Walk into any electronics store, and almost everything you see runs on semiconductors. But if you check the fine print, hardly any of those chips say "Made in India." That’s not an accident—it’s a big story about how chips are made, why they matter, and where India fits in this global race.
First, let’s get real about what a semiconductor is. We’re talking about those tiny chips inside phones, laptops, cars—basically anything smart. Making them isn’t like making your everyday gadgets. It takes billion-dollar factories, high-level engineering, and a supply chain that runs like a Swiss watch. India has the talent, no doubt, but building up the factories and the whole ecosystem? That’s where the challenge starts.
Years ago, you’d hear the phrase “Make in India” everywhere. Chips, though, stayed on the wish list. Even today, most of the chips powering gadgets in India are imported from places like Taiwan, South Korea, or the US. So, is India making semiconductors at all? There’s more happening than you might think, but it’s not on the industrial scale you’d see in Taiwan or China—at least, not yet.
- How Chips Are Actually Made
- Where India Stands Today
- Why Local Chip Production Matters
- Major Projects and Policy Push
- What's Next for India's Chip Dream
How Chips Are Actually Made
Ever wondered why semiconductors are such a big deal? Making a single chip is way more complicated than building a smartphone or car. It starts with a chunk of pure silicon called a wafer. Think of it like a sheet cake, but a lot more precise. Each wafer gets sliced super thin, polished, and cleaned until it’s spotless.
The next part is where the magic happens. Factories use machines called photolithography tools (imagine massive projectors) to print tiny patterns on the wafer. These patterns are what turn a plain slab of silicon into a smart chip. They layer different materials, etch them with chemicals, and sometimes even zap them with electricity. A chip can have billions of tiny switches inside (called transistors), all working together.
- Designing: Engineers create the chip’s blueprint, usually with computer programs, before a single wafer is touched.
- Fabrication: Factories (fabs) use extreme accuracy to cut, layer, and process the wafer. One speck of dust can ruin things.
- Testing & Packaging: Each chip gets tested—bad ones get tossed out. Good ones are sealed and shipped worldwide.
Most fabs need to stay cleaner than a hospital surgery room. Workers wear full body suits—anything less and static or dust could ruin million-dollar batches. That’s why setting up chip manufacturing in places like India isn’t just about money. You need the tech, the machines, raw materials, and people who know the whole drill.
Major Chip-Making Countries | Share of Global Production (%) |
---|---|
Taiwan | ~60 |
South Korea | ~17 |
USA | ~12 |
China | ~6 |
India | <1 |
So, when people ask if semiconductors are made in India, it helps to know just how complex and specialized this process is. India’s got some places doing design work and building simpler chips, but the high-end, high-volume stuff? That’s where the country’s still playing catch-up with global giants.
Where India Stands Today
If you look around, India isn’t mass-producing high-end semiconductors just yet. Right now, almost all advanced computer chips in use across the country are imported from major players like Taiwan’s TSMC, South Korea’s Samsung, and the United States’ Intel and GlobalFoundries. There’s no Indian equivalent churning out those powerful, tiny brains for your smartphone or laptop—at least for now.
But don’t get the wrong idea—India’s not totally out of the game. The country has a strong presence in what’s called semiconductor design. Plenty of U.S. chip giants have major design centers in Bengaluru and Hyderabad. Engineers here design and test complicated circuits for companies like Qualcomm, Intel, and AMD. So, while the chips aren’t physically “made in India,” a lot of the brains behind them are Indian.
When it comes to chip manufacturing—what’s officially called fabrication or 'fabs'—the picture is much smaller. India does have the ISRO-linked Semi-Conductor Laboratory (SCL) in Mohali, but it mostly handles foundry work for defense and research, at basic technology nodes compared to today’s global standards. For those keeping track, that means old-school 180nm tech, while the world’s moving to 3nm chips. In plain English: India’s fabs are making much simpler chips than the ones powering the latest iPhone.
Here’s a quick comparison of fab capabilities:
Country | Most Advanced Node (nm) | Main Use |
---|---|---|
Taiwan (TSMC) | 3 | Smartphones, servers, AI chips |
South Korea (Samsung) | 3 | Memory, processors |
India (SCL) | 180 | Defense, public sector |
There have been some recent attempts to change this. Big industry names like Vedanta and Tata are eyeing the electronics manufacturing space, and the government has announced plans to boost the chip industry with funding support for new factories. Applications for new fabs in Gujarat and Karnataka are being reviewed, but as of today, nothing mass-market has come online yet.
So for now, India’s semiconductor manufacturing is mostly small-scale and research-focused. Indian engineers and designers are a big part of the world’s chip creation story, but if you’re holding something with a chip made on Indian soil, it’s probably from a special project—not a regular smartphone, laptop, or car.
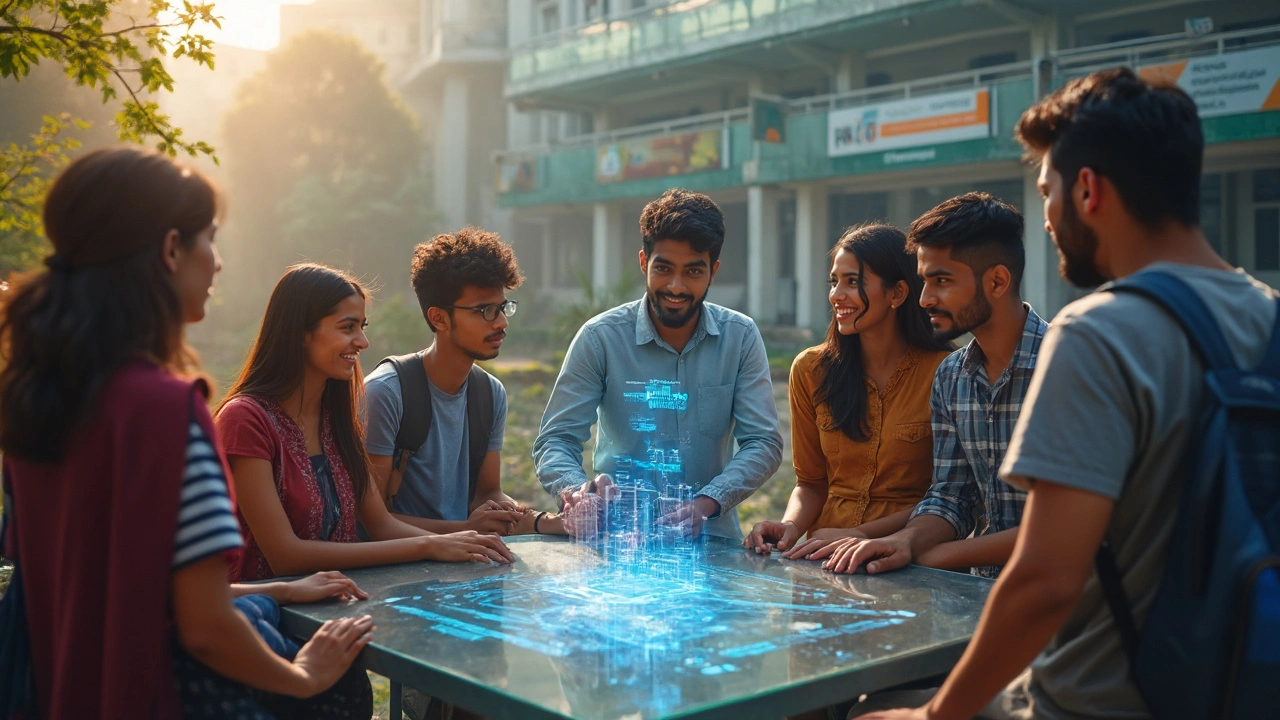
Why Local Chip Production Matters
If you’ve ever wondered why there’s a buzz about semiconductors and making them in India, it’s not just about bragging rights. It hits home for national security, job creation, and the price tags on everything from smartphones to electric vehicles.
Let’s break it down. When a country depends on imported chips, it puts a lot of faith in global supply chains. The world learned the hard way in 2021, when the chip shortage hit—suddenly, car factories and phone brands in India had to slow down because chips from Taiwan and the US couldn’t arrive on time.
- Security and Self-Reliance: Local chip making means not being left hanging because of trade fights or sudden factory shutdowns in other countries.
- Jobs and Training: A single semiconductor fab can create thousands of high-skilled jobs. And we’re not just talking engineers; we’re talking about operators, quality control, logistics, the whole nine yards.
- Making "Make in India" Real: Right now, a lot of things are just ‘assembled’ in India with imported guts inside. Local chips mean value stays in the country, not just the final screw.
Here’s how much impact electronics manufacturing and semiconductors have on the Indian economy:
Factor | Value/Impact |
---|---|
Annual electronics imports (2024) | $60 billion+ |
Estimated chip market in India (2026) | $80 billion |
Jobs from a single fab unit | 10,000+ direct and indirect |
Building a local chip industry isn’t just about saving money, either. Even a 10% cost jump in chips can swing prices of gadgets and cars by quite a bit. When chips are made closer to home, it means faster development, more stable prices, and less waiting for new tech to launch in India.
So, it’s not hype. When you hear talk about local chip factories, it’s India trying to stop losing billions on imports, create real jobs, and make sure it doesn’t get caught off guard again when the world runs short of chips.
Major Projects and Policy Push
If you’ve been keeping an eye on the news, you’ll know India hasn’t just sat around waiting for chips to fall from the sky. The government is throwing real money and policies at the semiconductors game. Their biggest move? The Production Linked Incentive (PLI) scheme for electronics, rolled out to attract companies and investors to build factories in India. In 2021 alone, they put down $10 billion just to encourage chip making. That’s not pocket change.
Here’s what stands out for anyone following electronics manufacturing in India:
- Micron Technology: In 2023, the American chip giant got the green light for a $2.75 billion chip assembly and testing plant in Gujarat. It’s not full fabrication (where they make the silicon wafers), but it puts India on the map for high-value chip assembly.
- Vedanta-Foxconn Project: This was hyped up as India’s big leap. They announced a $19.5 billion project in Gujarat to build a full-fledged semiconductor manufacturing plant. Although Foxconn pulled out mid-2023, Vedanta is negotiating with new partners to keep the dream alive. The idea is clear: India wants its own fabs, and they want them soon.
- ISMC and Tower Semiconductor: Another proposed fab in Karnataka hopes to focus on analog chips—these are critical for cars and medical gear. Progress is slow, but the intent is serious.
What’s the government actually doing to make it easier? For one thing, they’ve fast-tracked licenses and made it simpler for foreign direct investment (FDI). They’ve also launched the DLI (Design-Linked Incentive) for homegrown chip designers, so Indian brains aren’t left out.
If you like numbers, check this out:
Year | Investment Announced ($B) | Active Projects |
---|---|---|
2021 | 10 | PLI Scheme, DLI Scheme |
2023 | 22.25* | Micron, Vedanta, ISMC |
*Includes planned and announced investments.
Most chips are still imported, but anyone starting a business or looking to work in this sector should track these semiconductors projects. If even half of them go live, the story of "Are semiconductors made in India?" could be totally different by the end of the decade.
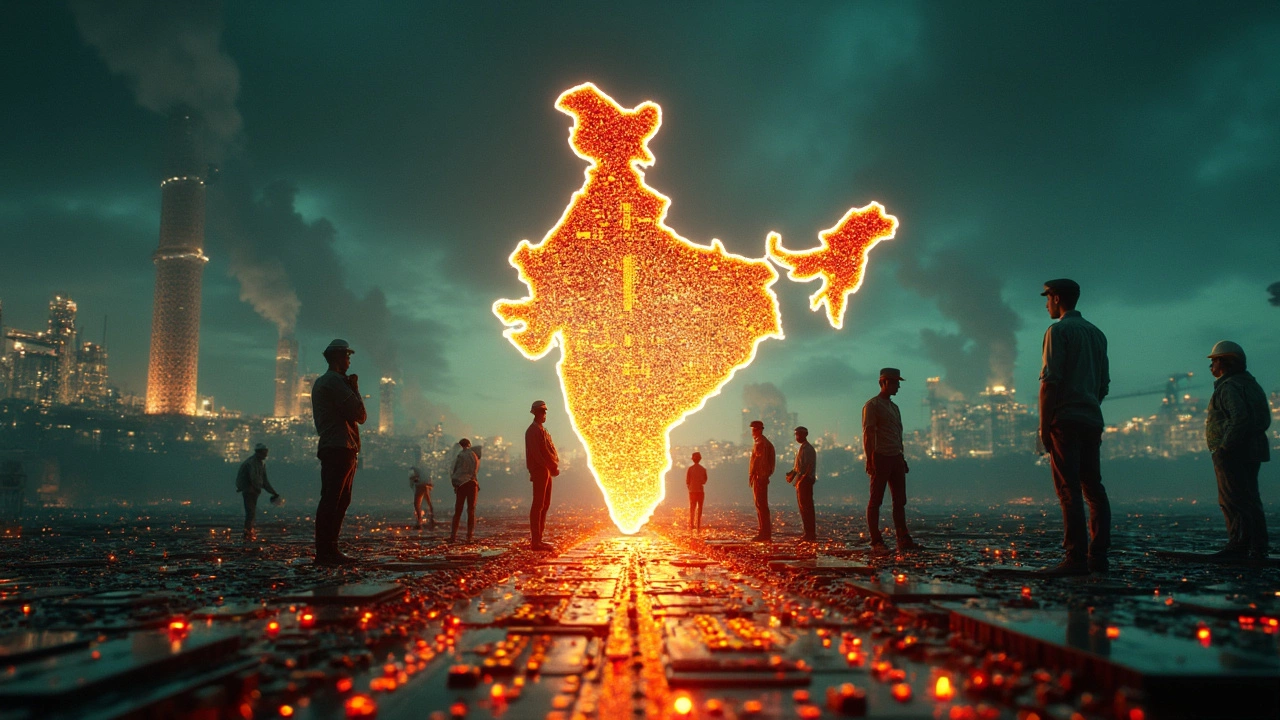
What's Next for India's Chip Dream
India’s ambition to become a true semiconductors powerhouse is finally picking up real steam. In 2023 and 2024, the government announced incentives worth over $10 billion to lure big global players in electronics manufacturing and chip fabrication. Heavyweights like Micron and Tata Group confirmed investments in Gujarat and Assam—real factories, not just paperwork. The Tata-Micron project, for example, is set to build a full-scale assembly, testing, marking, and packaging (ATMP) unit in Gujarat, with plans for mass hiring and tech transfers.
You might wonder, "When will we see an actual 'Made in India' chip in a mobile phone?" That’s not around the corner. Building a chip industry from scratch is a marathon, not a sprint. Experts say that the first commercial chips born, built, and packaged in India will likely roll out by late 2025 or 2026—if everything sticks to the current schedule.
Still, there’s visible progress on campus too. Indian engineers are designing chips for global companies right now, even if the final product is still made offshore. IITs and private colleges have launched courses on VLSI (that’s Very Large Scale Integration, the stuff chips are made of), and student hackathons on chip design are popping up like crazy. If you’re dreaming about a job in core semiconductors, now’s the time to skill up—companies are hiring for roles that didn’t exist in India just a few years ago.
Here’s what to keep an eye on if you’re following this space:
- Updates from Tata, Micron, and ISMC as they set up India’s first chip fabs and ATMP units.
- Government policies—watch for tweaks to the incentive schemes or tax breaks that might attract other big names.
- Partnerships with countries like Japan, the US, and the EU, which could speed up tech transfer and workforce training.
- Continued growth in chip design and embedded software, which might become India’s calling card before manufacturing catches up.
Year | Major Event |
---|---|
2023 | Micron announces $2.75 billion ATMP facility with government support |
2024 | Tata Group breaks ground on a chip fabrication unit in Dholera, Gujarat |
2025 | Expected start of commercial chip packaging in India |
The road ahead for India isn’t a straight line, but the country is finally in the race. If the next few years go right, "Made in India semiconductors" might soon be more than just a slogan—they’ll be part of your phone, your car, maybe your washing machine too.