Ask anyone, and they’ll probably say plastic is cheap to make. It’s true—walk into any store and you’ll see plastic in almost every product, often at bargain prices. But here’s the twist: the process of making plastic isn’t always as inexpensive as it seems. There are a bunch of hidden costs that catch a lot of businesses off guard.
It all starts with raw materials. Most plastics come from oil or natural gas, and those prices are anything but stable. Political drama on the other side of the world? Oil prices jump—so does the cost of making plastic. And it doesn’t stop there. The machines that melt, mold, and shape plastic eat up huge amounts of electricity. If a factory’s power bill goes up, so does the price tag on every plastic bottle, toy, or gadget they pump out.
If you’re thinking about working with a plastic manufacturing company, understanding the real costs behind plastic is crucial. Knowing where the money goes can help you negotiate better deals, ask smarter questions, and avoid nasty surprises. Plus, if you’re aiming for budget-friendly options, there are definitely strategies and tips that can make the process less painful on your wallet. Let’s break down what really drives the cost of plastic manufacturing.
- What Goes Into Making Plastic?
- Raw Material Costs: Not as Cheap as You Think
- Energy and Equipment: The Hidden Expenses
- Mass Production vs. Custom Orders
- Recycling: Is It Cheaper or Not?
- Tips for Cutting Costs with Plastic Manufacturing Companies
What Goes Into Making Plastic?
Most people don’t realize how much actually happens before that plastic cup or phone case lands in your hand. The whole process starts with a core ingredient: oil or natural gas. These fossil fuels are the raw materials—chemists call them “feedstocks”—used to make different types of plastics. Roughly 99% of all plastics come from these sources.
The journey from oil to finished product includes a bunch of steps:
- Extraction: Companies first pull crude oil or natural gas out of the ground. This requires a lot of heavy machinery and energy.
- Refining: The oil or gas is then heated and separated into various chemicals at refineries. Naphtha, one specific fraction, is super important because it’s the base for many plastics you see every day.
- Polymerization: Here’s where the magic happens. Factories use chemical reactions to string tiny molecules (monomers) together, making long chains called polymers. These are the backbone of plastic.
- Compounding: Next, manufacturers mix in coloring, softeners, or other additives to get different textures, strengths, or colors.
- Forming and Shaping: That modified plastic gets melted and shaped into everything from water bottles to car bumpers using machines like injection molders or extruders.
This whole process isn’t just about chemistry—it’s powered by a ton of electricity and heat. In fact, energy can make up to 20% of the total cost of plastic production, depending on where you are and how efficient the factory is.
Step | Cost Share of Total |
---|---|
Raw Materials (Oil/Gas) | Up to 50% |
Energy | 10–20% |
Additives & Colorants | 5–10% |
Labor | 10–20% |
Maintenance & Equipment | 5–10% |
So, while it looks like plastic just pops out of a machine, in reality it takes a whole chain of steps, a lot of equipment, and significant costs along the way. That’s why when oil prices change, or electricity gets expensive, you’ll see prices jump even for that simple plastic toy or container.
Raw Material Costs: Not as Cheap as You Think
If you think plastic is just cheap junk, think again. Raw materials are the real game-changer in plastic manufacturing, and the costs can swing wildly overnight. Most plastics—like polyethylene, polypropylene, and PVC—are made from crude oil or natural gas. When oil prices spike, the price of making plastic follows almost immediately.
Let’s cut to the chase with some real numbers. The price for polypropylene pellets, just the raw stuff, jumped from around $1,000 a ton in 2020 to nearly $1,800 a ton by early 2021. And this wasn’t a one-off thing. Natural disasters, refinery shutdowns, or geopolitical messes all mess with prices regularly.
Plastic Type | Main Raw Material | 2023 Avg. Price (per ton) | 2020 Avg. Price (per ton) |
---|---|---|---|
Polyethylene (PE) | Ethylene (from oil/gas) | $1,400 | $900 |
Polypropylene (PP) | Propylene (from oil/gas) | $1,600 | $1,000 |
PVC | Vinyl chloride (from salt/oil) | $1,200 | $800 |
But that’s not all. There’s also a whole chain of logistics, shipping, and processing fees before those plastic pellets even hit the factory floor. Not to mention, environmental fees and taxes have become a thing lately, especially in Europe and North America. These parts sneak into the final bill, making things less "cheap" than people expect.
Here’s a quick tip: If you’re comparing quotes from different plastic manufacturers, always ask about their material sources and how they deal with price swings. Some companies lock in prices with long-term contracts when oil is cheap—which means they’re less likely to pass on sudden increases to you. Others buy at market rates, so your costs go up and down with global events. Knowing who does what can save you a headache later.
Energy and Equipment: The Hidden Expenses
People usually picture plastic as lightweight and cheap, but the process behind it is actually an energy monster. Making plastic needs tons of power. For example, in injection molding—the process behind most bottle caps and toys—the machines need to heat raw materials up to 270°C (more than twice as hot as your oven at home) before squeezing them into molds.
Here’s the thing: industrial plastic machines run all day, racking up electricity bills that would make your eyes water. Energy can take up anywhere from 10% to 30% of the total cost to produce plastic parts, depending on the factory and the country. Some reports say that just one old, inefficient injection molding machine can cost a factory an extra $9,000 per year in extra energy compared to a newer, efficient model.
It’s not just about electricity. The equipment itself is pricey. Extruders, blow molders, and injection molding machines can range from $50,000 for a small one to over $500,000 for a giant, high-speed setup. Plus, these machines don’t last forever—they need regular maintenance, replacement parts, and sometimes full overhauls after a few years.
Equipment | Average New Price (USD) | Maintenance Per Year |
---|---|---|
Injection Molding Machine | $150,000 | $10,000–$20,000 |
Blow Molding Machine | $100,000 | $8,000–$15,000 |
Extruder | $75,000 | $7,000–$12,000 |
On top of all that, any downtime—when a machine breaks or needs cleaning—means lost production, which can make the final product even more expensive. If you’re checking prices from a plastic manufacturing company, make sure to ask how old their equipment is and if they use energy-efficient machines. Sometimes, factories with newer tech can actually offer lower prices because their machines eat up less energy.
Bottom line: behind every cheap plastic part, there’s a mountain of hidden energy and equipment costs that manufacturers deal with every day. The less efficient the setup, the more money leaks out—and the higher the price you end up paying.
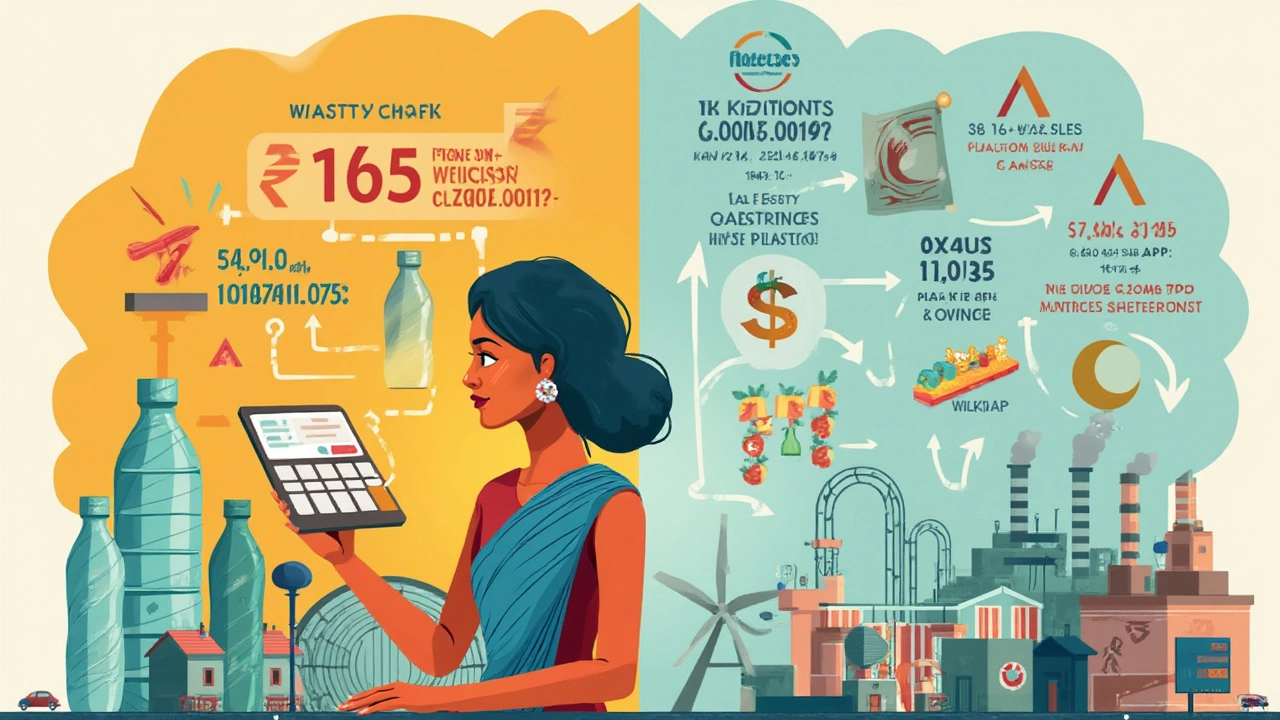
Mass Production vs. Custom Orders
This is where the real difference in plastic production costs shows up. If you need a million identical water bottles, the math is very different than ordering a few hundred custom phone cases. Mass production lets plastic manufacturing companies spread all those upfront expenses—like making molds and setting up machines—across a huge number of parts. That’s why big brands selling standard plastic items can do it so cheaply.
Custom orders tell a different story. Creating a custom design usually means building a new mold, which often costs anywhere from $5,000 to $50,000, depending on complexity and size. If you’re only making a small batch, that mold cost gets divided by way fewer items, so the price per piece goes up—sometimes a lot.
Check out how the price can change based on order size:
Order Size | Mold Cost | Cost Per Part (Mold Only) |
---|---|---|
10,000 pieces | $10,000 | $1.00 |
100,000 pieces | $10,000 | $0.10 |
1,000,000 pieces | $10,000 | $0.01 |
See how each part gets cheaper the more you make? And that’s just for the mold—raw materials, energy, and machine operation also get cheaper per piece when you’re cranking out large runs. Custom jobs often require extra setup, testing, and sometimes fancier materials, which can add even more cost—and slow down delivery.
So if you want to keep costs low with a plastic manufacturing partner, sticking to standard, high-volume products is the way to go. But if you need something unique, it’s smarter to order as many as you can at once, because the per-unit cost drops fast as quantity goes up.
Recycling: Is It Cheaper or Not?
Everyone loves the idea of recycling. It sounds good, it feels responsible, and you might think it saves companies money by reusing old plastic instead of making new stuff. But here’s the real story: recycling plastic isn’t always cheap. Sometimes, it’s more expensive than just starting from scratch with new materials.
Why does this happen? First, plastic has to be sorted, cleaned, and processed before it’s melted down and turned into new products. Sorting is tricky—different types of plastic can’t always be recycled together, so lots of labor and high-tech machines are needed. Plus, cleaning all those containers, bottles, and wrappers before they go into a shredder takes a bunch of water, detergent, and energy. Once it’s finally clean, recycled plastic (also called "recycled resin") sometimes needs extra processing—because it can get contaminated or lose quality during recycling.
Here’s a look at typical cost differences for making new plastic versus recycling:
Process | Average Cost (USD per ton) |
---|---|
Virgin (new) plastic | $1,000 - $1,300 |
Recycled plastic | $900 - $1,600 |
The price swings a lot, depending on oil costs (which affect new plastic) and on the quality or cleanliness of recycled plastic. Sometimes, recycled plastic is actually more expensive, especially if prices for oil drop. In 2024, several reports showed recycled plastic pellets costing up to $1,600 per ton in parts of Asia, while fresh plastic was cheaper in some markets. Quality matters too—certain products, like food packaging, can’t use recycled plastic unless it’s super clean. That means even more processing and higher expenses.
So, is recycling worth it for manufacturers? Sometimes yes—especially if local laws require using recycled material, or if customers demand it for eco reasons. But from a pure cost perspective, recycling doesn’t always beat making new plastic. Smart companies compare prices and source recycled plastic when it lines up with both their plastic manufacturing costs and their values. If you’re sourcing plastic for your product, run the numbers for both options. And always check if your supplier recommends recycled or virgin resin for your needs.
- If cost is your top concern, get quotes for both recycled and new plastic before deciding.
- If you need extra clean material (like for food), expect recycled plastic to be pricier and check regulatory rules.
- Ask your supplier how they handle sorting and cleaning—this impacts quality and cost.
Recycling plastic has a lot going for it, but the cost savings aren’t always guaranteed. It pays to do a bit of homework before jumping in.
Tips for Cutting Costs with Plastic Manufacturing Companies
Worried your plastic project is going to blow your budget? There are actually some solid ways to keep costs down without cutting corners on quality. A few smart moves can make a big difference when dealing with any plastic manufacturing company.
- Choose the right material: Not all plastics are equally priced. Common resins like polyethylene and polypropylene usually cost less than specialty grades or engineering plastics. If your product doesn't need wild chemical resistance or high heat, stick with the basics to save cash.
- Order in bigger batches: Small runs almost always cost more per piece. The setup for each job—like making a custom mold—costs the same no matter if you make 100 or 10,000 items. Bigger orders spread out these fees, making each item cheaper.
- Design for manufacturing: Complicated shapes, sharp corners, or thin walls can push up costs fast. A simpler design makes the molding process easier and reduces the chance of defects. If you’re not a design pro, work with the manufacturer’s engineers to tweak your design for efficiency.
- Reuse tools and molds: Need a similar product in the future? Using the same mold can save thousands. Some companies even rent out common mold shapes, which is great for limited runs or prototypes.
- Consider recycled plastic: When it fits your needs, post-consumer or post-industrial recycled resins slash material costs and can make your brand look greener. Some manufacturers specialize in recycled options that meet most standard specs.
- Negotiate on logistics: Shipping can be a sneaky expense. Ask about local suppliers or factories close to your main market. Shorter transport means lower costs and faster delivery.
If you’re unsure where to start, don’t be shy—ask the manufacturer for money-saving recommendations. They’ve seen every kind of project and often have ideas that never show up in the quote. The key? Be upfront about your priorities and open to small changes that could yield big savings.