Lean manufacturing stands as a powerful philosophy shaping the modern production landscape. At its core lie the 4Ms—Man, Machine, Material, and Method—each a critical cog in the manufacturing wheel. These elements collectively drive efficiency and waste reduction, leading to a smoothly run production floor. Understanding how these components work in harmony can significantly enhance manufacturing processes.
In today's fast-paced industrial world, companies strive to be lean, not just in scale but in operation, fostering an environment where productivity thrives and resources are wisely used. This concept isn't just about cutting costs; it's about creating more value with less. Together, the 4Ms provide a framework for businesses looking to navigate and lead in the competitive landscape of manufacturing. Let's explore how each of these elements can transform production into a streamlined, efficient powerhouse.
- Introduction to Lean Manufacturing
- Exploring the 4Ms
- Man: The Human Element
- Machine: Tools and Technology
- Material: Resources and Utilization
- Method: Processes and Improvement
Introduction to Lean Manufacturing
Lean manufacturing is more than just a trend; it's a transformative approach that has taken the world by storm. Originating from the production lines of Toyota in Japan, it advocates for a systematic method of waste minimization while maximizing productivity. The idea behind lean principles is elegantly simple: use fewer resources to achieve more. What sets lean manufacturing apart is its emphasis on respecting human elements and encouraging continuous improvement, known in Japanese as 'kaizen.'
In today's dynamic industrial landscape, companies are constantly seeking ways to enhance efficiency without compromising quality. This is where lean manufacturing shines, offering a proven pathway to operational excellence. The approach tackles the so-called 'seven wastes'—overproduction, waiting time, transport, extra processing, inventory, motion, and defects—that can bog down production processes. These waste elements can appear trivial but, when scrutinized and addressed, result in significant performance upgrades.
Lean manufacturing has extended beyond the automotive sector, its early proving grounds, and now finds applications across various industries from healthcare to software development. The versatility of these principles underlines their importance in a competitive market. As Henry Ford once said, "Coming together is a beginning, staying together is progress, and working together is success." This resonates well within the lean framework, where collaboration and teamwork sit at the core of the production strategy. Transforming a manufacturing floor to follow lean principles doesn’t happen overnight. It requires a commitment from all levels of a company, emphasizing that change begins with leadership buy-in and permeates down to every worker.
Implementing lean manufacturing doesn’t just mean slashing costs and downsizing operations. Instead, it's about creating more value for customers without exhausting resources. Savvy companies recognize lean as not merely a set of tools but a culture that engenders efficiency and enhances competitiveness. Recent reports indicate that businesses adopting lean methodologies have witnessed a reduction in lead times by 50% and inventory levels by 30%.
Creating such marked improvements involves understanding and applying the cornerstone 4Ms of lean—Man, Machine, Material, and Method—which together foster a methodical, well-rounded approach to manufacturing. These elements promote a balanced integration of technology and human skills, facilitating robust production systems that can adapt swiftly to market demands. Embracing lean means embarking on a journey of continuous adaptation and learning. But with the prospects of greater productivity and customer satisfaction, it is a journey worth taking.
Exploring the 4Ms
The dynamic world of lean manufacturing revolves around the pivotal concept of the 4Ms: Man, Machine, Material, and Method. These elements are not merely components of a system; they are the lifelines of an efficient and responsive production process. Each M embodies a separate dimension of manufacturing, with unique challenges and opportunities for enhancement. Alone, each facet carries its weight, but when orchestrated effectively, they become a symphony of productivity and effectiveness.
Man, the human element, brings skills, creativity, and decision-making capabilities to the forefront. Workers are often seen as the heart and soul of manufacturing operations. It's their expertise that drives innovation on the production floor. It is crucial for businesses to invest in their workforce—offering continuous training, fostering a positive workplace culture, and ensuring safety. After all, an engaged and motivated workforce results in higher productivity, better quality, and less waste. A famous quote from the lean manufacturing guru, Taiichi Ohno, captures this beautifully:
“People don't go to Toyota to work, they go there to think.”
Machine represents the tools and technology that amplify human efforts. The relationship between man and machine defines the efficiency of the manufacturing process. Investing in modern machinery and maintaining it adequately ensures minimal downtimes and maximum productivity. The rise of Industry 4.0 technologies, such as the Internet of Things (IoT) and Automation, has transformed how machines are operated, paving the way for more intelligent and interconnected manufacturing systems.
The Material component addresses the importance of raw inputs in production. Its availability, quality, and cost significantly affect the outcome of manufacturing efforts. Ensuring a reliable supply chain and keeping inventory levels optimized can lead to significant cost savings and enhanced operational efficiency. In a recent survey, it was found that efficient material management could reduce production costs by up to 20%. The emphasis is on reducing waste, using high-quality inputs, and maintaining just-in-time inventory to keep the production line moving smoothly.
Finally, the Method refers to the processes and strategies employed to produce goods. Lean manufacturing champions methods that eliminate waste and add maximum value to the end product. By refining processes and implementing standardization, companies can ensure consistent quality while reducing cycle times. Adopting methodologies such as Six Sigma or the 5S system can create a robust framework for continuous improvement, fostering a culture where innovation and efficiency become the norm. Empowering employees to contribute to method improvements ensures that processes evolve to meet the changing demands of the market.
In the modern manufacturing era, understanding and mastering the 4Ms are essential for companies aiming for excellence. It's a journey of continuous improvement, where every department and every individual is engaged in optimizing the manufacturing ecosystem. Ultimately, the 4Ms aren't just about reducing costs—they're about enhancing value, ensuring sustainability, and fostering innovation in a competitive landscape.
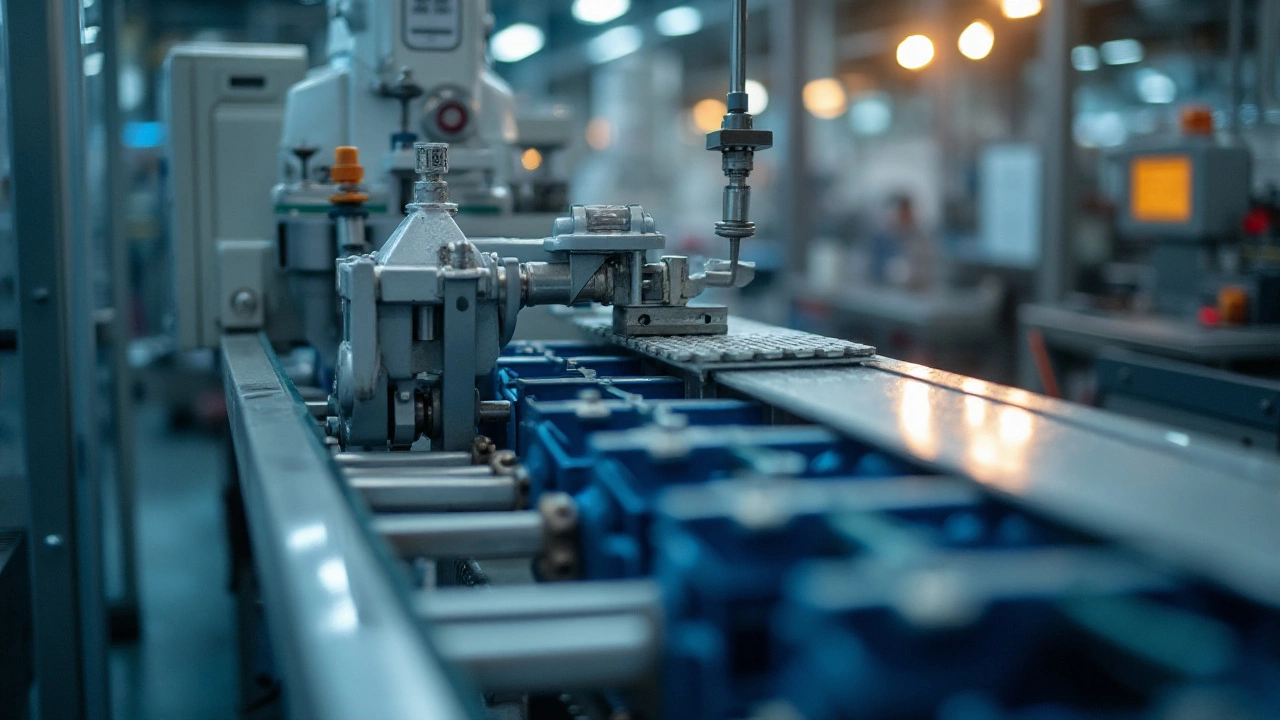
Man: The Human Element
The role of humans in the world of lean manufacturing is unparalleled. Behind every machine, material, and method are skilled individuals who bring these elements to life on the production floor. These workers are the heart and soul of manufacturing, offering creativity and adaptability no machine can replicate. In recent years, there’s been a seismic shift towards recognizing the importance of investing in the workforce to drive efficiency. This involves comprehensive training and fostering a culture of continuous improvement, where employees are empowered to contribute ideas and insights for better production outcomes. The human element is about more than just manual labor; it includes critical thinking, decision-making, and problem-solving abilities that enhance production quality and reduce errors.
A well-trained workforce not only boosts morale but also significantly impacts the bottom line. A happy, engaged employee is more likely to identify inefficiencies and suggest improvements, thereby reducing waste. According to a study by the Manufacturing Institute, companies that invest heavily in employee training reportedly see a 15% to 25% increase in productivity. This makes the strategy a favorite among firms looking to excel in lean manufacturing. Emphasizing training requires structured programs tailored to the skill needs of employees, which in turn builds a robust talent pool, ready to tackle future challenges. Contributing to this concept, a respected industry leader, Jack Welch, once noted,
"Before you are a leader, success is all about growing yourself. When you become a leader, success is all about growing others."This highlights the intrinsic value in developing each individual's skills and potential.
When approaching lean manufacturing with the human element in mind, it is vital to explore how workplace ergonomics and design can impact efficiency. Ergonomically designed workspaces reduce the risk of injury and fatigue, which are common bottlenecks in production environments. Employers who invest in ergonomic improvements often see a decrease in work-related injuries by almost 30%, according to OSHA reports. These workspace considerations directly translate to enhanced worker productivity and satisfaction. Implementing ergonomic solutions is a strategic move to ensure workers can perform their roles effectively without the burden of physical strain, allowing for a more dynamic production environment.
Technology also plays a transformative role in enhancing the capabilities of the human element. With advancements in automation, humans are no longer restricted to repetitive tasks but rather are encouraged to engage in overseeing and controlling these new-age technologies. This integration enhances efficiency across the board, as skilled workers can utilize tools that assist in real-time decision-making and monitoring of production. In this way, technology empowers workers to optimize processes without feeling bound by the limitations of manual execution. Organizations that successfully pair human ingenuity with technological advancements stand at the frontier of modern manufacturing excellence.
Machine: Tools and Technology
In the realm of lean manufacturing, the 'Machine' stands as a testament to human ingenuity and innovation. Machines are more than just tools—they are the backbone of industrial productivity, driving the efficiency of production lines. Their importance can't be overstated in a world that constantly seeks to automate and improve processes. Industrial machinery ranges from simple, manually operated apparatus to highly complex, computerized systems that execute intricate tasks with precision. Emphasizing efficiency, every machine must adapt to the rapidly changing demands of modern manufacturing environments. The technology integrated within these machines plays a crucial role in determining a facility's output and quality.
The evolution of machines has been profound; from steam engines that heralded the first industrial revolution to today's AI-powered robots, the journey has been marked by groundbreaking milestones. These advancements have allowed manufacturers to produce goods at an unprecedented scale and speed. For instance, CNC (Computer Numerical Control) machines have taken over the precision tasks of cutting and shaping materials, delivering consistency that manual processes could never achieve. Their ability to operate with minimal human intervention not only boosts productivity but also reduces human error and waste, aligning perfectly with the lean philosophy.
Technology plays a critical role in maintaining the integrity and efficiency of production lines. Modern industry leaders incorporate IoT (Internet of Things) to connect all pieces of manufacturing equipment, enabling seamless communication and data transfer. This interconnectedness offers real-time monitoring and maintenance updates, allowing for predictive maintenance and reducing downtime significantly. By predicting when machines will likely fail, companies can schedule interventions before problems arise, saving considerable time and cost. A study by the World Economic Forum suggests that integrating IoT in manufacturing can increase productivity by up to 25%.
Another crucial aspect of machinery in lean manufacturing is energy efficiency. As environmental consciousness grows, industries aim to minimize their carbon footprint. Achievements in engineering have led to the development of machines that consume less energy while maintaining, or even increasing, output levels. Energy-efficient equipment not only contributes to a healthier environment but also reduces operating costs in the long term.
Embracing cutting-edge technology requires substantial investment. It's not just about buying the latest equipment—it's also about training staff to use these machines efficiently. Regular training programs ensure that workforce skills are aligned with technological advancements, maximizing the potential benefits of new equipment. The organizations that succeed in this endeavor realize technology is not a one-time purchase but a strategic, ongoing partnership. As the famous Japanese engineer Taiichi Ohno once noted, "Having no problems is the biggest problem of all." This reflects the continuous improvement culture vital in lean practices, with machines at the very heart of such progress.
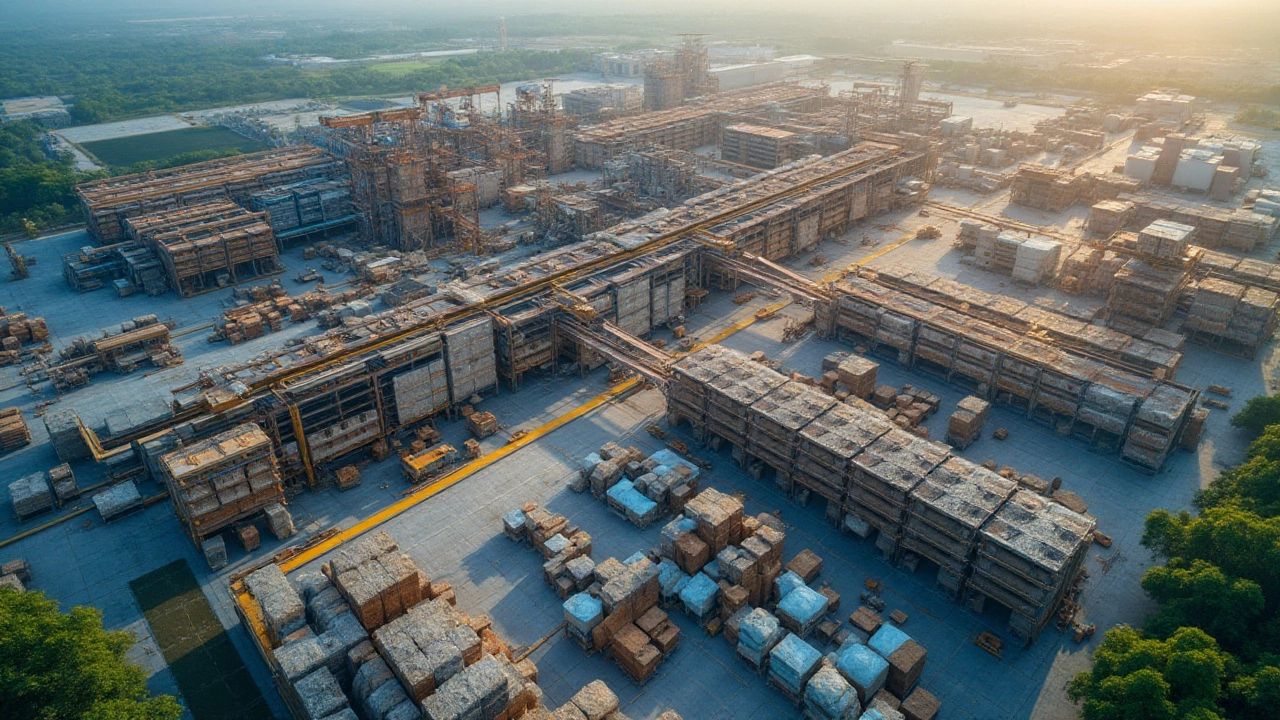
Material: Resources and Utilization
Central to the principles of lean manufacturing is the effective management of materials. Often considered the lifeblood of any production process, materials dictate both the quality of the final product and the efficiency of its production. Proper material management involves everything from ensuring adequate supplies and minimizing waste to maximizing the use of materials through innovative design and process adjustments. Each of these steps is crucial in ensuring that production lines operate smoothly without the disruptions that can occur when materials are mishandled.
The first step in optimizing material utilization involves forecasting the required analytics precisely. Businesses must frequently assess how much material is needed by deeply analyzing historical data and future demand projections. This ensures not only that supply meets demand but also that excess stock doesn't pile up, which can tie up valuable capital and lead to wastage due to spoilage or obsolescence. By closely aligning purchase orders with production schedules, companies can maintain a lean inventory.
Moreover, waste reduction is a key component of lean material management. It's not enough just to have the right materials on hand; manufacturers must be diligent about how these materials are used. Consider implementing a zero-waste philosophy, which encourages repurposing scrap or leftovers where possible. A case study from Toyota, a pioneer in lean practices, revealed their process of meticulously reusing scrap metal, which not only saved them millions but also aligned with broader environmental responsibility goals. This culture of minimizing waste extends not only to the materials themselves but also to the packaging and transportation used in the supply chain.
Innovative Design and Process Adjustments
Innovation in product design can yield significant improvements in material utilization. By reimagining how components fit together or choosing alternative materials that offer the same strength or flexibility at a lower cost, companies can save both money and resources. Take, for example, the aerospace industry, where composite materials are increasingly replacing traditional metals. Composites provide the same durability at a fraction of the weight, leading to fuel savings and reduced environmental impact—a win-win for the industry and the planet.
Perhaps one of the most overlooked aspects of materials management is the training and involvement of employees. Engaged workers who understand the importance of efficient material use can be some of the best assets in identifying areas where waste occurs and suggesting improvements. Developing a culture of continuous improvement, or Kaizen—a central philosophy in lean manufacturing—encourages employees at all levels to contribute to better material practices.
Implementing technology can significantly enhance material management practices. Smart sensors and inventory management software can provide real-time updates on material usage and alert managers to discrepancies or shortages. By automating these processes, companies enable employees to focus on more strategic tasks rather than being bogged down by routine administrative duties. As per a study conducted by McKinsey & Company, firms implementing advanced analytics reported an increase in productivity by 20-25%, highlighting the vast potential for growth through technological integration.
"The lean approach to materials encourages a balance between waste reduction and value creation, crucial for sustainability in today's manufacturing industries." — Lean Institute
Efficient material utilization is not just a bottom-line issue; it's part of a broader commitment to sustainable production practices. By integrating advanced planning, waste reduction efforts, innovative design, and employee engagement, businesses can dramatically improve their operations. Through these efforts, not only do organizations enhance their economic efficiency, but they also reinforce their commitment to a sustainable future.
Method: Processes and Improvement
In the realm of lean manufacturing, the Method represents the intricate processes that guide production towards efficiency and precision. It is more than just a set of instructions; it is a carefully crafted series of actions designed to optimize each stage of manufacturing. By streamlining these processes, businesses can ensure a consistent and high-quality output, reducing waste and maximizing resource utilization.
To truly understand the power of an optimal Method, one must identify bottlenecks—those points in the production line where slowdowns occur. Addressing these issues often requires a creative approach, where flexible thinking aids in breaking down old barriers. Developing a robust system that monitors every aspect of production can alert manufacturers to potential problems before they escalate. Regular feedback loops should be established to provide a constant stream of improvements. This proactive strategy allows for continuous refinement, aligning with the lean principle of relentless enhancement.
Continuous improvement often revolves around the Japanese concept of Kaizen, which means 'change for the better.' This philosophy encourages all employees, regardless of rank, to suggest improvements actively. Embracing such ideas not only facilitates innovation but creates a culture of teamwork and shared responsibility. When everyone is involved in the quest for betterment, the collective knowledge of the workforce becomes a formidable asset.
"Success is a journey, not a destination. The doing is often more important than the outcome," once admired business thinker Arthur Ashe explained, emphasizing the process itself as a crucial component of improvement.
Integration of modern technology is indispensable within these methods. Advanced data analytics and machine learning algorithms play a role in predicting trends and optimizing workflows. In fact, companies that adopt digital solutions see productivity increases of up to 20%. Sensors and IoT devices can provide real-time data, helping operators make informed decisions quickly. Automation tools further grant efficiency in routine tasks, liberating human workers to focus on more complex challenges.
The Method is at its most effective when informed by meticulously collected data. Statistical tools like Six Sigma provide insights into process variability and help in achieving unprecedented control levels. Such data-driven approaches foster an environment where issues are tackled based on evidence rather than assumptions. Establishing standardized procedures can also result in significant gains, as consistency often drives excellence.
Ultimately, the objective of improving Methods in manufacturing is not only about achieving optimal efficiency but about creating a resilient system that can adapt to change. As market demands evolve, so too must the Methods by which goods are produced. Staying ahead of the curve allows manufacturers to set trends rather than follow them. By implementing these strategies, businesses can reinforce their foundation, ensuring not just survival but prosperity in the rapidly evolving industrial landscape.