Ever wondered what makes a plastic 'high quality' when it comes to manufacturing? It's not just about durability or flexibility. In the industry, quality encompasses several factors including strength, temperature resistance, and even how eco-friendly the material is. For anyone diving into the world of plastic manufacturing, knowing these can be a game changer.
Take polycarbonate, for example. It's renowned for its clarity and impact resistance—think of your tough safety glasses or those durable water bottles. These qualities make it a top contender in many high-performance applications. But polycarbonate is just one piece of the puzzle.
Then there's polyethylene terephthalate (PET)—popular in the food and beverage industry thanks to its excellent barrier properties. Yet, quality doesn't stop at the physical attributes. It includes how easily the material can be recycled, aligning with the growing sustainable practices in industries worldwide.
Choosing the right plastic isn't one-size-fits-all. What works for automotive parts might not suit medical equipment. Each application has unique requirements, and a high-quality plastic will meet those without compromising performance.
- Understanding Plastic Quality
- Popular Types of High-Quality Plastics
- Factors Determining Plastic Quality
- Choosing the Right Plastic for Your Needs
- Sustainability and Innovation in Plastics
- Future Trends in Plastic Manufacturing
Understanding Plastic Quality
When we talk about quality plastic, we're looking at a combination of properties that make a material fit for its intended use. It's not just one single thing—it's a mix of characteristics that includes strength, flexibility, and resistance to things like temperature and chemicals.
Key Properties of High-Quality Plastics
To get a handle on what quality means in the plastic world, consider these core properties:
- Durability: A good quality plastic should withstand physical stress without cracking or warping. Think about the robust nature of high-density polyethylene (HDPE) used in piping and construction materials.
- Thermal Resistance: Some applications require plastics that can endure high temperatures. For instance, polyetheretherketone (PEEK) is often used in aerospace and automotive industries thanks to its ability to resist extreme temperatures.
- Chemical Resistance: Plastics like polypropylene (PP) are often chosen for their resistance to acids and chemicals, making them ideal for lab equipment.
- Clarity and Aesthetics: For products like packaging, the clarity of a plastic like PET can make all the difference in visual appeal and functionality.
Testing and Measurement
Quality isn’t subjective—it’s measured. Plastics undergo various tests to assess these properties. Tensile strength tests, for example, measure how a plastic performs under tension. Then there's impact strength testing, which checks how well it absorbs shocks.
These tests are crucial for ensuring that a plastic meets the necessary standards for whatever purpose it's being used. In fact, failing to meet quality standards can lead to product failure and safety issues, which nobody wants.
The Role of Sustainability in Quality
In our eco-conscious world, sustainability is becoming a big part of what makes plastic 'quality.' Manufacturers are increasingly focusing on creating biodegradable plastics or those that can be easily recycled to reduce environmental impact. Just think about the recent push towards using more recycled PET (rPET) in various packaging solutions.
Understanding what makes high-grade plastic truly ‘quality’ helps manufacturers choose the right material for the job, ensuring safety, performance, and even sustainability. It's a complex mix, but getting it right is crucial for success in today's market.
Popular Types of High-Quality Plastics
When you're picking a quality plastic for manufacturing, the variety can be kind of overwhelming. But certain types have earned their spot in the limelight due to solid performance across different industries.
Polycarbonate (PC)
Widely used for its impressive strength and transparency, polycarbonate is a favorite in producing things like CDs, water bottles, and eyewear lenses. Its impact resistance is notable, making it ideal for use where durability is key. Plus, it has a high heat resistance, so it's used in applications where temperature can get tricky.
Polyethylene Terephthalate (PET)
PET is the superstar of the packaging world. It's the go-to for beverage bottles and food containers because of its excellent barrier properties. Not to forget, it's lightweight and fully recyclable, which ticks a big sustainability box in today’s eco-conscious landscape.
Polyvinyl Chloride (PVC)
PVC is a bit of a workhorse in construction. It's used for pipes, window frames, and flooring. Its ability to withstand weather conditions without degrading quickly is a significant plus. Although it's tough, it's also flexible enough to be shaped or extruded into various forms.
Acrylonitrile Butadiene Styrene (ABS)
This material is particularly known for its toughness and impact resistance. Ever wondered why LEGO bricks are so enduring? Yup, they're made of ABS. Thanks to its glossy surface and rigidity, ABS is also found in automotive parts and electronic housings.
High-Density Polyethylene (HDPE)
The secret to HDPE's popularity is its high strength-to-density ratio. It's commonly found in products like milk jugs, shampoo bottles, and grocery bags. Beyond consumer goods, it's crucial for industrial purposes such as piping and plastic lumber.
Knowing what makes these plastics stand out helps manufacturers choose the right material for their specific applications, ensuring high performance and longevity. Whether it's a need for strength, flexibility, or sustainability, there's a quality plastic fit for every purpose.
Factors Determining Plastic Quality
When it comes to identifying the highest quality plastic for manufacturing, several key factors come into play. Understanding these can make all the difference in choosing the right material for the job.
Strength and Durability
The first thing that hits the top of the list is how strong the plastic is. Does it crack under pressure? High-grade options like polycarbonate boast impressive impact resistance, ideal for applications where toughness is a must.
Temperature Resistance
Not all plastics can take the heat. Some will warp or melt when things get too hot. Plastics like polypropylene, however, handle higher temperatures without losing any of their integrity. Think of it like choosing the right gear for a hot kitchen versus a cold mountain.
Chemical Resistance
This is a biggie if your plastic will come into contact with chemicals. Certain plastics like polyethylene stand strong where others might degrade or discolor. It’s a crucial factor in industries like medicine or food packaging where safety is key.
Eco-Friendliness
Going green is not just trendy; it’s becoming essential. With increasing focus on sustainability, the ease of recycling is a major player in determining a plastic's quality. Look out for those that can go through multiple life cycles, reducing waste and environmental impact.
Cost-Effectiveness
What's the magic formula? Balance. While you might aim for the highest quality, the price tag is just as important. You need a material that hits the right quality notes without blowing the budget. Often, finding the sweet spot involves some trade-offs.
Factor | High-Quality Example |
---|---|
Strength | Polycarbonate |
Temperature Resistance | Polypropylene |
Chemical Resistance | Polyethylene |
Eco-Friendliness | PET (Polyethylene Terephthalate) |
In the end, the choice of plastic depends on what matters most for your application. Each factor weighs differently depending on specific needs, but getting these priorities right ensures you're on the path to selecting the best quality material.
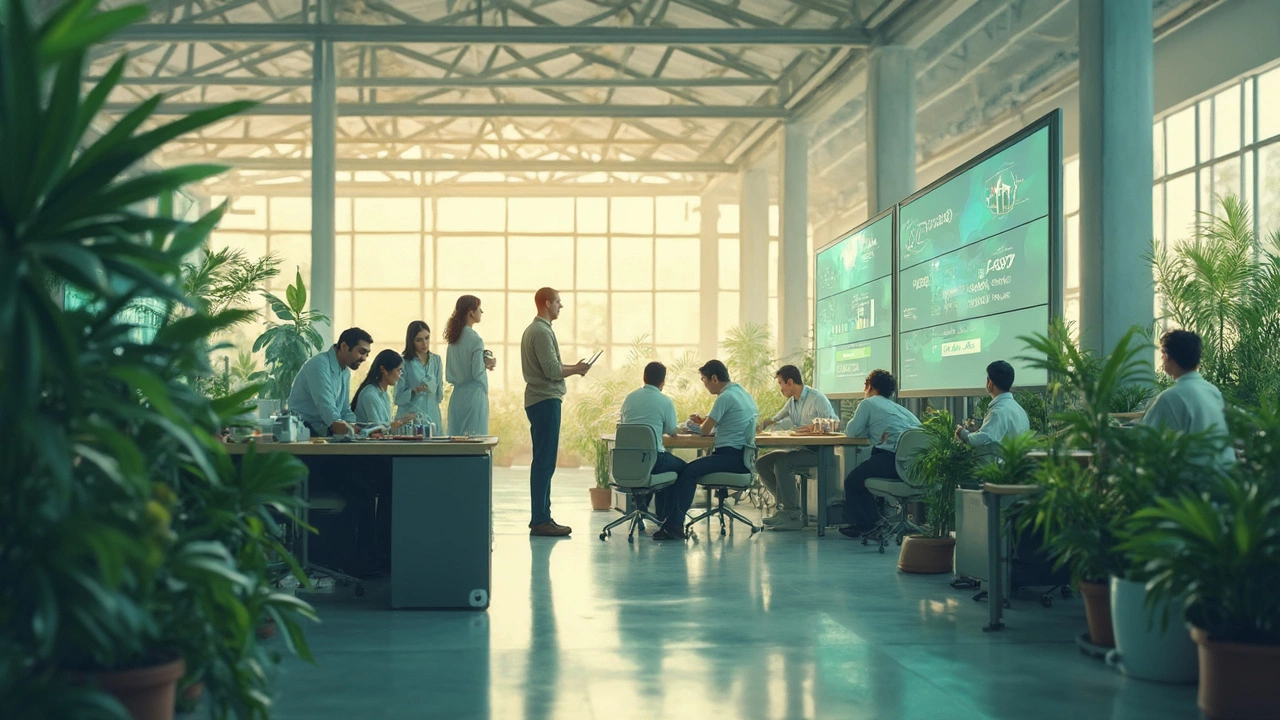
Choosing the Right Plastic for Your Needs
Selecting the ideal quality plastic is all about matching the material's properties with your specific project needs. It's not just about finding the strongest or most flexible option, but more about finding the material that ticks all the boxes for your particular application.
Functionality and Environment
Consider what role the plastic will play. For instance, is it required to endure high temperatures or provide a protective barrier? For electronics, ABS plastic is a go-to because of its electrical insulating properties. Depending on whether you're crafting outdoor furniture or medical supplies, your choice of material will differ dramatically.
Regulatory Compliance
Some industries have specific compliance standards for materials, especially those involving food or pharmaceuticals. Using FDA-approved plastics like certain grades of PET can be a necessity. Always double-check the regulations to avoid costly errors.
Sustainability and Recycling
With increasing environmental concerns, opting for recyclable plastics can be a wise choice. Bio-based plastics are emerging as eco-friendlier options. Investing in sustainable materials not only benefits the planet but can also align your brand with green practices.
Cost-Effectiveness
Budget plays a big role in decision-making. Different types of plastic come with different price tags. A thermoset plastic might be pricier than a thermoplastic but could offer savings in longevity and performance.
Material Properties: A Quick Check
Type of Plastic | Key Properties | Common Uses |
---|---|---|
Polycarbonate | High impact resistance, clear | Safety goggles, electronics cases |
ABS | Strong, good heat resistance | Automotive parts, toys |
PET | Transparent, recyclable | Bottles, food containers |
Expert Consultation
Sometimes, speaking with a material scientist or a trusted supplier can provide insights that you might not have considered. They can help navigate through the myriad of choices, ensuring you get the right fit for your manufacturing needs. Don’t underestimate the value of expert advice.
Sustainability and Innovation in Plastics
Let's face it, the topic of plastics and the environment can be a bit heavy, but there's a bright side. Companies everywhere are investing big in making plastics more sustainable. This isn't just about using recycled materials; it's about creating new materials that break down better and are less of an environmental headache.
Innovative Materials
Ever heard of bioplastics? They're made from things like corn starch or sugarcane instead of oil. They're gaining traction because they’ve got a lower carbon footprint than traditional plastics. These bioplastics, along with innovations like self-healing plastics, are paving the way for more eco-friendly manufacturing.Recycling Revolution
Recycling tech is getting some cool upgrades too. There's chemical recycling, which breaks plastics down to their core components, allowing them to be rebuilt almost like new. This means fewer new resources are needed, leading to even higher quality plastic that's just as good as, if not better than, virgin material.The Business Edge
Now, why should businesses care? Well, sustainability often translates to cost savings in the long run. For instance, lighter and more durable materials improve shipping efficiency. Plus, there’s increasing pressure from consumers and regulators for greener options, and companies that adapt might soon have a competitive edge.High-grade plastic choices today are about balancing performance needs with sustainability goals. Whether it's using cutting-edge processes or opting for high-quality recyclable materials, the industry's shifting towards responsible production methods.
What's clear is that sustainability isn't just a trend; it's rapidly becoming standard in the world of plastic manufacturing. With the right innovations, high-grade plastics are evolving into solutions that are better for the planet and the bottom line.
Future Trends in Plastic Manufacturing
The world of plastic manufacturing is evolving faster than ever, thanks to technological advancements and a growing focus on sustainability. So, what's coming down the pipeline in this industry? Let’s take a closer look.
Sustainability as a Core Strategy
Everyone's starting to care more about where their products come from and where they end up. Manufacturers are increasingly adopting sustainable practices for producing quality plastic. This includes using renewable materials and improving recycling methods to create closed-loop production systems. Not only does this reduce waste, but it also helps companies meet stricter environmental regulations.
Bioplastics and Innovations
Bioplastics are kind of a big deal right now. Unlike traditional plastics, they’re made from renewable bio-based resources like cornstarch. Though still pricier than their fossil fuel counterparts, bioplastics are gaining ground as more businesses realize their long-term benefits for branding and environmental footprint.
Advanced Technologies and Automation
With Industry 4.0 on the rise, automation and smart technology are making an impact on plastic manufacturing. Automated systems streamline operations and reduce human error, which cuts costs and improves product quality. Plus, there's a lot of buzz around AI and machine learning, which help optimize production processes by predicting maintenance needs and reducing downtime.
Breakthroughs in Plastic Recycling
Recycling's been a hot topic for a while, but we're seeing some real breakthroughs now. Chemical recycling is becoming more viable, allowing previously non-recyclable plastics to be repurposed. This method breaks down plastics to their basic monomers, providing a chance to create new high-grade plastic with lesser impurities.
Trend | Impact on Manufacturing |
---|---|
Sustainability | Environmentally friendly practices and compliance with regulations |
Bioplastics | Promotes eco-friendly production processes |
Automation | Increases efficiency and reduces operational costs |
Recycling Innovations | Enables the reuse of plastics with improved technology |
These trends are not just helping meet consumer demands but also setting new standards in the industry. Whether it’s improving the quality of life or protecting the planet, the future of plastics seems pretty exciting!