- Future Trends
Introduction to ROM
When you think about food processing, the first images that might come to mind include sprawling factories, conveyor belts loaded with fruits and vegetables, and complex machinery humming in a synchronized dance. Hidden within this mechanical orchestra is a crucial component: Read-Only Memory, known as ROM. In the realm of technology, ROM is a household name, often associated with computers and digital devices. However, its role extends far beyond these traditional boundaries, finding a vital place in the industrial food landscape, significantly impacting how our favorite foods are produced.
To understand why ROM is such a game changer in food processing units, we must appreciate its fundamental properties. ROM is a type of non-volatile memory, which means it can retain data even when the power is turned off. This makes it an invaluable component in devices that require consistent data storage without the risk of accidental erasure. In food processing machines, ROM is responsible for storing the firmware that dictates how the machinery should function. It holds the vital instructions needed to maintain the routine operations that ensure every cookie is baked to perfection or each can of soup is sealed securely.
Its imperishable nature makes ROM vital for maintaining consistent and reliable operations. Food technology demands precision; after all, an error in processing could lead to serious safety issues or significant financial losses. The unwavering stability provided by ROM helps to safeguard against such risks, allowing manufacturers meticulous control over their processes, which leads to enhanced food safety and efficiency. According to a report by the Food Processing Magazine, companies implementing advanced technology systems, including ROM, have seen a reduction in operational errors by up to 35%.
Besides, the permanence of ROM brings peace of mind to operators who might worry about data integrity in high-stakes environments. As every instruction is permanently etched onto the chip, there's no chance of accidental deletions or data corruption—a critical feature when dealing with processes that must be repeated accurately over millions of cycles. Former technical director at TechFood Innovations, Thomas Garvey, was once quoted saying, "In an industry where precision is paramount, ROM provides the reliability that's often overlooked but never underdelivered." Such endorsement underlines its indispensable role in the sector.
We often overlook the silent hero behind complex systems until a breakdown occurs, but these unsung heroes like ROM quietly ensure that everything functions flawlessly. As food factories move towards more automation and greater reliance on technology, the role that ROM plays becomes even more crucial. Its capacity to seamlessly integrate into the scalable systems is essential for these environments where even the slightest deviation from the preset script can result in extensive downtime and substantial financial implications. By creating redundancy and stability, ROM enables food processing units to consistently meet quality standards without fail.
In the broader spectrum, the integration of ROM into food processing technologies is also an answer to the growing consumer demand for safe, traceable, and quality food products. Through the use of ROM, manufacturers can meet these needs more efficiently, proving that technology isn’t just an enhancer but a necessity for modern food production. With the industry's projected expansion, understanding ROM’s current and future potential becomes more relevant than ever, especially when considering the demands for heightened safety regulations and sustainable practices within the industry.
Role of ROM in Food Processing
In the fast-paced environment of food processing units, consistency and reliability stand paramount. As these units need to churn out thousands of products each hour, the systems controlling these processes must operate consistently without fail. Here is where Read-Only Memory (ROM) steps into the picture. ROM stores essential instructions and data perpetually, ensuring that every machine in the food processing line knows exactly what to do and when to do it. ROM's immutability means once data is written onto it during manufacturing, it cannot be easily altered or erased, acting as a safeguard against inadvertent or malicious changes.
The role of ROM in this industry lies not just in its ability to store data but also in its maintenance-free operation. In food processing units with stringent hygienic standards, the fewer maintenance interventions required, the lesser the risk of contamination. ROM-based systems do not need frequent reloading; thus, they are perfect for environments where uptime is critical. An impressive statistic: some food processing units boast a machine uptime of over 99%, partly credited to dependable ROM technology. Even the best RAM systems see a dip in performance without periodic attention, but ROM keeps every machine's mind unclouded, allowing the efficient operation of everything from mixers to packaging lines.
Imagine the consistency of a beloved food item. Suppose a cereal brand you started eating as a child still tastes the same today. This trusted uniformity results from processes that haven't deviated, guaranteed by the ROM's unchanging instructions guiding machines precisely over the decades. A retired engineer of a major food brand once shared,
"ROM is our silent sentinel. It gives our machines a memory immune to the whims of chance, ensuring our products remain safe and consistent, regardless of other technological upgrades around it."Such testimonials highlight how ROM invisibly safeguards one of the food industry's most valued assets - consistency. Products made to meet today's standards will still comply years from now, thanks to this steadfast technology.
Additionally, the integration of ROM in modern systems contributes to the overall efficiency by allowing seamless coordination between various automated procures. Let’s explore how different machinery benefits: a bottling line machine, for example, may use ROM to recall the specific timings for the perfect seal, ensuring each bottle leaves the factory absolutely leak-proof. Similarly, in temperature-sensitive operations like pasteurization, ROM helps store precise heat settings, ensuring pathogens are eliminated while flavors are retained. Universally, there's a pattern of utilizing ROM to safeguard crucial operations where repetitive precision is critical, reducing both errors and the need for regular system checks.
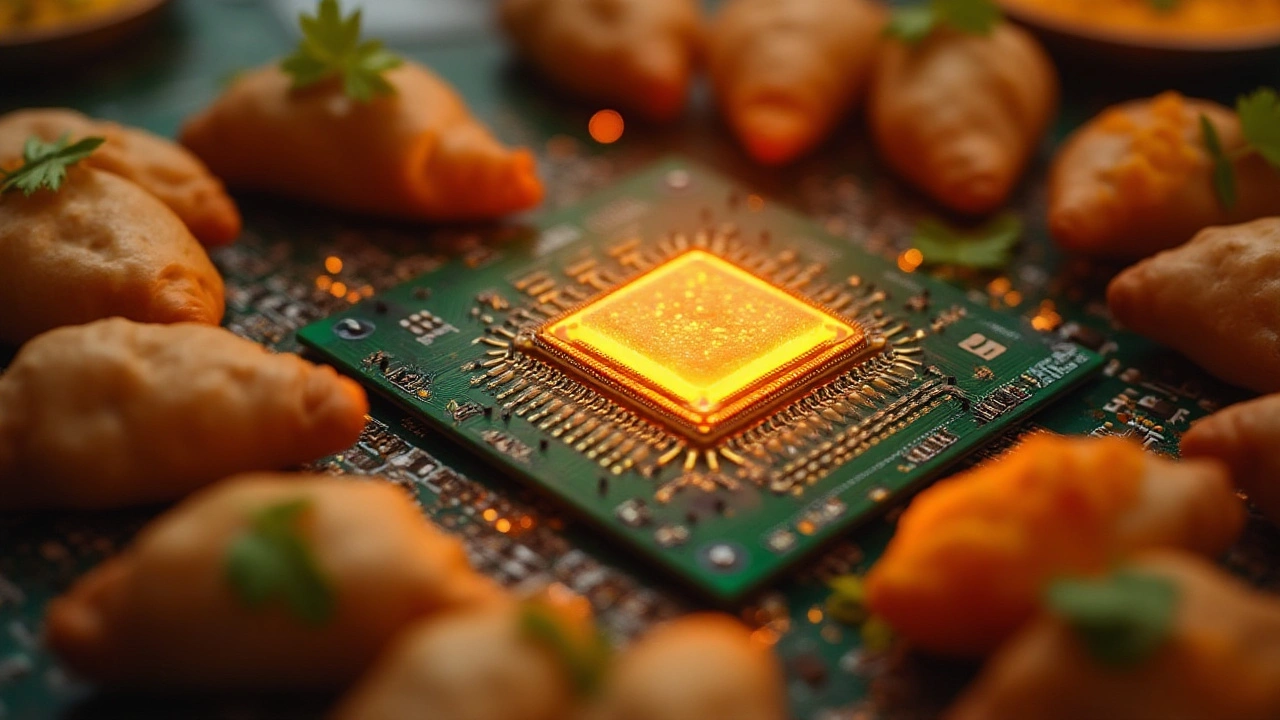
Benefits of Using ROM
When we address the significance of ROM in food processing units, it’s crucial to outline the various benefits that make it an indispensable technology in the industry. First and foremost, the reliability of ROM cannot be understated. Since it's designed to be immutable, this means it can store essential operational data that remains stable and secure over time. For food manufacturers, this translates to maintaining consistent recipes and processes critical for quality assurance. In an industry where variation can lead to safety concerns, such consistency is golden. Imagine a scenario where the proportion of ingredients must be precise—it’s ROM that ensures these values don’t drift over countless cycles of operation.
Another notable advantage is the food safety that ROM contributes to. Through its stable storage of critical operating procedures, it helps in adhering to stringent safety regulations by providing exact control over machine functions, thus reducing the risk of improper mixing or contamination. This protective layer not only secures the final product but also shields companies from liabilities related to deviations in product standards. It’s fascinating how such a small component can have a large impact on protecting consumer health.
In terms of reduced costs, ROM plays a crucial role. Due to its non-volatile nature, there are decreasing necessities for regular updates or modifications, leading to decreased downtime. When machines can reliably operate without frequent interruptions for recalibration or software updates, production efficiency naturally increases. This benefit spirals into lower operational costs and improved profitability for the business. A quaint yet powerful peace of mind comes from knowing the machinery won’t need constant babysitting.
According to a study by the Food Processing Technology Institute, "Implementing robust ROM systems into production lines has led to a 25% increase in production efficiency in surveyed plants."Furthermore, training employees becomes less of a hassle when ROM is utilized. Employees need less time learning how to manage conditions that deviate from standard operations because the baseline remains untouched with ROM systems. This advantage not only saves training costs but increases worker productivity as they can focus on optimizing other aspects of production.
Security is also enhanced with the presence of ROM. As it is challenging to modify, the sensitive operational data it logs is shielded from unauthorized alterations. This feature is crucial in protecting proprietary recipes and production methodologies, offering competitive leverage in the vast food industry. Manufacturers no longer have to fear the sudden misfortunes of data tampering that could tarnish their brand reputation overnight.
ROM has truly revolutionized many aspects of food processing, showing that sometimes, the smallest components can yield the most significant impacts. By ensuring consistency, boosting safety, trimming costs, and tightening security, ROM stands as a cornerstone technology in modern food processing, subtly yet powerfully influencing both daily operations and long-term industry outcomes.
Challenges and Solutions
When implementing ROM technology in modern food processing units, a number of challenges arise from both technical and operational perspectives. One significant issue revolves around integrating this static memory into equipment that must remain adaptable to various production needs. For food manufacturers, flexibility is key, and the inability to modify data in ROM can be limiting when needing swift process adjustments. Yet, this rigidity also offers a level of reliability needed in ensuring consistent output quality over time, an assurance much appreciated by manufacturers and consumers alike.
An additional hurdle involves the long-term stability of food processing systems. Since ROM serves as a non-volatile storage solution, it guarantees data retention without the aid of power. This means that the operating instructions stored are safe from unpredictable power outages or fluctuations. Nonetheless, manufacturers must carefully plan initial programming as updates entail replacing semiconductor chips. Mitigating these problems requires precise initial setup and thorough testing of every programmed routine.
Moreover, balancing the initial cost of implementing ROM is an important factor. Despite its durability, investing in ROM technology can be costly, especially for small-scale processors aiming to improve their technological setups. As food safety regulations evolve and consumer expectations grow, the pressure to adopt state-of-the-art technology intensifies. One possible solution lies in leveraging grants and subsidies from governmental and organizational bodies that support innovation in the food sector. Some regions have shown remarkable success using such financial aid programs to modernize food systems, reflecting an encouraging trend toward widespread adoption of cutting-edge solutions.
Security and Data Integrity
As with many modern technologies, food processing units equipped with ROM face cybersecurity threats. Protecting critical operational instructions from tampering poses a challenge as cyber threats continue to grow more sophisticated. Ensuring ROM's defenses require a layered systems approach, incorporating advanced encryption and monitoring measures to shield against malicious interference. Regular security audits and maintaining up-to-date measures are crucial to safeguard the process integrity and ensure compliance with global food safety standards. According to Dr. Alex Moore, a leading expert in food technology, "Ensuring the security of system operations through regular updates and monitoring is not just about preventing loss, but enhancing trust in our food systems."
Solutions often involve creating redundancies within the system or employing hybrid memory solutions combining ROM with other more flexible storage options. This allows for retaining the advantages of ROM's stability while gaining the flexibility needed to update processes without replacing hardware. Collaborations with cybersecurity experts can provide additional insight and guidance to companies seeking to build robust defenses against digital threats that could impact both safety and productivity on the food line. By blending technology with strategy, the benefits of ROM in food processing can be maximized, even amidst a fast-evolving digital landscape.
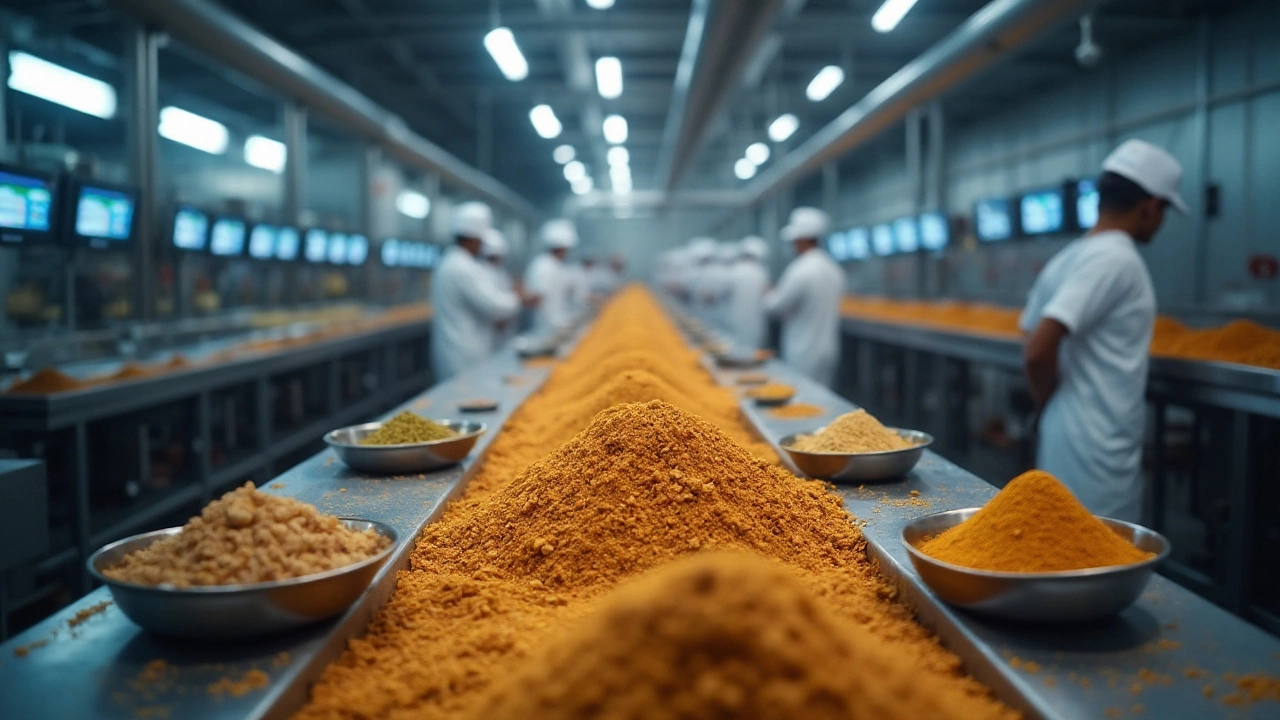
Practical Applications
In the ever-evolving landscape of food processing, the integration of ROM within equipment and devices has surfaced as a game-changer. The primary role of this memory type is to hold critical programming instructions that need to be executed with unwavering reliability. These instructions often relate to machine calibration, quality control processes, and emergency protocols that ensure seamless operations. It is no exaggeration to say that without the underlying strength of ROM, the stability and precision required in food manufacturing could be jeopardized. In many food processing units, you will find ROM embedded within control systems, sustaining programmed sequences that guide machines through every step of the production line, ensuring that tasks are carried out precisely as intended without variability.
Take, for instance, the process of pasteurization, where maintaining exact temperature and timing is paramount to ensure product safety. The ROM in such systems stores immutable data that governs these parameters, allowing for consistent and reliable operation cycles, and eliminating the possibility of accidental tampering. It's fascinating to note that even a small glitch in communication could result in product recalls or health warnings, highlighting the critical role of ROM in safeguarding public health. In some advanced systems, ROM works hand-in-hand with real-time sensors and feedback loops, allowing for adjustments to be made based on externally-generated data while maintaining core programming integrity.
With food safety regulations becoming increasingly stringent, the reliance on solid technological frameworks continues to grow. Many experts underscore the importance of technology in this arena. A senior engineer at a prominent food-processing company once remarked,
"The backbone of our operational success lies in our ability to depend on unmodifiable programming. It's the invisible lifeline of our production cycle, ensuring that nothing goes wrong."Such insights illustrate the intangible yet undeniable presence of ROM and its contributions to maintaining the impeccable standards of food production. Additionally, with increasing automation, efficient memory solutions are shaping the industry more than ever. From small-scale establishments to multinational corporations, the adherence to programmed precision is a universal need.
As the food industry marches into future phases, one can expect an enhanced reliance on smart technology configurations. Companies are eager to integrate machine learning and AI in tandem with traditional ROM systems. This collaboration aims to harness the best of both worlds: the unwavering reliability of ROM and the adaptability and data-driven insights provided by AI. By doing so, manufacturers can innovate continuously, offering products that are both safe for consumption and delightfully consistent. Embracing such technology doesn't just enhance efficiency but also opens pathways to achieving revolutionary breakthroughs in food processing. The tangible benefits of such integrations are immense, with many already witnessing marked improvements in production smoothness and consistency.
Future Trends
The landscape of food processing is ever-evolving, with technology setting the stage for continuous advancements. In the realm of food processing, future trends are increasingly pointing towards smarter and more efficient systems, and the role of ROM is central to these developments. As we head into an era where automation and precision become even more crucial, ROM's unyielding ability to store critical instructions unchangeably remains of paramount importance. It ensures that machines continue to perform their tasks reliably, particularly under challenging conditions where manual intervention could lead to inconsistencies. This capacity to provide steadfast control over essential processes in food processing has positioned ROM as a cornerstone of future-proof technology.
An emerging trend is the integration of AI and machine learning in food processing units, enabling machines to learn and adapt. While this shift towards intelligent systems is undeniable, the inclusion of modifications or new 'learning' data doesn't come at the compromise of core stability, which is where ROM's function as a stable memory base remains critical. There's also a rising demand for transparency in the food supply chain, and ensuring processes are tamper-proof is non-negotiable. The reliability of ROM in sustaining process constancy provides a safeguard even as other more dynamic technologies operate around it.
According to a report by Food Technology Magazine, "With the increasing complexity of production requirements and the push for high-speed processing, the uncompromised reliability of ROM in controlling these systems is more critical than ever." As food safety regulations continue to tighten globally, technologies that offer robust reliability, like ROM, will see increased application. Plants are moving towards integrating Internet of Things (IoT) solutions, with ROM playing a vital role in data integrity. These systems can gather and analyze vast amounts of data in real-time, but the core foundation of operational code must remain steadfast.
Looking ahead, companies are exploring the development of ROM chips with enhanced environmental resilience, catering to the harsh environments often found in food processing facilities. Additionally, the advent of more sustainable and efficient manufacturing technology is driving interest in energy-efficient components, including ROM, which continues to operate with low power consumption. This trend aligns with global sustainability goals as businesses seek to minimize their carbon footprint while maximizing production output. Among the groundbreaking proposals is the concept of adaptive ROM that maintains its core strength of stability but allows for minor adjustments under strictly controlled conditions, potentially merging eras of technological development.
The application of ROM in thermal processing systems, often used to sterilize and preserve foods, is expanding. Here, its ability to store intricate calibration data ensures optimal performance even under fluctuating operational demands. As more integrative technologies permeate the food processing domain, manufacturers are advocating for hybrid systems where ROM interoperates with volatile memories offering flexibility. Such systems appear likely as companies strive to balance adaptability with the unassailability of their processing baselines. As we progress, we will likely witness a significant transformation involving ROM in food tech, proving that even a technology often considered static has a vibrant future ahead.