The manufacturing industry plays a pivotal role in shaping the global economy. With a plethora of companies vying for the top spot, it's crucial to understand what differentiates the leaders from the rest. This article explores how some of the foremost manufacturing companies have secured their positions as industry giants through innovation, sustainability, and technological advancements.
From engineering feats to ethical manufacturing practices, these companies have set themselves apart by not only meeting the demands of today but also by anticipating the needs of tomorrow. As we delve deeper, we'll examine the traits that define their success and how these principles can be applied across the board. It's an exciting journey into the world of manufacturing, where change is the only constant.
- Introduction to Manufacturing Giants
- Innovative Practices in Manufacturing
- Sustainability and Ethical Manufacturing
- Technological Advancements Driving Growth
- Evaluating Top Performers in the Industry
Introduction to Manufacturing Giants
Manufacturing giants stand as vital pillars in the expansive world of production and industry. These large-scale companies often dominate the landscape, utilizing their extensive networks and resources to influence economic trends globally. A few key players have distinguished themselves uniquely by not only their sheer size and output but also by implementing innovative technologies and practices that set benchmarks for others to follow. For instance, companies like Siemens and Toyota have long been recognized as leaders in the field, thanks to their commitment to quality and constant refine of production processes.
In understanding these top manufacturers, it's important to note the historical context and evolution that have played significant roles in their growth. Many of these enterprises have roots dating back several decades or even centuries, having navigated through significant technological advancements and economic shifts. Their ability to adapt and thrive amid change speaks volumes about their strategic foresight and resilience. An example is General Electric, founded in the late 1800s, which has transformed from a simple electrical company to one of the most diversified and powerful corporations in the world.
"Innovation distinguishes between a leader and a follower." — Steve Jobs
What truly sets these organizations apart is their relentless pursuit of efficiency and quality. They invest heavily in research and development, pushing the boundaries of what current technology can achieve. These companies are not just participants in the industry; they are pioneers blazing trails for others to follow. Consider Samsung, which started as a trading company and has grown into a manufacturing juggernaut, influencing not only the electronics industry but also the broader manufacturing sector. Their commitment to cutting-edge technology and streamlined production strategies has enabled them to stay ahead in a competitive marketplace.
Industry leaders also adhere to rigorous standards in sustainability, a growing concern in today's world. Companies like Unilever have placed significant emphasis on ethical manufacturing practices, ensuring their operations do not harm the environment. This focus on sustainable and ethical production is not just a marketing strategy; it is ingrained in their corporate identity and can yield long-term benefits both socially and economically. As businesses grapple with climate change and resource scarcity, those that lead the charge in adopting sustainable methods are likely to set the foundation for future industry standards.
Innovative Practices in Manufacturing
The journey of manufacturing companies in adapting innovative practices is like watching a river carve its way through rocky terrain, leaving a mark of unwavering persistence and creativity. The change has mostly been driven by the need to stay competitive in an ever-evolving market. The best manufacturing companies today are those that adopt a forward-thinking approach. A wonderful example of innovation in manufacturing is the implementation of additive manufacturing, commonly known as 3D printing. This technology has enabled manufacturers to create complex and precise components with minimal waste, significantly reducing the production cost and time. It's a groundbreaking shift that turns complex ideas into tangible structures at the press of a button.
Lean manufacturing is another practice that has caught the attention of many in the industry. Originating from the automotive sector, it prioritizes efficiency by eliminating waste without compromising on quality. Toyota, for instance, has pioneered this method, showing how cutting down on surplus can effectively streamline operations and boost productivity.
"The Toyota Production System is a 'lean' manufacturing process pioneered by Toyota to make their production more flexible and efficient," says a leading industrial analyst.Combining these practices with various digital transformations, such as the Industrial Internet of Things (IIoT), allows manufacturers to oversee operations in real-time. It’s like having a command center where the pulse of operations is constantly monitored.
Robotics and Automation
In recent years, robotics and automation have taken the manufacturing sector by storm, ushering in a new era of precision and speed. Industrial robots can tirelessly perform tasks round-the-clock, tasks which would otherwise require multiple human shifts. Consider semiconductor manufacturing, where minute measurements and zero tolerance for error are critical. Robots fit the bill perfectly, executing repetitive tasks with consistency. Statistics support this trend as the adoption of robots in factories worldwide is on the rise. A study highlighted in 2023 predicted that by 2030, robot usage will quadruple, revolutionizing manufacturing processes.
Sustainability through Innovation
Environmental concerns have also become a focal point, urging companies to adopt more sustainable manufacturing practices. Many top manufacturers have introduced renewable energy resources into their operations. For instance, companies like Unilever are moving towards 100% renewable energy in their production facilities. They are setting a precedent that sustainability can indeed be profitable and environmentally friendly. With consumers becoming more environmentally conscious, companies understand that this transformation is not just a moral obligation but a strategic business move. Using biodegradable and recyclable materials has become part of product innovation, aligning industry goals with the growing demand for environmentally conscious goods.
- Waste reduction through innovative processes.
- Integration of renewable energy sources into day-to-day operations.
- Use of sustainable materials in production.
- Implementation of energy-efficient machines and processes.
- Recycling processes integrated into manufacturing.
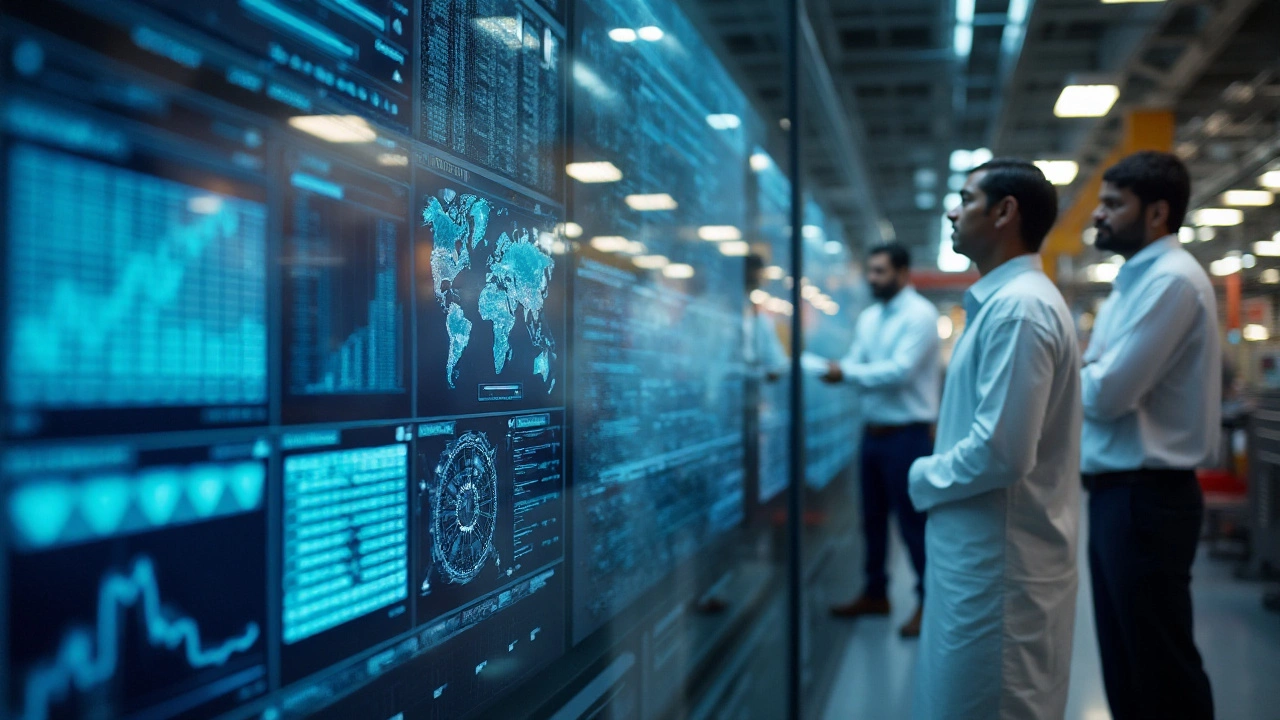
Sustainability and Ethical Manufacturing
In the rapidly evolving world of manufacturing, sustainability isn't just a buzzword—it's a necessity that many leading manufacturing companies are embracing diligently. These companies understand that the environment's well-being is crucial for their long-term survival and success. As industrial giants mold their strategies, they're increasingly prioritizing eco-conscious practices, striving to reduce their environmental footprints. This commitment includes utilizing renewable energy sources, minimizing waste, and optimizing supply chains to be greener and more efficient. The shift comes as governments worldwide implement stricter environmental regulations, pushing businesses to adapt quickly. Adopting sustainable practices not only protects the planet but also serves as a competitive advantage, attracting environmentally-conscious consumers.
At the heart of ethical manufacturing is a dedication to transparency and fairness. Many top manufacturers recognize that their responsibilities extend beyond the factory floor. Ethical practices encompass fair labor conditions, ensuring workers' rights are respected, and their environments are safe. Companies are paying closer attention to the origins of their raw materials, putting pressure on suppliers to adhere to ethical guidelines. As awareness grows, consumers are demanding accountability, pushing producers to adopt practices that prioritize both people and the planet. A well-known example is Patagonia, a company lauded for its initiatives in ethical supply chains and sustainable products. Consumers’ growing inclination towards supporting brands that champion these values reflects a larger trend in the industry.
Said best by Yvon Chouinard, founder of Patagonia, "The economy is a subset of the environment, not the other way around."
Innovation is also playing a crucial role in making manufacturing more sustainable. Companies are investing in cutting-edge technologies such as AI and IoT to improve operational efficiency while reducing resource consumption. Such advancements help streamline production processes, lower energy use, and allow for real-time monitoring of emissions. These technological tools are indispensable in achieving sustainability goals, providing valuable data that drives change. For example, BMW has integrated AI to enhance efficiency in its production lines, which contributes to significant energy savings. This embrace of technology signifies a promising shift towards more resilient and sustainable manufacturing landscapes.
The adoption of sustainability practices varies across the manufacturing sector, with certain regions and industries leading the charge. European manufacturing firms often rank high in global sustainability indexes, thanks to progressive policies and public support. However, the push for sustainability isn't confined to one part of the world. Manufacturing sectors in Asia and North America are increasingly acknowledging the benefits of adopting greener principles. Industry leaders emphasize that embarking on a sustainable pathway requires collaboration and commitment from all stakeholders, urging smaller firms to follow suit.
The journey toward holistic sustainability in manufacturing isn't without challenges. It requires significant investment, fundamental shifts in operational tactics, and a willingness to tackle unforeseen obstacles. Yet, the rewards are immense: reduced costs, enhanced brand reputation, and a solid contribution to combating climate change. The principles of sustainability are gradually becoming embedded within corporate cultures, shaping decision-making processes and future strategies. In doing so, manufacturing companies are not just enhancing their viability but also paving the way towards a more equitable and sustainable global economy. The manufacturing sector stands at a pivotal juncture, with decisions made today likely to define the industry's future trajectory.
Technological Advancements Driving Growth
The realm of manufacturing companies is as dynamic as it is expansive, with technological innovations acting as the heartbeat of its continuous evolution. The last decade has witnessed unprecedented growth driven by advancements that have redefined how the industry operates. One cannot talk about manufacturing today without mentioning the impact of automation and robotics. By replacing repetitive tasks, these technologies have not only increased efficiency but also enhanced precision, ensuring that quality remains uncompromised.
Consider the use of IoT, or the Internet of Things, which has been a game-changer for many top manufacturers. This technology allows machines to communicate with each other, leading to the creation of smart factories. Such establishments are capable of self-regulating and adapting, greatly minimizing downtime. This connectivity extends beyond machinery, as products themselves can be embedded with sensors, providing valuable data that manufacturers can use to improve their output. It's a fascinating mesh of interconnected devices that continuously share insights and contribute to optimizing the production process.
Additive manufacturing, more commonly known as 3D printing, has added another dimension to the sector. Originally used for prototyping, it has swiftly moved into mainstream production, allowing companies to reduce waste and customize products at a scale previously thought impossible. Imagine the thrill of printing a complex machine part on-demand, cutting down lead times and inventory costs dramatically. This flexibility has given birth to new business models where customers partake in the design process, creating tailor-made solutions that cater to individualized needs.
Artificial Intelligence and Machine Learning
No exploration of technological advancements in manufacturing can be complete without acknowledging the role of artificial intelligence and machine learning. These tools are being utilized to predict potential failures before they happen, thereby radically increasing machine uptime. Algorithms sift through mountains of data to spot patterns that might elude human eyes, enabling predictive maintenance and the anticipation of consumer demand trends. As manufacturing grows more complex, such foresight becomes invaluable.
"Innovation distinguishes between a leader and a follower." — Steve Jobs
Taking note of the role agile software plays in connecting various aspects of production provides insight into how the future may unfold for industry leaders. Digital twins, virtual replicas of physical devices and systems, offer ways to test and optimize setups within a virtual environment before actual implementation. This technology has proven immensely beneficial in reducing trial and error, saving both time and resources. Consider how these developments contribute to not only maintaining competitiveness but also setting benchmarks for the entire industry.
Augmented Reality (AR) has started to make its presence felt, offering new ways to bridge the gap between the digital and physical worlds. Engineers and technicians can overlay digital instructions directly onto machinery, reducing assembly and maintenance errors significantly. This intuitive way of blending digital tutorials with hands-on work not only enhances productivity but also boosts worker proficiency, turning potential novices into accomplished operators in record time.
As manufacturing companies continually chase innovation, the convergence of these technologies has given rise to more sustainable practices. They offer a pathway toward what is called Industry 4.0, representing a fusion of advanced production and operations techniques with smart digital technologies. This overhaul ensures the industry remains sustainable, future-proof, and, most importantly, ready to expand upon the possibilities of yesterday to tackle the challenges of tomorrow.
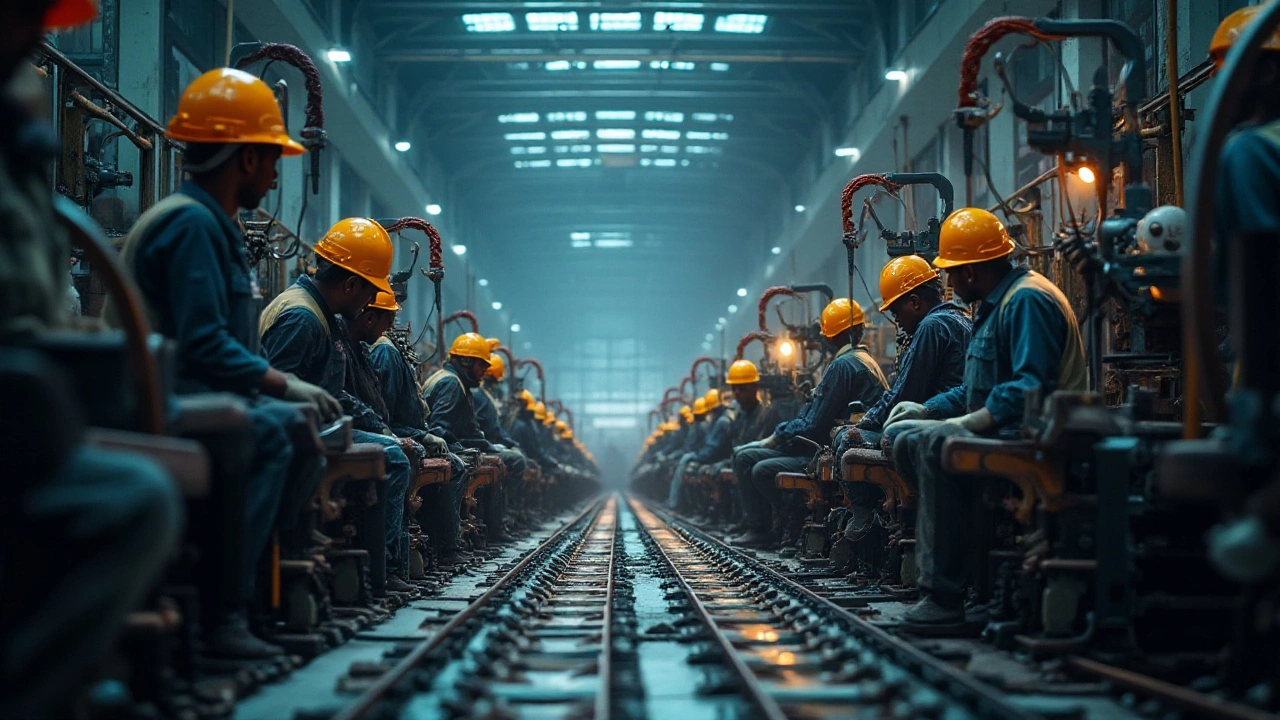
Evaluating Top Performers in the Industry
In the bustling realm of manufacturing, distinguishing the top manufacturers requires a keen understanding of various performance metrics. These companies aren't just churning out products; they're setting benchmarks in quality, efficiency, and innovation. To categorize a company as a top performer, one must look beyond mere scale or volume. Instead, it involves examining their adaptability to market demands, commitment to sustainability, technological integration, and even their ability to navigate geopolitical challenges.
One of the remarkable examples is Toyota, a name synonymous with quality and innovation in the automotive industry. Toyota’s success can largely be attributed to its unique production system, often referred to as the Toyota Production System (TPS). This method prioritizes efficiency and quality by minimizing waste, a practice that has inspired countless other industries. Another vital aspect is how giants like Siemens are leading by their investment in Industry 4.0 technologies. By harnessing the power of IoT and smart manufacturing, they’re not just increasing efficiency but also enabling a higher degree of customization, allowing them to stay ahead of consumer trends.
Looking into sustainability, Unilever has emerged as a paragon of ethical manufacturing. With initiatives aimed at reducing carbon footprints and promoting eco-friendly practices, Unilever has shown that profitability and sustainability can indeed go hand in hand. They have set ambitious goals for reducing plastic use and improving sourcing transparency, thus appealing to a socially conscious consumer base. A company's leadership in such areas vastly contributes to its standing as an industry leader. As a rule of thumb, exceptional companies are those that perform well across a spectrum of areas rather than excelling in just one.
When it comes to numbers, these companies also paint a statistically impressive picture. Take, for instance, the export numbers reported by leading manufacturing nations. According to a report by the International Federation of Robotics, global manufacturing companies have increasingly adopted automation, enhancing not only their production output but also maintaining product consistency at a lower cost. This strategic move to integrate robotics and AI has played a pivotal role in maintaining their competitive edge.
Industry leaders also draw significant attention through their workforce development strategies. Providing extensive training programs that upskill employees highlights their commitment to advancing human capital alongside technological capital. Promotions from within the company, loyalty programs, and career development opportunities create a more sustainable business environment and less workforce turnover. An outstanding example of this approach is evident in General Electric’s continued dedication to workforce education, which in turn has effectively fueled their strong market presence.
In critiquing these top performers, it becomes clear that success in manufacturing goes beyond production statistics. It's a balanced blend of people, resources, innovation, and ethics. As Maya Angelou once said,
"You can't use up creativity. The more you use, the more you have."The same is valid in manufacturing. These industry leaders continuously innovate, adapt, and grow not just to thrive, but to define the future of the manufacturing landscape.