In the evolving domain of food processing, precise measurement standards are not just a necessity; they are the backbone that ensures product quality and safety. MTS, or Measurement Type System, is a critical component in this ecosystem, shaping the way industries maintain uniformity in their production lines.
But what exactly does MTS encompass? This concept integrates systematic approaches to quantify and control various processes, making it essential for maintaining the integrity of food products from start to finish. We'll explore the significance of MTS in food processing, unraveling its principles and how it aligns with industry standards.
From small batch productions to large-scale manufacturing, understanding and implementing MTS can transform efficiency levels and enhance product reliability. Join us as we delve into this integral aspect of the food industry, offering practical insights and tips on adopting MTS effectively in your operations.
- Defining MTS in Measurement
- Importance in Food Processing
- Core Principles of MTS
- Applications in the Industry
- Tips for Implementing MTS
Defining MTS in Measurement
Measurement Type System, often abbreviated as MTS, is a pivotal framework within the food processing industry. It serves as a standardized protocol for gauging various parameters integral to the manufacturing process. At its core, MTS ensures that the measurements used in production are not only accurate but also consistent across different batches. This level of precision is vital in an industry where minor discrepancies can lead to substantial variations in product taste, quality, and safety. For example, consistent temperature control during pasteurization is necessary to eliminate harmful microorganisms without compromising the product's nutritional value.
An MTS isn't just restricted to weights and volumes; it extends into several other crucial areas such as time, temperature, pressure, and humidity. These factors significantly impact the texture, flavor, and preservation of food products. Integrating MTS into a food processing unit requires a detailed understanding of each stage of production and the potential points of deviation that might arise. Implementing such a system can be complex but offers a high payoff in terms of ensuring edible goods meet rigorous quality standards.
Historically, the need for standardized measurements originated from the global exchange of goods. As different countries traded their culinary specialties, the lack of a unified measurement system often led to misunderstandings and inconsistencies. In response, scientists and industry leaders collaborated to develop frameworks like MTS that could transcend regional differences. Today, these measurements are bolstered by advancements in technology, such as automated data collection and analysis systems. "The harmonization of measurement units has become a cornerstone for international trade," says Dr. Eleanor Shaw, a food scientist whose research has underpinned many industry standards.
To successfully implement an MTS, food processing units must adhere to specified protocols that guide measurement activities. It often includes adopting calibrated measuring equipment, regular employee training, and continuous monitoring to ensure compliance. The adoption of such a system is usually accompanied by setting benchmarks against which all measurements are compared. These benchmarks help identify deviations and prompt corrective actions before they escalate into significant issues. The use of robust MTS practices can lead to increased operational efficiency, minimized waste, improved product quality, and higher consumer satisfaction.
Importance in Food Processing
In the arena of food processing, the MTS framework is not just an add-on; it's an essential tool that underpins the efficiency and reliability of operations. It orchestrates the accuracy that industries need to meet both consumer expectations and regulatory standards. Measurement Type System (MTS) ensures that every product is crafted with the utmost precision, which is crucial in a field where quality cannot be compromised. By safeguarding measurement accuracy, MTS helps in reducing wastage, optimizing resources, and thus enhancing profitability.
The implementation of MTS goes beyond just ensuring consistency. It plays a pivotal role in risk management by identifying potential inconsistencies before they cascade into larger issues. With food safety being a paramount concern, MTS becomes indispensable for regulatory compliance and consumer trust. For instance, if a batch of processed food falls outside predefined quality parameters, MTS helps pinpoint the anomaly swiftly, allowing for quick corrective actions.
Food processing units rely heavily on the ability to replicate processes with high accuracy. This requirement becomes increasingly critical when scaling operations to meet growing demands. Here, MTS seamlessly integrates process parameters across different scales without losing precision. A consistent MTS application can also foster innovation by allowing teams to experiment with new recipes and processes while maintaining control over variability.
As Jane Doe, a renowned food science expert, once put it,
"The cornerstone of food processing excellence lies in our ability to measure with precision, predict outcomes, and perfect every batch produced.”Such precision forms the bridge between traditional methods and the state-of-the-art technologies prevalent today, encouraging a balance of art and science in food manufacturing.
Moreover, within the landscape of sustainable practices, MTS contributes significantly by promoting efficient use of resources. The detailed measurement controls prevent overuse of raw materials and energy, contributing to reduced environmental impact. Supporting this are various technologies that seamlessly integrate with MTS, offering real-time data insights and predictive analytics.
Here's a glimpse into how MTS impacts food processing industries:
Aspect | Impact |
---|---|
Resource Utilization | Optimizes raw material use, cutting costs and waste |
Quality Control | Ensures product consistency and safety |
Operational Efficiency | Reduces downtime and improves throughput |
Sustainability | Minimizes environmental footprint |
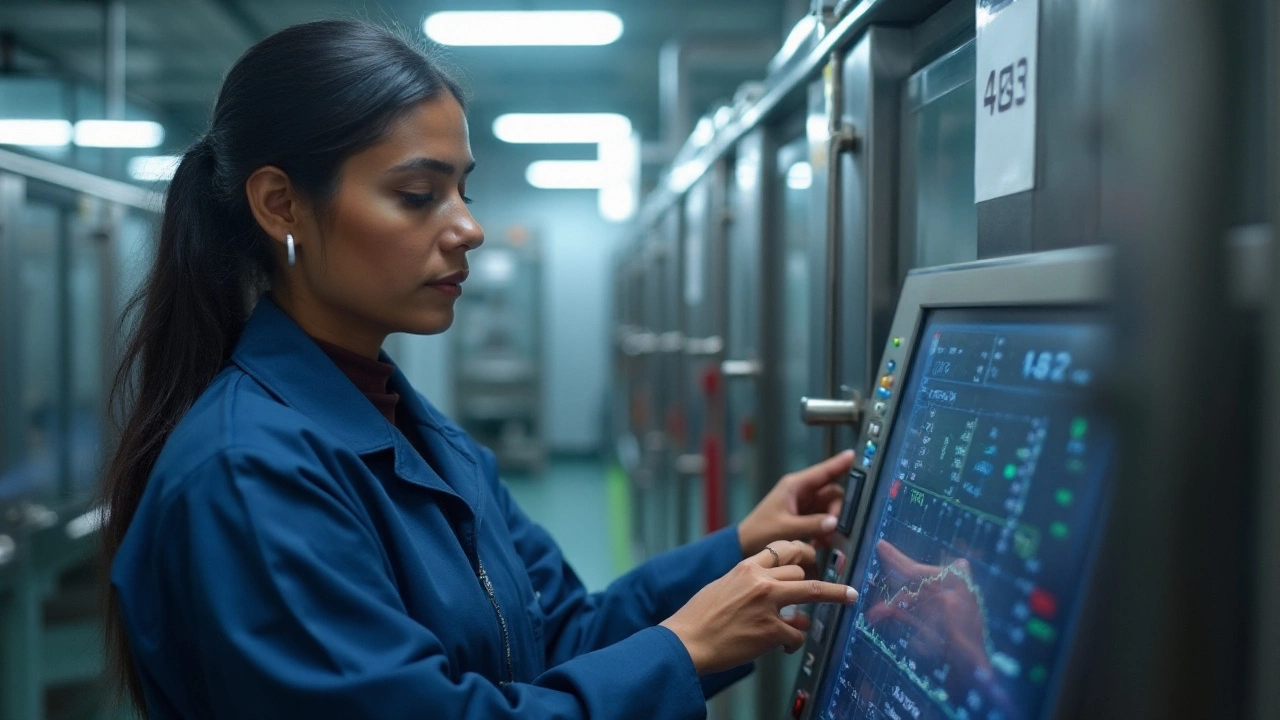
Core Principles of MTS
In the realm of food processing, understanding the Core Principles of MTS is akin to grasping the heartbeat of the entire operation. These principles are deeply embedded in the pursuit of perfection and efficiency within this dynamic industry. At the heart of MTS is the ambition to harmonize precision with practicality, ensuring every unit of measurement aligns seamlessly with the intended outcome. This starts with a keen focus on establishing universally accepted measurement standards that transcend the boundaries of local practices. The introduction of these principles has provided the industry with a solid foundation upon which quality and consistency are built.
Consistency, as it turns out, is not merely a desirable quality; it's a necessity. Strong measurement standards ensure that every batch of products meets the same exacting criteria, crucial in an age where consumer expectations are higher than ever. A central tenet of MTS is accuracy, and this is achieved through meticulous calibration of tools and machinery used in measurement processes. Regular audits and recalibrations are not just routine; they are fundamental to maintaining the integrity of these systems. The tireless pursuit of accuracy breeds trust not only within the production team but also with end consumers, for whom quality assurance is paramount.
Ensuring Accuracy and Reliability
Continuing with the principles of precision and consistency, MTS relies heavily on a system of checks and balances designed to catch and correct deviations before they affect the final product. This approach is often likened to the role of an orchestra conductor ensuring every instrument plays in tune. By incorporating advanced technologies like AI and machine learning, MTS adapts to the ever-evolving landscape of food production, continually scaling its measures to match the demand for sustainable practices. This continual adaptation is critical in mitigating wasteful practices, optimizing resources, and ultimately enhancing productivity on a broad scale. A fascinating statistic from 2023 indicated that companies integrating MTS strategies reported a 25% reduction in production errors. Such real-world impacts highlight the tangible benefits of these core principles in food processing.Another aspect of MTS involves rigorous documentation. Keeping detailed records of every measurement process captures fluctuations and discrepancies while providing a vast pool of data for future reference and improvement. It's this meticulous record-keeping that allows teams to not only identify trends and anomalies but also to forecast potential challenges before they escalate into critical issues. As a celebrated food scientist once said,
"The essence of quality is the precision with which we measure."This quote encapsulates the ethos that drives the MTS framework forward.
Integration with Technology
Incorporating technology into MTS is not an afterthought but a strategic initiative that transforms potential into reality. Automation and digital measurement systems are now pivotal in ensuring the rapid, accurate transfer of data across different segments of the production line. These systems minimize human error and accelerate processes without compromising on the quality of information gathered. As we move towards more digitized systems, the principles of MTS evolve too, paving the way for more sophisticated, yet user-friendly interfaces. With technology enhancing data accuracy and timeliness, MTS offers a future-proof strategy crucial for any food processing unit aiming to remain competitive.Applications in the Industry
The MTS framework has firmly established its critical role within the food processing industry. Its integration into various stages of production has streamlined operations and elevated quality control measures. One of the primary applications is in the standardization of measurements across different food processing units. This ensures consistent quality, taste, and packaging across batches and locations. For instance, in a factory producing canned soup, MTS helps ensure that each can holds the precise amount of ingredients, maintaining the balance of flavors consumers expect.
Another important application is in the calibration of machinery. Industrial machines require precise settings to function effectively, and MTS provides a benchmark for tuning these machines to their optimal performance. Whether it's a pasteurization unit that must heat products to specific temperatures or a packaging line that needs exact measurements to avoid waste, MTS becomes invaluable. According to an industry expert, "Measurement consistency can significantly reduce operating costs by minimizing material waste and energy consumption."
Quality assurance processes are another arena where MTS application shines. By providing concrete metrics, it allows quality control teams to assess product standards objectively. This is particularly crucial in industries where hygiene and safety are paramount, such as dairy processing or ready-to-eat meals production. Through MTS, potential production flaws can be detected and corrected early, saving both time and resources.
Moreover, MTS plays a strategic role in the supply chain management of the food industry. By having defined metrics and measures, companies can enhance their inventory management and reduce the likelihood of stock shortages or overproduction. Automated systems can utilize MTS data to make real-time adjustments to supply orders, ensuring that materials are used efficiently and costs are kept under control. In a competitive market, this ability to respond adeptly to demand shifts is a game-changer.
Finally, consumer satisfaction is heavily influenced by the applications of MTS. When customers purchase a product, they expect consistent quality. If one batch differs in taste or texture from another, it can severely impact brand reputation. MTS ensures that consumers receive the reliable quality they expect, thereby enhancing brand loyalty and customer trust.
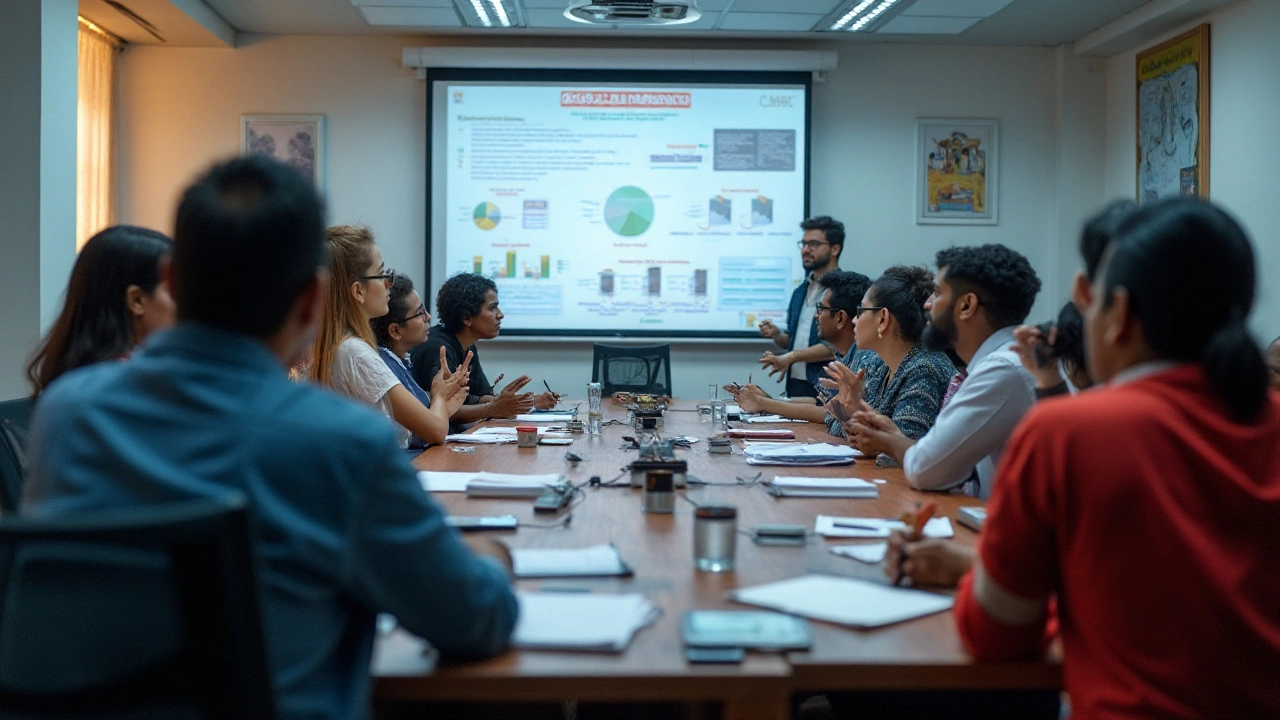
Tips for Implementing MTS
Embarking on the journey of integrating MTS within food processing environments begins with a comprehensive understanding of its components. The integration process is an amalgam of understanding, planning, and efficient execution. It's crucial to start by evaluating the current measurement systems in place. Knowing what exists allows for a clearer picture of what changes or enhancements are necessary. Engaging with the quality assurance team is vital, as they possess insights on past discrepancies and areas needing improvement. By collectively discussing these elements, a roadmap can be devised that sets the tone for successful implementation.
The essence of a successful MTS implementation lies in detailed calibration. Precise calibration ensures that measurements during processing are not just accurate but consistently reliable across all product batches. One must consider using advanced, industry-standard calibration tools and software. These tools can seamlessly integrate into the existing infrastructure, enhancing the measurement process efficiently. In the words of measurement expert Dr. Clarke, "Consistent calibration isn't just a step in the process, it's a cornerstone for reliable food production standards." Such consistency in measurements bridges the gap between production and quality assurance.
After calibration, staff training emerges as a crucial aspect to ensure smooth adaptation and utilization of the new system. A well-trained staff can significantly minimize errors and optimize food processing efficiency. Training sessions should emphasize the importance of accurate data recording and understanding results outputted by the systems. Investing time in training is a long-term benefit, not just a checkbox mark in the implementation plan.
Maintaining a robust feedback loop is another significant practice. Collecting insights from both the operational floor staff and the management can reveal valuable information about the daily operation hurdles and strategic alignment. These insights should then be analyzed systematically, leading to iterative improvements in the measurement Type System integration. Having a dynamic feedback mechanism ensures that the system evolves with production requirements and industry standards.
Leveraging Technology for MTS
Introducing advanced technology solutions is your ticket to the future of food processing measurements. Technology acts as a catalyst promoting seamless data sharing across departments, thus ensuring every decision is data-backed and strategic. Deploying IoT (Internet of Things) in measurement tools allows for real-time monitoring and swift adjustments in processes, driving efficiency to new heights. Moreover, cloud-based platforms facilitate data storage and access, enabling informed decisions with historical data analysis at their core.
Finally, setting measurable goals and benchmarks within the MTS framework keeps the entire implementation on track. Establishing clear and achievable milestones helps assess progress and make necessary adjustments swiftly. This proactive approach not only refines the MTS process but also aligns it with the broader organizational objectives, fostering a culture of continuous improvement.