Running a manufacturing company isn't just about making products; it's a balancing act that involves leadership, strategy, and often, government support. It's a world where CEOs aren't the only ones calling the shots. In fact, there's a whole structure in place that manages everything from production lines to sales strategies.
Government schemes play a vital role in supporting manufacturing companies, especially in terms of funding and policy regulations. These schemes can provide the crucial edge companies need to stay competitive. So, who exactly holds the reins in a manufacturing setup? Well, let's get into the nitty-gritty of who does what and how they keep the wheels turning.
- Understanding the Hierarchy
- Key Players in Management
- Impact of Government Schemes
- Navigating Challenges
- Future of Manufacturing Leadership
Understanding the Hierarchy
A manufacturing company is like a well-oiled machine, made up of many gears working together. At the top of the chain, you typically find the CEO or president, who oversees the entire operation and sets the vision for the company. But the real action happens a few layers down.
Key Management Roles
- Chief Operations Officer (COO): They ensure that production runs smoothly, managing teams and resources to hit targets.
- Plant Manager: This person is on the ground in the factory, making sure daily operations meet quality standards and deadlines.
- Production Managers: They oversee specific areas of production, coordinating activities and ensuring efficiency.
- Quality Control Managers: These folks safeguard the quality of products, performing checks and implementing procedures to maintain standards.
The Role of Middle Management
Middle managers play a critical role. They're the bridge between leadership and the factory floor, translating strategic goals into action plans. They handle everything from scheduling shifts to tweaking production processes to improve efficiency.
Supporting Staff
Don't forget about HR, accounting, and IT departments. They might not be directly involved in making products, but they're essential to keeping the company running smoothly. HR manages hiring and workplace culture, accountants keep the finances in line, and IT ensures all the tech is working as it should.
Key Players in Management
When it comes to a manufacturing company, the management team is like the engine that keeps everything running smoothly. It's not just about top-level executives; it’s a team effort where every person plays a role. Let's break down who these key players are and what they do.
CEO and Executive Leadership
The CEO is usually the face of the company but behind those closed doors, they make some critical decisions. They set the vision and strategic goals, ensuring the company moves in the right direction. Then, there's the executive leadership team including the COO, CFO, and sometimes CTO, all supporting the CEO by focusing on operations, finances, and technology respectively.
Operations Management
Operations managers are essential players in the manufacturing industry. They're the ones who turn the wheels on the production line, ensuring everything ticks like a well-oiled machine. From managing workflow to maintaining production schedules, they make sure nothing falls behind.
Middle Management
Think of middle managers as the bridge between top management and the factory floor. They oversee smaller teams and help implement strategies. They might not be making big decisions but their role in executing plans is crucial.
Human Resources
We can't forget the folks in HR. They handle a vital part of management—recruiting and maintaining a satisfied workforce. They make sure you’ve got the right people for the job and that they’re happy doing it.
Supply Chain and Logistics
This crew manages the entire journey of parts and products from start to finish. They ensure that raw materials arrive on time and that finished products are sent to markets without delay. Efficient logistics are essential for keeping costs down and operations smooth.
Quality Control
Quality matters a lot in business management, especially in manufacturing. Quality control teams monitor production to ensure every item meets the required standards. Their checks and balances are key in maintaining the company’s reputation.
All these players contribute in unique ways to run a manufacturing company efficiently. They’re the ones who turn strategy into action, ensuring the company doesn’t just survive but thrives.
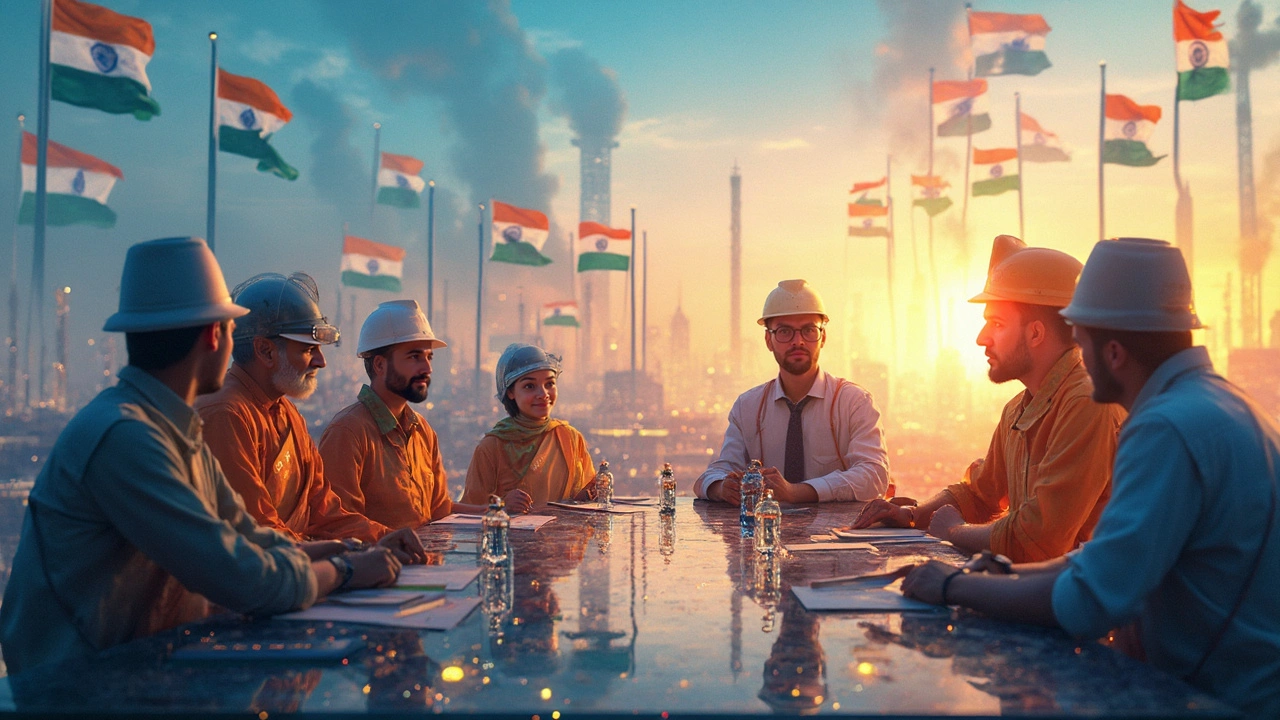
Impact of Government Schemes
When it comes to running a manufacturing company, understanding and leveraging government schemes can be a game-changer. These schemes are designed to boost the industrial sector and make it more competitive both locally and globally.
Funding and Financial Support
One of the biggest ways government schemes help is through financial support. Whether it's low-interest loans or grants, these resources can help manufacturing companies invest in new technologies and expand operations without being crippled by debt. For instance, the Production Linked Incentive (PLI) scheme in some regions offers incentives on incremental sales, giving manufacturers the push they need to increase output.
Policy Regulations and Compliance
Government schemes often come with regulations aimed at steering companies toward sustainable practices. These policies are not just red tape; they're often paired with benefits like tax breaks, making it easier for companies to comply while improving their bottom line.
Encouraging Innovation
Innovation is another area where government plays a critical role. Programs aimed at research and development can provide the resources manufacturers might not otherwise afford. A scheme may cover part of the R&D costs, allowing companies to innovate without the heavy financial burden.
Skill Development
The impact of government schemes isn't limited to what's produced. They also focus on who's producing. Many schemes offer skill development programs to ensure workers are trained in the latest technologies and practices. This is a win-win for employees seeking growth and employers needing skilled labor.
Overall, government schemes bridge gaps that could otherwise slow down progress in the manufacturing industry. By ensuring the necessary support structures are in place, these initiatives help businesses navigate a challenging landscape.
Navigating Challenges
Running a manufacturing company means constantly facing a slew of challenges. It's not just about keeping production going. There are hurdles like supply chain disruptions, labor issues, and regulatory compliance that you have to tackle daily.
Supply Chain Disruptions
Supply chain hiccups can throw a real wrench in the works. From natural disasters to global pandemics, these disruptions can delay operations considerably. Smart manufacturing leaders always have backup plans to quickly switch suppliers or find alternative routes when something goes sideways.
Regulatory Compliance
Keeping up with regulations is another major headache. Different regions have their own rules, and failing to comply can lead to hefty fines. Staying informed about the latest laws and adapting processes accordingly is something every company needs to get good at.
Labor Issues
Finding skilled workers is tougher than ever, and retaining them is just as hard. Offering competitive wages and comprehensive training programs can help keep your workforce stable.
Here’s a quick look at some labor trends:
Year | Labor Force Shortage (%) |
---|---|
2023 | 5.4 |
2024 | 6.1 |
2025 | 5.8 |
Utilizing Government Schemes
Government schemes often come to the rescue, offering financial support or training programs. But knowing how to navigate these opportunities is crucial. Always keep an eye out for new schemes that can give your company the edge it needs to thrive. Many businesses fail to even explore these options fully, missing out on valuable support.
In short, navigating challenges in the manufacturing sector is a never-ending task. But with well-defined strategies and utilizing the right support, companies can stay resilient in the face of adversity.
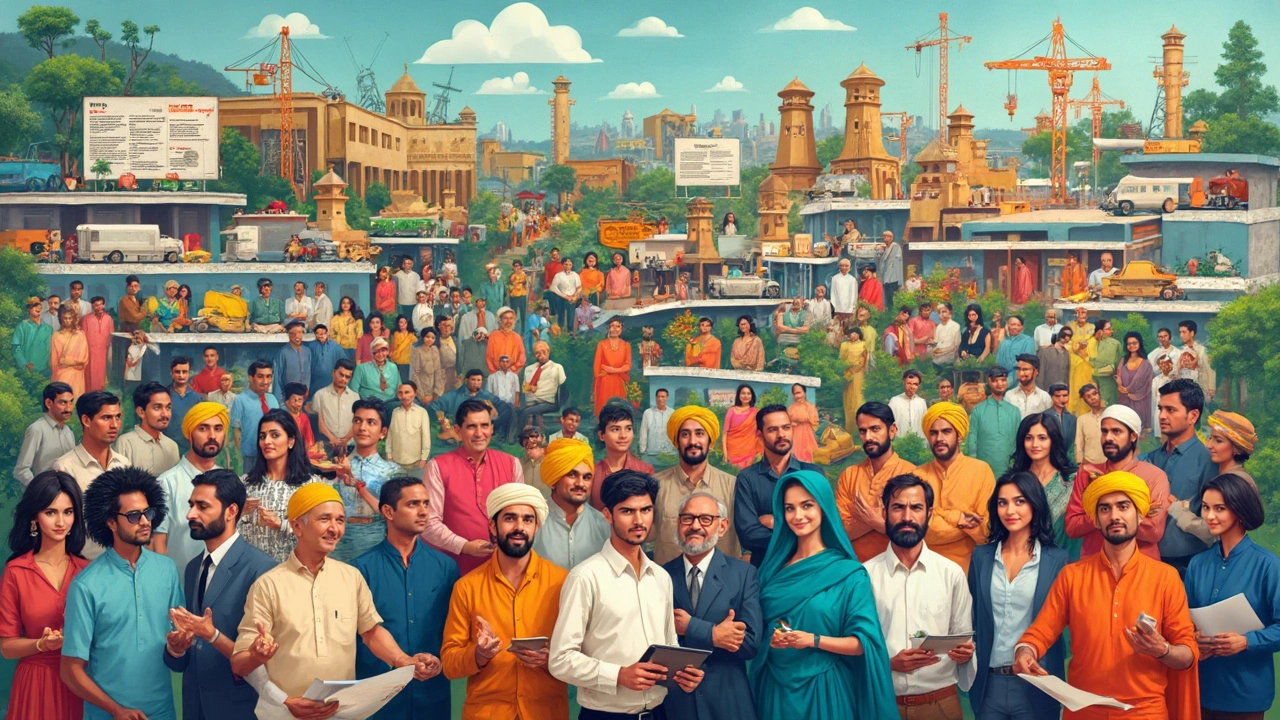
Future of Manufacturing Leadership
The world of manufacturing isn't standing still; it's advancing at a dizzying pace. As technology reshapes industries, those who run a manufacturing company will have to adapt quicker than ever. Future leaders will need to be more than just decision-makers; they'll have to be innovators, too.
With the rise of automation and AI, leaders must be tech-savvy. They're expected to understand digital tools that can optimize production, predict market needs, and manage supply chains efficiently. The days of manual data entry are fading, replaced by real-time analytics that give companies a competitive edge.
Adapting to Technological Changes
Leaders should not only embrace new technology but also drive cultural change within their organizations. This means fostering an environment that encourages innovation. It's about seeing technology as an enabler rather than a disruptor. Finding the right balance between human oversight and automated processes will be critical.
Government Schemes Shaping the Future
Government schemes are also evolving to support this change. Initiatives such as tax incentives for adopting green technologies and grants for workforce development are propelling companies forward. The challenge lies in navigating these opportunities effectively.
Building a Resilient Workforce
Another key focus for future leaders will be workforce development. As automation takes on more roles, jobs will transform but not necessarily vanish. Upskilling employees ensures they remain valuable contributors, and engaged workers tend to be more productive.
Prioritizing Sustainability
Sustainability isn't just a buzzword; it's becoming a deciding factor for consumers and investors. Future leaders who prioritize eco-friendly practices can not only appeal to environmentally conscious customers but also benefit from government incentives. Going green might mean fostering innovation in everything from product design to waste management.
Year | Automation Adoption |
---|---|
2025 | 45% |
2030 | 70% |
Ultimately, the future of manufacturing belongs to those who are willing to embrace change, harness technology, and lead with purpose. Those running tomorrow's manufacturing companies will not only make products but will shape the future of industry itself.