When my son Ishaan asked me why some factories in our town had closed their doors, I realized this isn’t just a news headline—it’s a real thing hitting families across the country. But is manufacturing actually down in the US, or is there more to the story?
First, here’s the blunt truth: America still makes a ton of stuff. We’re not talking about the super-old-school assembly lines you see in vintage documentaries, but the high-tech operations building cars, electronics, and complex machinery. But no sugarcoating—the number of people working in factories is lower compared to the golden era of the 1970s and 80s. Part of it is jobs going overseas, sure, but robotics and automation play a huge part too. One stat that always gets people: Between 2000 and now, manufacturing output in the US actually grew by about 30%, even though we’ve lost millions of factory jobs. That means machines are doing more of the heavy lifting now.
If you’re reading this and you work on the floor, or run a small shop, those big numbers might not mean much when a local plant shuts down. It’s a complicated picture—one where government schemes, global supply chains, and tech changes mix together.
- The Numbers: Factory Jobs and Output
- How Government Schemes Shape the Industry
- Why Some Regions Feel the Pain More
- Tips and Realities for Workers and Business Owners
The Numbers: Factory Jobs and Output
Here’s where things get real with US manufacturing: we pump out more products than you’d think, but we do it today with way fewer hands on deck. Back in 1979, the US had nearly 19.5 million workers in manufacturing. Fast-forward to today, and that number is closer to 13 million. That’s a drop you can’t ignore. But the wild part? Output—the actual stuff being made—hasn’t crashed in the same way. It’s actually climbed, especially in high-tech sectors.
Check out this simple breakdown:
Year | Factory Jobs (millions) | Manufacturing Output Index* |
---|---|---|
1979 | 19.5 | 70 |
2000 | 17.3 | 98 |
2024 | 13.0 | 125 |
*Base year index: 2012 = 100 (Federal Reserve data)
This chart says it straight: we lost over 6 million factory jobs since 1979, yet we still upped our game on total output. The change is mostly thanks to automation—robots, computer-guided tools, and more efficient machines. So, more stuff, fewer people.
Another thing—industry trends show that what we make has shifted. The old picture of rows of workers making shoes or simple electronics is outdated. US factories now pop out airplanes, medical tech, and chips for your car. Traditional jobs disappeared fast, but new roles in programming, machine repair, and advanced materials popped up in their place.
And wages? They haven’t kept up with inflation. Even if output is up, factory workers aren’t always seeing bigger paychecks. This gap is why the vibe in some hometowns is way bleaker than the national stats let on.
If you’re tracking factory jobs these days, know this: there’s growth in areas like clean energy and food production, but you can’t expect the old school manufacturing boom to come roaring back without some serious changes.
How Government Schemes Shape the Industry
Every time someone drops the words "government manufacturing schemes," some people’s eyes glaze over. But these programs have a massive impact on what actually happens in American factories. The big headline this past year? The CHIPS and Science Act. That’s a $280 billion government push, rolled out in 2022, meant to bring semiconductor manufacturing back to the US. Instead of ordering chips from overseas, the plan is to make more of them right here. Intel and Micron announced new plants in Ohio and New York because of it. Those aren’t just press releases—construction is real, jobs are lined up, and local economies are hoping for a boost.
Then there’s the Inflation Reduction Act. Passed in August 2022, it’s pumping billions into clean energy projects, electric vehicles, and battery factories. You hear about new battery plants in places like Georgia and Tennessee? These didn’t just pop up by chance. They follow tax credits and federal money. If your business is in the US manufacturing supply chain, these new rules can decide whether you hire, fire, or expand.
Here’s a quick breakdown of where big government money went lately for factory jobs and new projects:
Program | Main Focus | Estimated Spending |
---|---|---|
CHIPS & Science Act | Semiconductors | $52 billion |
Inflation Reduction Act | Green Energy, EVs | $370 billion |
Buy American | Government Purchases of US Goods | $100+ billion, ongoing |
One thing these government programs can’t fix overnight: skills gaps. Some money is now going into worker training, but a lot of folks who lost old-school manufacturing jobs need new training to land work in today’s high-tech plants. For small and medium-sized businesses, it’s worth following updates from the Department of Commerce or your local economic development office. Grants, tax breaks, and hiring incentives come and go, and sometimes they make the difference between closing up shop or doubling down on new hires.
If you care about industry trends or run a shop that’s just barely hanging on, it’s worth keeping tabs on these government schemes. Even small policy tweaks—like expanding the definition of "American-made" or changing tariffs—can shake up your cost sheet fast.
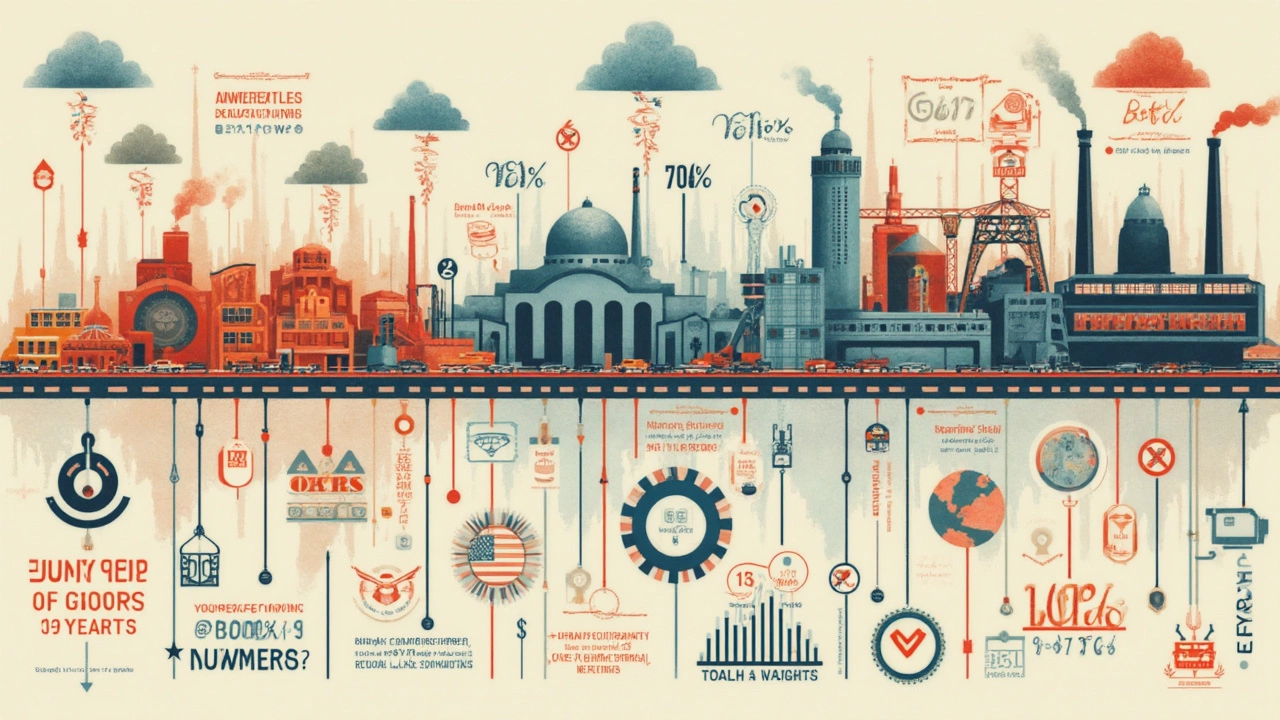
Why Some Regions Feel the Pain More
Everyone hears about shuttered plants, but the pain isn’t spread out evenly across the country. The real kicker is, some areas get hit way harder when those jobs disappear. Places like the Midwest—think Ohio, Michigan, and Indiana—built their whole towns around big factories. So when companies move production overseas or invest in robots, it can feel like the heart got ripped right out of the city.
The US manufacturing story is really a local one. While cities like Dallas and Nashville have managed to pivot into tech and healthcare, spots like Flint and Gary struggle to fill the gaps left by lost factory jobs. Here’s a simple breakdown that shows how uneven it is:
State | Factories Lost (2010-2024) | Manufacturing Jobs Lost |
---|---|---|
Ohio | 2,300+ | ~65,000 |
Michigan | 1,900+ | ~52,000 |
Texas | 500- | Gained 25,000+ |
Some reasons for these differences:
- Local economies in the Midwest often rely heavily on one big employer. When that employer downsizes, there’s not much else to fall back on.
- The South, especially places like Texas, snags new factories because of lower taxes, cheaper land, and big pushes from state governments.
- Regions focused on older industries—like steel or auto parts—sometimes don’t have enough tech training programs to help workers switch fields.
What makes it sting even more? Real estate prices in these towns often drop, schools shrink, and local diners end up with fewer customers. The fallout isn’t just personal; it shakes up the whole community. The lesson: industry trends and government moves matter, but where you live makes all the difference in how the manufacturing cycle hits home.
Tips and Realities for Workers and Business Owners
If you’re staring at shrinking shifts or wrestling with costs to keep your shop running, you’re not alone. Things have changed in US manufacturing—but understanding where you fit right now is more useful than waiting around for the old days to come back.
For starters, don’t ignore upskilling. The best manufacturing jobs now often go to folks trained in things like robotics, CNC machines, and digital quality checks. According to the National Association of Manufacturers, about 2.1 million manufacturing jobs in the US could go unfilled by 2030 simply because of the skills gap.
- If you’re a worker, check out community college programs or free online courses in basic automation, CAD, or logistics. Even learning to read digital blueprints makes you way more hireable.
- If you run a small factory or shop, tap into government support—there are real grants for automation upgrades and tax breaks for buying American-made equipment. The Manufacturing Extension Partnership (MEP) is a good resource for personalized help.
Tech isn’t everything. Some supply chain headaches from the last couple of years (remember the chip shortage?) make it smart to source parts locally when you can, even if it seems pricier up front. Small-batch and custom products are having a moment as well—especially in industries like automotive and specialty consumer goods.
Here’s a quick comparison of job trends to keep everyone grounded:
Year | Manufacturing Jobs (Millions) | Manufacturing Output (Index) |
---|---|---|
2000 | 17.3 | 96 |
2010 | 11.5 | 102 |
2023 | 12.9 | 124 |
What’s that mean in real terms? Factories are producing more with fewer people, so the smart money’s on adaptability. Try not to get stuck doing things one way if the market’s changing under your feet.
Government manufacturing schemes like the CHIPS Act and the Inflation Reduction Act are pouring billions into certain sectors (like semiconductors, green energy, and EVs). If you’re in those spaces, there are contracts and incentives popping up all the time—keep an eye on federal and state grant announcements, and don’t be afraid to ask for help navigating the process.
The hard truth: the days of just clocking in and pushing the same button are pretty much over. But with some effort—whether you’re learning a new skill or finding a grant—there’s real opportunity in factory jobs and running a shop that adapts fast. The folks who stay curious and flexible are the ones doing just fine.