Ever thought about what goes into those shiny Ford cars on the road? Well, it turns out, quite a lot of steel! The Ford Motor Company doesn't just call any random supplier when they need steel; they have a network of trusted partners that help ensure those cars are as sturdy as they look.
Who exactly are these steel suppliers? Companies like U.S. Steel and ArcelorMittal usually lead the pack, providing Ford with high-quality materials to ensure strength and durability. These aren't small-time players — they're big names in the industry, renowned for their superior product.
Why does this matter? Because the quality of steel directly affects a car's safety, performance, and longevity. Ford can't afford to cut corners when it comes to choosing suppliers; they've got a reputation to maintain, after all. Plus, having a close relationship with suppliers means Ford can innovate and adapt to new technologies more swiftly.
- Major Steel Suppliers for Ford
- Importance of Steel Quality in Automobiles
- Ford's Strategic Locations for Sourcing
- The Supply Chain Complexity
Major Steel Suppliers for Ford
When it comes to supplying steel for Ford, the company prefers working with giants in the steel industry. Why? Because these suppliers provide the reliability and quality that's crucial for manufacturing sturdy vehicles. Ford doesn't compromise on the materials that go into their cars, trucks, and SUVs. Let's take a closer look at some of their major suppliers.
U.S. Steel
One of Ford's primary suppliers is U.S. Steel. Known for its history and expertise in steel production, U.S. Steel offers a range of products that meet the demanding standards of automotive manufacturing. They produce their steel using advanced technologies to ensure high strength and durability.
ArcelorMittal
Another big name supplying steel to Ford is ArcelorMittal. As the world's leading steel and mining company, ArcelorMittal has a global presence. They provide innovative solutions that help Ford achieve lightweighting — crucial for improving fuel efficiency in vehicles.
SSAB
SSAB, a Swedish company, is also in Ford's supplier lineup. SSAB specializes in high-strength steels that can be used to make cars lighter without compromising safety or performance. This is increasingly important as automakers work towards producing greener vehicles.
With these strategic partnerships, Ford ensures a steady supply of strong, high-quality steel that forms the backbone of their vehicles. It's all about getting that balance of strength, weight, and cost just right, and these suppliers play a big role in making it happen.
Interesting Fact: Regional Sourcing
A lot of Ford's steel is sourced from regions close to their manufacturing plants. This not only reduces transportation costs but also minimizes the environmental impact. An example is the Great Lakes area, rich in iron ore deposits and home to many American steelmakers.
Importance of Steel Quality in Automobiles
Why does steel quality matter so much in making cars? Well, it plays a huge role in several key aspects such as safety, durability, and performance. Every car owner wants a car that not only lasts long but also protects them in case of accidents. So, let’s dig a little deeper into why steel quality is a big deal for automakers like Ford.
Safety Comes First
The quality of steel is directly tied to vehicle safety. High-quality steel tends to absorb impact better in case of collisions. This means it minimizes the force that reaches passengers inside, which can mean the difference between life and death in severe crashes. And it’s not just about the ability to absorb shock. Good steel ensures the structural integrity of the vehicle, which is essential for maintaining shape and providing protection.
Durability and Longevity
It’s no secret that cars take a daily beating — from rough roads to harsh weather conditions. Top-notch steel resists rust and corrosion better, which leads to longer vehicle life. Ford pays close attention to the quality of steel they use because they know that high durability means fewer replacements and repairs for car owners. Today’s vehicles, especially SUVs and trucks, demand high-strength steel to handle the extra weight and stress, proving the importance of using quality materials.
Performance and Efficiency
Steel quality can also influence how a car handles and performs. High-strength but lightweight steel contributes to optimized fuel efficiency. With the world moving towards reducing carbon footprints, more efficient vehicles mean Ford continues to be environmentally responsible, helping drivers save on fuel costs too. A lighter car using just the right amount of quality steel can translate to better speed and handling. Who doesn't like a ride that drives smooth and burns less fuel?
The Ever-Important Ford Reputation
Finally, Ford has built a reputation over the years for creating reliable and robust vehicles. The company’s commitment to using high-grade steel supports this reputation, keeping it competitive in the car parts industry. After all, customers expect nothing less than what Fort Tough promises!
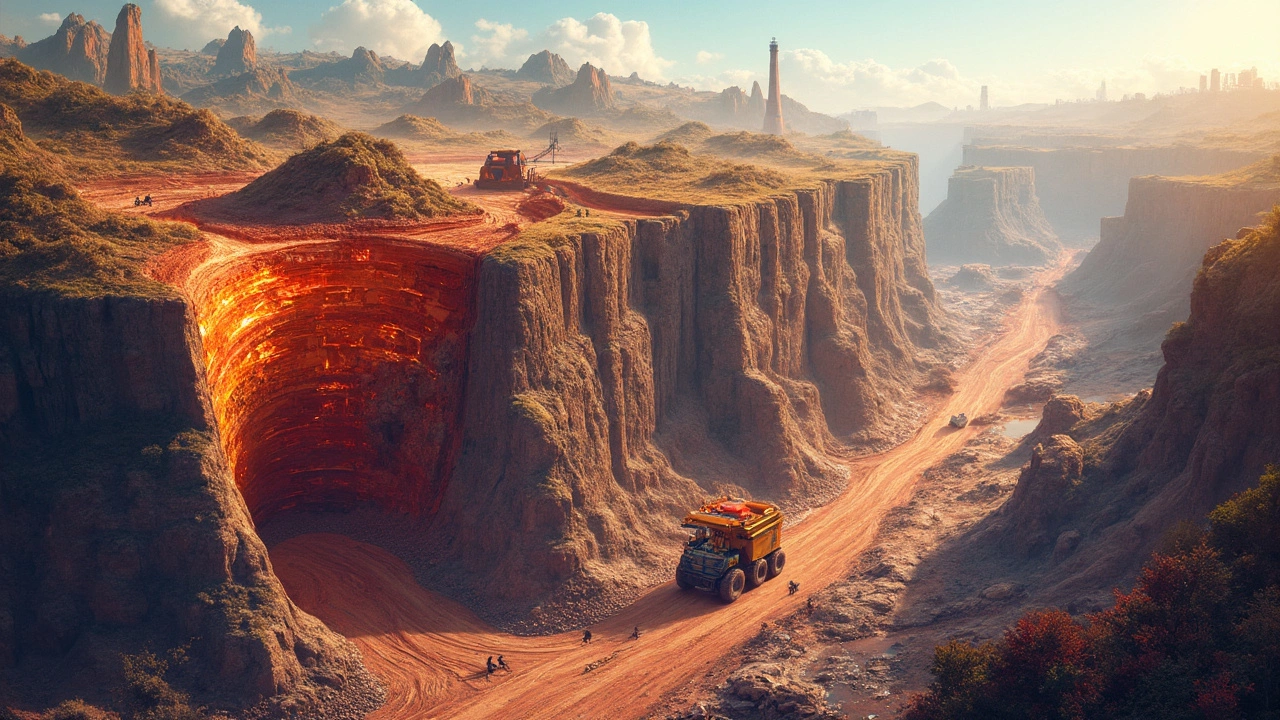
Ford's Strategic Locations for Sourcing
When it comes to sourcing steel, Ford is no slouch. They're extremely strategic about where they get their materials from, ensuring efficiency, quality, and cost-effectiveness throughout the supply chain. What’s interesting is that Ford's sourcing locations are not random; they’re purposefully chosen to leverage proximity to essential resources.
Proximity to Steel Suppliers
A major chunk of the steel used by Ford comes from the Great Lakes region. This isn't just because of the scenic views but because it's home to some of the largest steel producers in the US. Take, for example, the famous city of Pittsburgh. Nestled near the Great Lakes, it's a central hub for steel production and allows Ford to minimize transportation costs while maximizing direct access to suppliers like U.S. Steel.
International Partnerships
While many think of America when it comes to Ford, their steel sourcing is global. They work with international giants like ArcelorMittal, which has facilities all over the globe. This not only diversifies their sources but ensures that disruptions in one region won't halt production.
Efficiency and Logistics
Ford has plants close to key logistics hubs, like ports and major highways. This strategic placement means raw materials can move swiftly from suppliers to production lines. With facilities worldwide, Ford can adjust its logistics based on market demands and supply fluctuations, showing just how adaptable they are.
Location | Primary Supplier | Key Advantage |
---|---|---|
Detroit, USA | U.S. Steel | Proximity to production facilities |
Oshawa, Canada | ArcelorMittal Dofasco | Access to Canadian markets |
Valencia, Spain | ArcelorMittal | European market presence |
Ultimately, Ford’s strategy isn’t just about buying steel; it's about comprehensive planning in the supply chain. They marry strong supplier relationships with smart logistics to keep their edge in the automotive market.
The Supply Chain Complexity
The journey of steel from the ground to a shiny new Ford is anything but straightforward. The supply chain isn't just about placing an order and receiving a delivery. It's a tightly choreographed dance that involves multiple players, from miners to manufacturers, and a lot of logistical gymnastics.
The starting point often involves mining iron ore, which is the primary ingredient of steel. This ore is then processed into various types of steel, depending on the requirements. For automakers like Ford, who are rigorous about vehicle performance, suppliers need to refine steel to exacting specifications to ensure quality and consistency.
Coordination with Suppliers
Ford maintains relationships with multiple suppliers to mitigate risks like material shortages or price hikes. Firms such as U.S. Steel and ArcelorMittal, often located near the Great Lakes, have easier access to the raw materials, reducing transport costs which is vital for keeping expenses under control. Ford's strategic move ensures they’re never too dependent on a single source.
Global Logistics
Once the steel meets Ford's standards, it enters the global logistics web to reach various Ford plants across the world. Massive ships, long-haul trains, and fleets of trucks are engaged in transporting the material. This extensive network is crucial for keeping production lines humming since any disruption can lead to costly delays.
Leveraging Technology
Technology now plays a significant role in managing this complex process. Systems are in place for real-time tracking of shipments, forecast demand, and optimize routes for fuel efficiency. This tech-forward approach not only improves the supply chain's reliability but also its resilience against unforeseen disruptions, like natural disasters or geopolitical tensions.
Interestingly, Ford often prepares for such complexities with a dual-sourcing strategy, which means they source the same materials from different suppliers. This not only provides a safety net but also fosters a competitive environment among suppliers, encouraging them to offer better prices and improved quality.
Addressing Challenges
Despite all these arrangements, challenges do pop up. For instance, fluctuations in steel prices can spike due to market conditions, impacting overall manufacturing costs. Being among the largest automakers, Ford does have some leverage to negotiate pricing, but external factors always play a role.