Alright, let's talk plastic! Ever stopped to think about where manufacturers actually get all that plastic we see everywhere? Surprisingly, it's not just a single path from oil to your hands—it's a whole journey.
First off, most plastics start life as petrochemicals derived from crude oil and natural gas. Companies tap into these resources because they're abundant and, importantly, economically viable. But it's not as straightforward as just digging up some oil and turning it into plastic.
There's plenty more to the picture, like recycling, which gives used plastic a second life. Businesses have realized that recycling isn't just good PR—it's also a smart way to reduce costs and environmental impact.
- The Raw Materials Behind Plastic
- Recycling: A Second Chance for Plastic
- Bioplastics: An Eco-friendly Alternative
- The Future of Plastic Sourcing
The Raw Materials Behind Plastic
So, where does plastic really come from? Let's break it down. At its core, most plastic is made from petrochemicals—these are chemicals that come from petroleum or natural gas. Why these? Simply put, they're cheap and pretty easy to get ahold of. Around 4% of the world's oil production goes directly towards making plastic.
Petroleum and Natural Gas
First, let's look at petroleum's role in plastic manufacturing. It all starts when we extract crude oil from deep underground. This oil is then refined to separate out different components, including naphtha, which is crucial for making many types of plastic.
Natural gas joins the party here, too. Companies use a part of the gas called ethane to create another critical ingredient in the plastic-making process. Together, these form the backbone for a huge range of plastics we use daily.
The Polymerization Process
Once these raw materials are refined, the magic really happens. The extracted chemicals undergo polymerization—where small molecules called monomers join together to form long molecular chains known as polymers. Think of it like linking up sections of a toy train: more links mean a longer train.
Depending on the monomers and polymerization techniques used, you get different plastics with unique properties. For instance, polystyrene from styrene monomers becomes that foam cup, and polyethylene makes up your grocery bags.
Some Interesting Numbers
The sheer amount of plastic produced is staggering. According to recent data, global plastic production was around 390 million metric tons annually. The world demand doesn't seem to slow either, with more innovative applications popping up constantly.
A Peek at Supply Chains
Once manufactured, these plastic suppliers ship their products worldwide. Logistics here are key, making sure raw materials get to the right places without wasting time or resources. It's not just about getting plastic from point A to point B; it's about doing it efficiently.
Recycling: A Second Chance for Plastic
Diving into the world of plastic sourcing, recycling stands out as a game-changer. Imagine giving discarded plastics a new lease on life—it’s exactly what happens through recycling. Now, how does this process fit into the bigger picture of plastic manufacturing?
Recycling involves collecting used plastic materials and transforming them back into useful products. This might sound straightforward, but there's a bit more to it. The magic happens in facilities where plastics are sorted, cleaned, and then melted down. From here, they're remolded into new shapes and forms, ready to be used again.
Types of Recyclable Plastics
Not all plastics are made equal, and consequently, not all are recyclable. Commonly recycled materials include PET (think soda bottles) and HDPE (like your typical milk jug). These materials have a high demand because they can be easily reprocessed into new products.
The Benefits
- Environmental Impact: Recycling reduces the need for virgin materials, thus conserving resources and cutting down on energy consumption.
- Economic Advantage: By reusing plastics, manufacturers can cut costs on raw materials.
- Waste Reduction: Less plastic ending up in landfills eases the burden on our waste management systems.
For some perspective, check out this data table showing plastic recycling rates over the years:
Year | Recycling Rate |
---|---|
2020 | 8.7% |
2021 | 9.5% |
2022 | 10.1% |
As you can see, there's progress, but room for improvement. By making recycling a bigger part of plastic suppliers' operations globally, the industry's ecological footprint could shrink significantly.
In short, recycling isn't just about reusing materials—it's a critical part of moving towards a sustainable future in the plastic manufacturing industry.
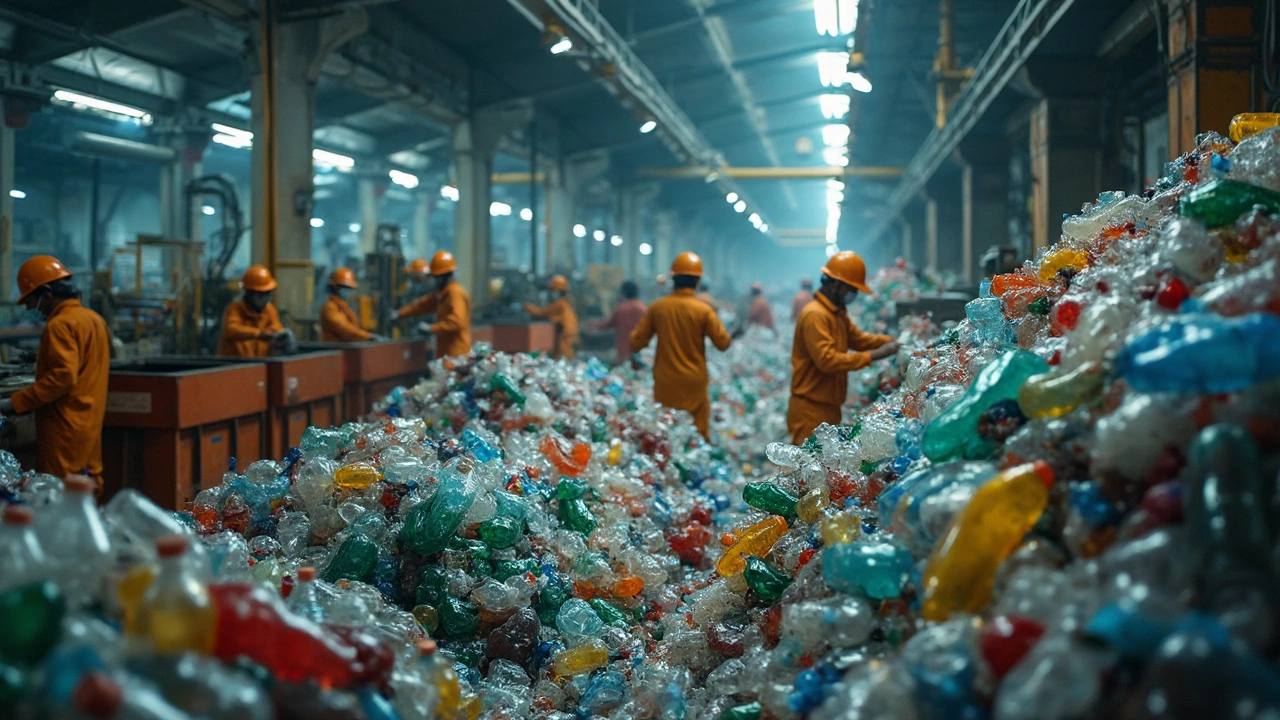
Bioplastics: An Eco-friendly Alternative
Switching gears now, let's chat about bioplastics. These are gaining traction as a more sustainable option in the world of plastic manufacturing. So what are they exactly? Bioplastics are derived from renewable sources like corn, sugarcane, and even potato starch, instead of traditional petrochemicals.
Understanding the Basics
You know what's cool? Bioplastics not only reduce reliance on fossil fuels but also have the potential to lower greenhouse gas emissions. How's that for a win-win? But here's the thing—bioplastics are not automatically biodegradable. Some are, some aren't, and it all depends on their composition.
The Types of Bioplastics
- PLA (Polylactic Acid): Made from fermented plant starch like corn, it's widely used for containers and food packaging.
- PHA (Polyhydroxyalkanoates): Produced by bacteria that ferments sugar, these are completely biodegradable and used in medical applications.
Pretty interesting, right?
The Adoption Challenge
While bioplastics sound perfect, the transition isn't without hurdles. Currently, they account for just 1% of the total plastics market. Why? Well, cost is a big factor, plus there's still a learning curve in processing bioplastics on a large scale.
However, as technology improves and economies of scale kick in, the price is likely to drop, making them a more feasible option for plastic suppliers worldwide.
Case Study: The Positive Impact of Bioplastics
In a 2024 study, it was found that switching to PLA could lead to a 25% reduction in carbon footprint for packaging materials. That's serious progress towards cleaner production!
From an environmental perspective, investing in bioplastics promises not just a cleaner planet but also aligns manufacturers with growing consumer demands for eco-friendly products. It's a fascinating pivot and one that's full of potential if we can crack the supply and cost issues.
The Future of Plastic Sourcing
Alright, so what's next for the world of plastic manufacturing? As we become more eco-conscious, the hunt for sustainable alternatives is heating up. Manufacturers are looking at everything from algae-based materials to advanced recycling methods to innovate the future of plastic sourcing.
Bioplastics: Leading the Charge
Bioplastics are a big deal right now. Made from renewable sources like corn starch or sugarcane, these materials are biodegradable, reducing their impact on the environment. Though they account for only about 1% of global plastic production today, their share is growing as more companies hop on the green bandwagon.
Recycling: Going Full Circle
Recycling's been around for a while, but new tech is taking it to the next level. We’re not just talking about melting down old water bottles. Companies are developing chemical recycling, which breaks down plastic to its molecular components, allowing for nearly endless reuse cycles. This is a game-changer, especially for plastic suppliers looking to cut waste.
Here's a quick look at the potential recycling progress in numbers:
Year | Projected Recycling Rate |
---|---|
2025 | 20% |
2030 | 30% |
2040 | 50% |
Government Policies and Innovations
Governments worldwide are also playing a part, with some big players implementing strict regulations to limit single-use plastics and incentivize recycling and innovation. This pressure is pushing companies to rethink the entire life cycle of their products.
The future of plastic sourcing will likely be a mix of traditional methods with these new innovations. It's a stirring time in the industry, with a real push to balance economic viability with environmental responsibility. As consumers become savvier, manufacturers will need to keep up.