Setting up a small textile factory in India? It sounds like a big leap, but let's break it down! Starting with the basics, the cost depends on several factors like location, factory size, and the kind of textiles you're planning to produce. The cost of land isn't the same everywhere, and that's a big chunk of your budget right there. Picking a spot in an industrial area can save you some cash compared to prime locations in urban centers.
Now, let's talk about the machines. Depending on what you want to produce, the investment in machines ranges pretty widely. Whether you're eyeing cutting-edge tech or more traditional machinery will tweak that budget quite a bit. And of course, folks working the machines count, too. Labor costs vary across regions, with wages generally lower in rural areas compared to metropolitan cities. Understand these costs well and you’ll have a better grip on your budget.
- Understanding Land Costs
- Machinery and Equipment Costs
- Labor and Operational Expenses
- Government Incentives
- Location Strategy
Understanding Land Costs
One of the biggest considerations when setting up a small textile factory in India is land cost. It's a major factor that varies greatly across different regions. If you're thinking of planting your roots in a bustling city, prepare to shell out more compared to setting up shop in a more rural or industrial area. Take Bengaluru, for instance. Known as an industrial hub, it offers competitive prices in certain industrial zones, but in the main urban areas, prices shoot up significantly.
According to recent reports, industrial land in Tier 1 cities like Mumbai or Delhi can range between ₹2,000 to ₹10,000 per square foot. But, if your sights are set on a Tier 2 city like Coimbatore or Surat, you might snag a deal at ₹500 to ₹1,500 per square foot. Industrial parks and special economic zones (SEZs) offer added benefits like tax incentives but come with an extra cost for amenities and infrastructure.
When budgeting for land, keep an eye on the connectivity and proximity to raw material suppliers and transport hubs. Being closer can cut transportation costs significantly, giving your factory operations a financial edge. Also, consider future growth. Will the location allow you to expand your operations smoothly in the future?
Some entrepreneurs are now even considering leasing land from the government or private developers. It can be a cost-effective option to get started without a hefty upfront payment. However, be aware of the lease terms and conditions, as they can impact your long-term business strategy.
Going through local government policies and incentives is vital. Some states offer subsidies or rebates for setting up manufacturing units, and these can lessen the overall financial burden. Exploring these options might just lighten your startup costs significantly!
Machinery and Equipment Costs
Alright, here’s where the fun begins! The cost of machinery and equipment is a biggie when setting up a small textile factory in India. The kind of textiles you plan on producing will dictate what machines you need.
For instance, if you’re diving into weaving, you're looking at buying power looms or shuttleless looms. Power looms are cheaper but might not be as efficient as their modern shuttleless cousins. The price tag for these can vary from INR 2 lakh to INR 10 lakh or more depending on the level of automation.
If garment manufacturing is your thing, then you’ll need machines like sewing machines, fabric cutting machines, and embroidery machines. Each sewing machine can range from INR 10,000 for a basic model to over INR 1 lakh for advanced versions that can handle heavy-duty jobs.
Type of Machinery | Estimated Cost (INR) |
---|---|
Power Loom | 2 to 10 lakh |
Shuttleless Loom | 7 to 25 lakh |
Basic Sewing Machine | 10,000 to 1 lakh |
Fabric Cutting Machine | 50,000 to 5 lakh |
It doesn't end here, though. You might need finishing machines like washing and dyeing equipment if your production plan includes those processes. These can add significantly to your budget, often reaching into the high lakhs, depending on capacity and technology.
Sometimes, you can find good second-hand equipment at a fraction of the price, but be sure to check the condition carefully to avoid costly repairs down the line. Also, factor in import duties if you're considering bringing in machines from abroad. That's an extra cost some folks forget about!
Planning your textile factory cost intelligently, by investing in the right mix of machinery and knowing where to save, can set you up for success from the get-go.
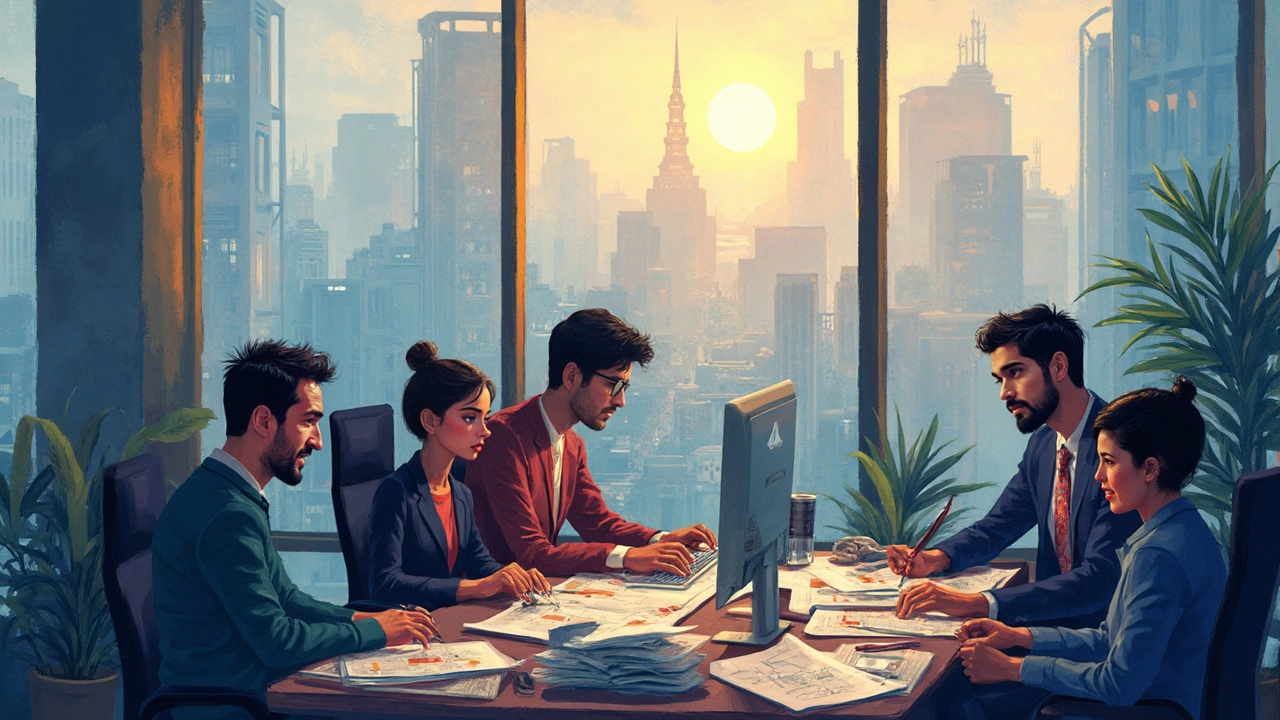
Labor and Operational Expenses
When setting up a small textile factory in India, labor costs are a key part of your budget. Thanks to a large and varied workforce, labor costs here are often lower compared to many other countries. That said, wages vary widely depending on the factory's location. For example, workers in metropolitan areas might demand higher pay than those in rural regions due to the higher cost of living.
To give you a better idea, the average monthly wage for a textile worker in a smaller city might range from INR 8,000 to INR 12,000. In more urbanized areas, these wages can go upwards. But it's not just about wages; managing workers effectively and maintaining positive relations is crucial. According to a report by PwC India, "Employing technology to optimize labor productivity can significantly lower operational costs while enhancing output quality."
Operational expenses don't stop at salaries. You also need to consider utilities like electricity and water, crucial for running those machines. Electricity alone can gobble up a significant portion of operational costs, especially if you're operating energy-intensive equipment.
On top of these, regular maintenance of machinery is essential to keep everything running smoothly. Neglecting this can lead to downtime, which directly impacts your production efficiency. A handy tip: have a small fund set aside specifically for unexpected repairs and maintenance.
Ultimately, understanding these costs and managing them wisely makes all the difference between breaking even and turning a profit. Focus on hiring skilled labor, optimize operations, and always keep an eye on those utility bills.
Government Incentives
Who doesn't like a little help from the government, right? If you're planning to dive into the textile manufacturing scene in India, there are quite a few incentives to keep in mind. The Indian government offers several schemes to promote the textile industry, aimed at making it more competitive globally while also supporting local businesses.
One of the most popular schemes is the Amended Technology Upgradation Fund Scheme (ATUFS). Under this scheme, you can get a capital subsidy on the purchase of new machinery, making it easier to keep your textile factory efficient and up-to-date with the latest tech.
Additionally, if you're setting up a factory in a special economic zone (SEZ), you're likely in for some tax benefits. SEZs often provide exemptions from customs duties and offer easier regulatory compliance, which can save you a bunch of time and money.
Another perk in certain states is power tariff subsidies. While these vary from one state to another, understanding where you can get cheap electricity could significantly cut down your operational expenses.
Don't forget to check out state-specific incentives as well. States like Gujarat, Maharashtra, and Tamil Nadu have their own packages tailored for textile units. These can include benefits like reimbursements on freight costs and employment subsidies.
Here's a quick look at some of the incentives:
- Capital subsidy under ATUFS.
- Tax exemptions in SEZs.
- Power tariff subsidies.
- State-specific benefits like freight and employment subsidies.
Remember, though, these benefits often come with specific conditions, so it pays to do a bit of homework or consult a local expert before making any commitments.
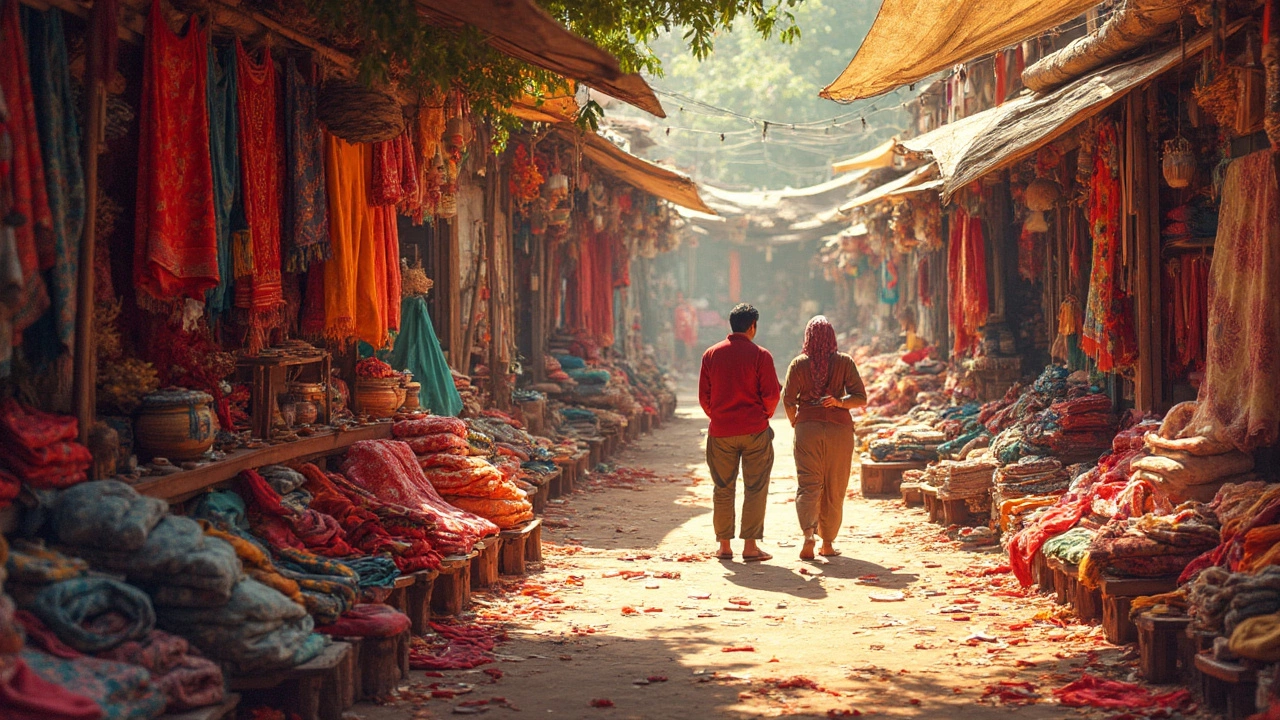
Location Strategy
Choosing the right location for your textile factory is like finding the right spot for your dream home—it's crucial and can make all the difference. You have to think about the land costs, but it's also about logistics. Being close to both your suppliers and markets can really save on those pesky transport costs.
Industrial parks or special economic zones (SEZs) in India might have cheaper land costs compared to urban areas. Plus, these areas often offer better infrastructure, like roads and reliable electricity, which is essential when you're running all those machines.
Now, a bit about labor—different states in India offer varied labor costs, which could either be a boon or a burden. For example, places in Tamil Nadu and Gujarat have a rich pool of skilled textile workers and competitive labor rates, making them popular hotspots for textile manufacturing.
You should also keep an eye out for government incentives. Certain regions provide tax breaks or subsidies to boost small factory setups. This can be a serious money-saver, so it pays to do your research or even talk to a local consultant who knows the ropes.
State | Average Land Cost (INR per sq ft) | Skilled Labor Availability |
---|---|---|
Tamil Nadu | 1200-1500 | High |
Gujarat | 1100-1400 | High |
Maharashtra | 1300-1600 | Medium |
Ultimately, your location strategy should not just focus on costs but also on how it aligns with your business goals. With the right strategy, your small textile factory could be well on its way to success in the bustling India textile industry.