Everyone's heard of the industrial revolution, right? But who actually kicked it all off and became known as the 'father of manufacturing'? It's a name not many people immediately think of: Eli Whitney. His name is like gold in the annals of manufacturing because he pretty much transformed the way products were made with his creation of interchangeable parts. This was way back in the early 1800s. Before Whitney, if one part of a machine broke, you'd have to custom-make a new one—imagine the headache. But interchangeable parts turned this problem on its head, making it faster and less expensive to repair machinery.
Whitney's idea wasn't just a minor tweak; it was a game changer. It laid the groundwork for what we now call mass production, impacting industries worldwide. Knowing this can shed light on how government schemes and policies today work to support and boost manufacturing sectors. They want to tap into this rich history to fuel present and future industrial success.
- The Origins of Manufacturing
- Key Innovators in Manufacturing
- Government Schemes Supporting Manufacturing
- Impact of Industrial Revolution
- Modern Manufacturing Practices
The Origins of Manufacturing
Let's kick off with the initial sparks that ignited the manufacturing world. The real roots of what we now consider modern manufacturing actually trace back to the 18th century, during the early days of the industrial revolution. Before this technological leap, manufacturing was mainly a cottage industry, with artisans and craftsmen painstakingly creating goods by hand. This transformed with the invention of steam power, which was crucial in transitioning from manual labor to machine-driven production.
One key figure often credited as the father of manufacturing is Richard Arkwright. He's known for inventing the water frame in 1769, a cornerstone in the textile industry. This machine could spin multiple cotton threads simultaneously and marked the beginning of factory-based production.
The Shift from Craft to Factory
This period saw the rise of major manufacturing hubs, especially in places like England. Factories sprouted with rows of machines, reducing the time and effort needed to produce goods. It was a time of significant social change too, as people moved from rural areas to cities seeking work.
Kraft and Wendell: Innovators
Another figure, Josiah Wedgwood, brought systematic mass production to pottery. He introduced division of labor in his factories, laying the groundwork for more complex industrial operations.
These developments paved the way for government schemes to enhance industrial growth. Rulers soon realized that a strong manufacturing sector meant a robust economy. Thus began a slew of policies designed to support and expand manufacturing capacities.
Year | Key Innovation | Impact |
---|---|---|
1769 | Water Frame | Enabled factory-based textile production |
1770 | Division of Labor | Increased efficiency in pottery manufacturing |
By underpinning the essence of industrial growth, these advancements didn't just shape the past; they continue to influence the way modern manufacturing practices evolve today.
Key Innovators in Manufacturing
When you're talking about the rise of manufacturing, some folks really led the charge. Besides Eli Whitney, there were other big players whose ideas and inventions shaped the industry. One of them was Henry Ford, the man who famously put America on wheels with the Model T. Ford didn’t just build cars; he revolutionized the production process with his introduction of the moving assembly line in 1913. This method cut the time to build a car from more than 12 hours to just about 90 minutes. Talk about a game changer!
James Hargreaves and the Spinning Jenny
Another early innovator was James Hargreaves, an Englishman who came up with the Spinning Jenny in 1764. This invention dramatically increased the amount of thread produced by a single worker, playing a critical part in the textile industry’s boom during the British industrial revolution. Manufacturing history wouldn’t be the same without these contributions.
Frederick Winslow Taylor and Scientific Management
Then there's Frederick Winslow Taylor, often dubbed the father of scientific management. In the early 20th century, Taylor studied how work could be done more efficiently, laying the groundwork for modern process optimization in manufacturing. His time studies and work management became essential practices in factories around the globe.
The Impact of Innovators
A neat little fact: by 1920, Ford's manufacturing breakthroughs made it possible for ordinary folks to buy cars at just five months’ salary, a big deal back then. Thanks to these masters of innovation, the foundation was set for future manufacturing schemes that many governments globally now aim to nurture and expand.
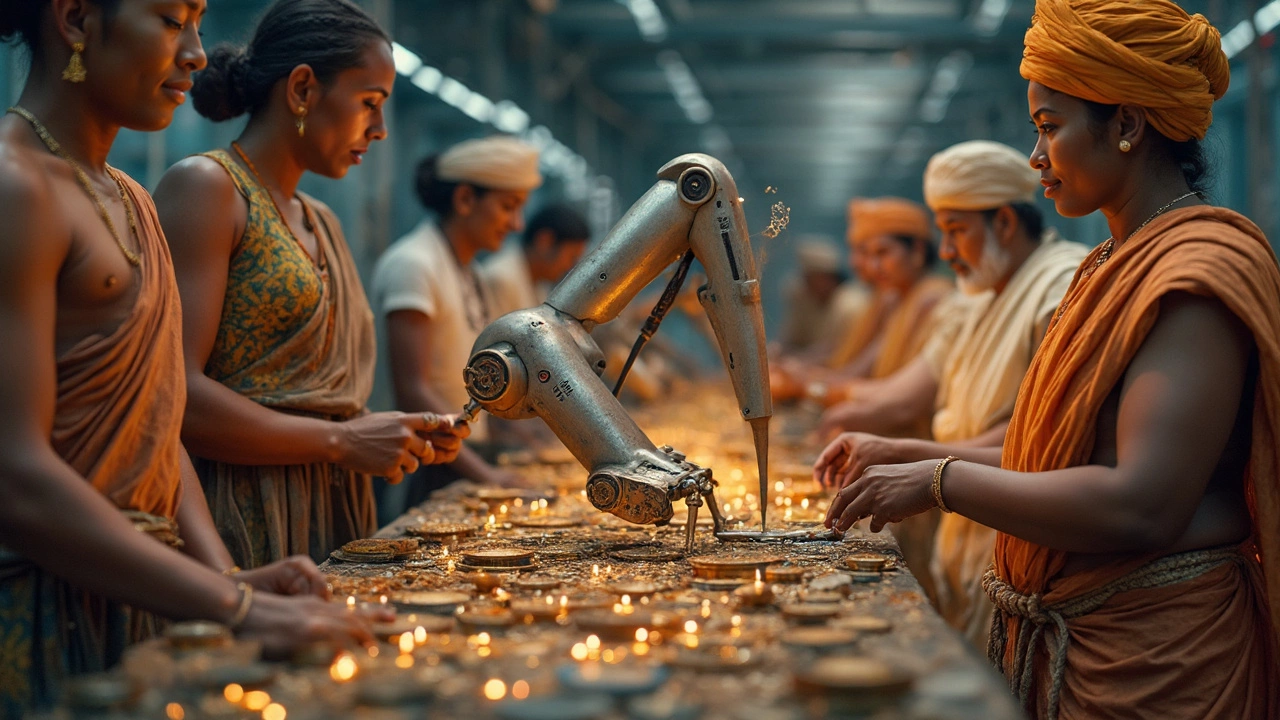
Government Schemes Supporting Manufacturing
Government schemes have been a major player in pushing the manufacturing sector forward. With everything from tax incentives to funding grants, these programs aim to make manufacturing more appealing and viable. The big idea is to create jobs, boost innovation, and keep our factories buzzing. Let’s dive into some examples that have sparked these changes.
Tax Incentives and Breaks
One of the most noticeable ways governments support manufacturing is through tax breaks. In countries like the United States, manufacturing businesses benefit from deductions on equipment purchases. This allows companies to upgrade their tech without breaking the bank. Similar schemes have been seen in the UK, where the Manufacturing Advisory Service provided tax incentives until it was replaced by newer initiatives in recent years.
Direct Funding and Grants
If there’s one thing manufacturers love, it’s direct funding. Governments set aside significant cash to fund programs that revamp manufacturing sectors. For instance, the UK’s Smart Manufacturing Grant aims to digitize and improve factories. The scheme offers substantial financial backing for companies looking to adopt cutting-edge tech.
Training Programs
It’s not just about machines and money; skilled workers are vital too. Many governments pour resources into vocational training schemes so the workforce is prepared for modern manufacturing jobs. Countries such as Germany are renowned for their apprenticeship programs, blending on-the-job training with quality education.
Country | Scheme | Focus |
---|---|---|
USA | Advanced Manufacturing Partnership | Innovation and R&D |
UK | High Value Manufacturing Catapult | Technology Adoption |
Germany | Industry 4.0 | Digitization |
As you can see, boosting manufacturing is often a national effort. Policies and schemes are continuously evolving to tackle new problems and take advantage of new opportunities. By understanding these schemes, manufacturers can pinpoint where to get some extra help and how to strategize their next move efficiently.
Impact of Industrial Revolution
No doubt about it, the industrial revolution was a massive game-changer. It took everything people knew about manufacturing and pretty much flipped it on its head. We're talking about a period from the late 18th century to the mid-19th century when the way products were made shifted dramatically.
Before this, most production happened in homes or small workshops. Then bam! Big factories sprouted everywhere, powered by smokin' steam engines and stocked with machines that could churn out goods way faster than a person could. Suddenly, stuff that once took days to make was done in hours. Faster work meant more money and cheaper products, which was pretty attractive to consumers.
Key Changes Brought by the Revolution
- Mechanization: Machines doing jobs that were once manual was a big part of the revolution.
- Urbanization: People flooded into cities looking for factory work, which led to a big shift from rural living.
- Growth in Industries: Textiles, iron, and coal industries boomed like nobody's business.
But what about costs? The rise of factories meant economies of scale, lowering costs per unit and making goods more affordable. Still, it wasn't all rosy. The focus on mass production meant working conditions could be tough, with long hours and little regard for worker well-being.
Relevance to Modern Manufacturing
Fast forward to now. The industrial revolution set the stage for today’s manufacturing. Modern factories are high-tech, using automation and data to keep the wheels turning smoothly. Plus, many government schemes are inspired by its success. These modern policies aim to boost industrial growth by encouraging innovation and supporting businesses looking to compete globally.
So, when you hear about a 'government initiative' supporting manufacturing, it often involves strategies that learned from both the triumphs and trials of the industrial revolution. It’s like running a relay race where today's manufacturers are picking up the baton from those early industry pioneers.
Year | Key Development |
---|---|
1760 | First textile mills using water power |
1770 | Steam engine revolutionizes transport |
1800 | Eli Whitney's interchangeable parts gain traction |
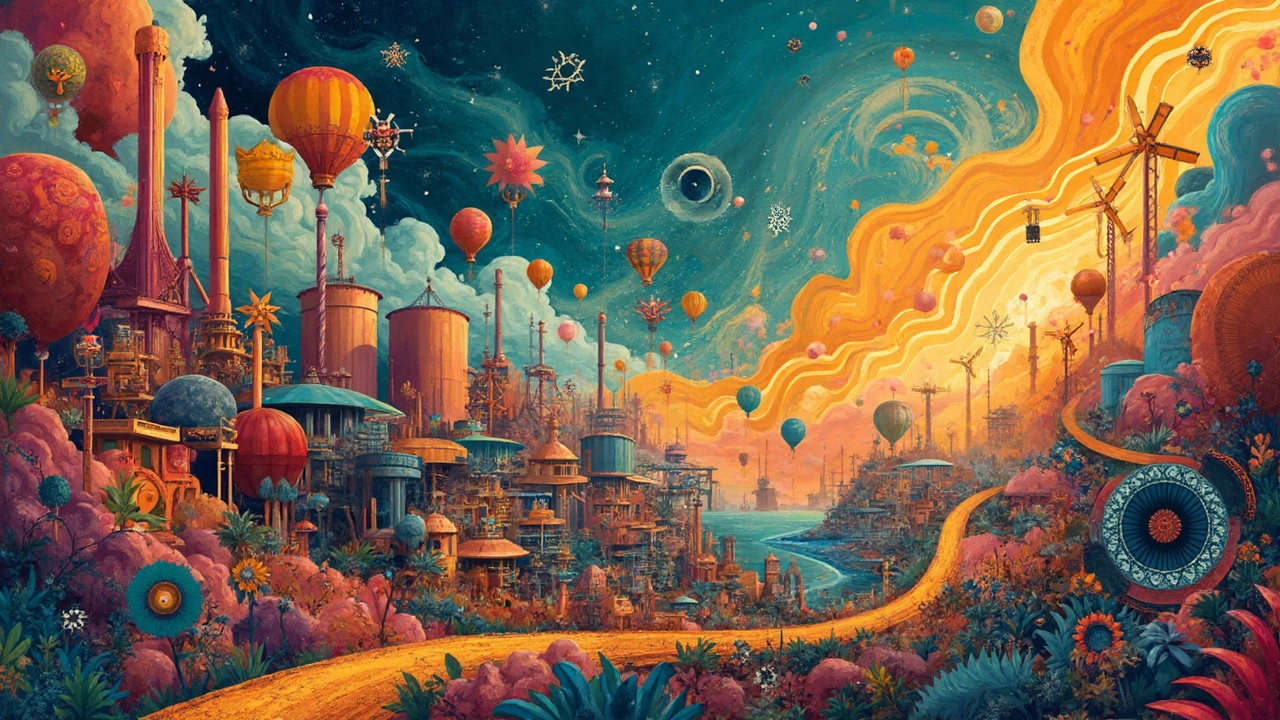
Modern Manufacturing Practices
Modern manufacturing is a whole new ballgame, thanks to tech innovations like AI and IoT (Internet of Things). These technologies are transforming manufacturing floors into smart, interconnected hubs where machines communicate with each other, enhance efficiency, and reduce human errors. It’s a far cry from Eli Whitney’s time! These changes align with government schemes aiming to bolster manufacturing sectors.
The Rise of Automation
Automation is huge today. Robots and automated systems take on repetitive tasks, freeing up human workers for more complex duties. This doesn’t mean machines are taking over our jobs. Rather, they’re reshaping them. We now focus more on roles that require creativity and critical thinking.
Sustainability in Focus
With climate change concerns mounting, eco-friendly manufacturing is more crucial than ever. Companies are now integrating sustainable practices to minimize waste and maximize resource efficiency. Some factories are even set up to be entirely waste-free—whether through recycling processes or using renewable energy sources.
Moreover, government schemes are backing these green initiatives. Grants and tax benefits are often available for businesses that reduce carbon footprints or invest in cleaner technologies.
3D Printing: The New Kid on the Block
3D printing might still sound a bit sci-fi, but it’s here and revolutionizing how we think about production. It allows for rapid prototyping and reduces the time from design to production significantly. No wonder so many industries are jumping on board!
Data-Driven Decisions
Another key trend is the use of big data and analytics. Data collected from various points in the manufacturing process helps businesses understand trends, address inefficiencies, and improve quality control—making for a smarter production cycle.
Key Tech | Impact on Manufacturing |
---|---|
AI | Enhances predictive maintenance |
IoT | Improves equipment efficiency |
3D Printing | Reduces production time |
Embracing these modern manufacturing practices isn't just about keeping up with trends; it's about setting up for long-term success. Staying ahead in the manufacturing game today means blending heritage and innovation into a seamless operation—something even the father of manufacturing would have admired.